Optimisation des activités de production : Stratégies et bonnes pratiques industrielles
Introduction
Dans le domaine industriel, l’optimisation des activités de production revêt une importance capitale pour assurer la compétitivité et la pérennité des entreprises. Ce processus complexe vise à maximiser l’efficacité des opérations tout en minimisant les coûts et les délais.
Pour comprendre l’optimisation des activités de production, il est essentiel de saisir sa définition et ses objectifs. Contrairement à une simple amélioration des processus, l’optimisation implique une approche systématique et intégrée visant à atteindre les niveaux optimaux de performance. Cela comprend l’optimisation des flux de travail, des ressources et des technologies utilisées dans le processus de production.
Les défis rencontrés dans l’optimisation des activités de production sont multiples et variés. Parmi les principaux obstacles figurent les contraintes de capacité, les fluctuations de la demande, les variations de la qualité des matières premières et les contraintes budgétaires. Par exemple, une entreprise manufacturière peut être confrontée à des goulots d’étranglement dans sa chaîne de production en raison d’une capacité limitée d’une machine critique.
Pour surmonter ces défis, les entreprises déploient un éventail de stratégies et de bonnes pratiques. Parmi les approches les plus couramment utilisées figurent les principes du Lean Manufacturing, qui visent à éliminer les gaspillages et à améliorer la flexibilité des processus. Par exemple, Toyota a révolutionné l’industrie automobile en mettant en œuvre des concepts Lean, réduisant ainsi les délais de production et les coûts de manière significative.
L’optimisation des activités de production constitue un enjeu majeur pour les entreprises industrielles souhaitant rester compétitives dans un environnement en constante évolution. Dans les sections suivantes de cet article, nous explorerons en détail les stratégies et les bonnes pratiques essentielles à une optimisation réussie, ainsi que les mesures de performance permettant d’évaluer l’efficacité des initiatives d’optimisation.
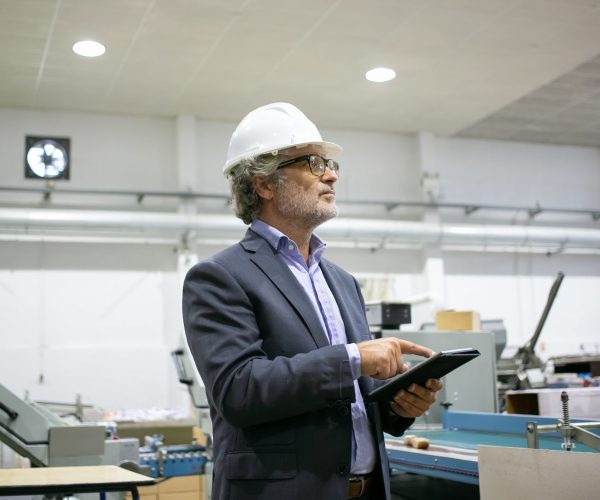
Toute votre gestion d'entreprise
dans un seul outil.
Les principaux défis de l'optimisation des activités de production
L’optimisation des activités de production est confrontée à une multitude de défis complexes et interdépendants. En ma qualité d’expert en transformation industrielle, j’ai constaté que la compréhension approfondie de ces défis est essentielle pour élaborer des stratégies efficaces d’optimisation.
L’un des défis les plus courants est la gestion des contraintes de capacité. Les entreprises peuvent rencontrer des difficultés à maintenir un équilibre entre la demande fluctuante du marché et leurs capacités de production. Par exemple, une entreprise alimentaire peut se retrouver confrontée à des pics de demande saisonniers, nécessitant une flexibilité accrue de sa chaîne de production pour répondre à la demande sans compromettre la qualité.
Par ailleurs, les fluctuations de la demande constituent un défi majeur pour l’optimisation des activités de production. Les prévisions de la demande peuvent être imprécises, ce qui entraîne des problèmes de surstockage ou de pénurie de produits. Pour atténuer ces fluctuations, les entreprises doivent mettre en œuvre des stratégies de gestion de la demande et des stocks efficaces, telles que la planification collaborative avec les fournisseurs et l’utilisation de techniques d’optimisation des stocks.
Un autre défi crucial est la gestion de la qualité des matières premières et des produits finis. Les variations de la qualité des matières premières peuvent affecter la stabilité des processus de production et la qualité des produits finis. Par exemple, une entreprise chimique doit faire face à des variations de la composition des matières premières, ce qui peut influencer la réaction chimique et la qualité du produit final.
Enfin, les contraintes budgétaires imposent des limites aux investissements dans de nouvelles technologies et des améliorations des processus. Les entreprises doivent donc trouver un équilibre entre l’optimisation des activités de production et la rentabilité financière. Par exemple, une entreprise manufacturière peut être confrontée à des pressions pour réduire ses coûts de production tout en maintenant des niveaux élevés de qualité et de satisfaction client.
En somme, l’optimisation des activités de production est un défi complexe qui nécessite une approche stratégique et intégrée pour surmonter les obstacles rencontrés. Dans les sections suivantes, nous explorerons les stratégies et les bonnes pratiques spécifiques permettant de relever ces défis et d’optimiser efficacement les activités de production.
Stratégies clés pour optimiser les activités de production
Dans le cadre de l’optimisation des activités de production, plusieurs stratégies clés peuvent être mises en œuvre pour maximiser l’efficacité opérationnelle et atteindre les objectifs de performance. En tant qu’expert en transformation industrielle, j’ai observé l’impact positif de ces stratégies sur la compétitivité et la rentabilité des entreprises. Une des stratégies les plus importantes est l’adoption des principes du Lean Manufacturing. Cette approche vise à éliminer les gaspillages et à optimiser les processus de production pour une utilisation plus efficace des ressources. Par exemple, une entreprise automobile peut mettre en œuvre des outils tels que le kaizen (amélioration continue), le 5S (organisation du poste de travail) et le kanban (système de gestion des flux) pour réduire les temps d’attente, minimiser les stocks et augmenter la productivité.
Parallèlement, l’intégration de technologies de pointe telles que l’Internet des Objets (IoT) et l’Intelligence Artificielle (IA) offre de nouvelles possibilités d’optimisation des activités de production. Par exemple, des capteurs IoT peuvent être utilisés pour surveiller en temps réel les performances des machines et prévenir les pannes avant qu’elles ne surviennent, tandis que des algorithmes d’IA peuvent analyser de grandes quantités de données pour optimiser les processus de production et prévoir la demande.
La gestion efficace de la chaîne d’approvisionnement est également cruciale pour optimiser les activités de production. Une coordination étroite avec les fournisseurs et les partenaires permet de réduire les délais de livraison, d’optimiser les niveaux de stock et d’assurer la disponibilité des matières premières au bon moment et au bon endroit. Par exemple, une entreprise de fabrication de produits électroniques peut mettre en place des partenariats stratégiques avec des fournisseurs de composants clés pour garantir une chaîne d’approvisionnement fluide et réactive.
En conclusion, l’optimisation des activités de production repose sur la mise en œuvre de stratégies adaptées aux besoins spécifiques de chaque entreprise. En combinant les principes du Lean Manufacturing, les technologies de pointe et une gestion efficace de la chaîne d’approvisionnement, les entreprises peuvent améliorer leur compétitivité, leur flexibilité et leur rentabilité sur le marché industriel.
Bonnes pratiques pour une efficacité opérationnelle maximale
Au-delà des stratégies globales, la mise en place de bonnes pratiques spécifiques joue un rôle crucial dans l’optimisation des activités de production. En tant qu’expert en transformation industrielle, j’ai identifié plusieurs pratiques essentielles qui contribuent à une efficacité opérationnelle maximale.
Tout d’abord, une planification et un ordonnancement rigoureux des opérations de production sont indispensables pour optimiser l’utilisation des ressources et minimiser les temps d’arrêt. Cela implique d’établir des calendriers de production réalistes en fonction des capacités de l’entreprise, des prévisions de demande et des contraintes de la chaîne d’approvisionnement. Par exemple, une entreprise agroalimentaire peut utiliser des outils de planification avancés pour optimiser la production en fonction des saisons et des cycles de croissance des cultures.
Ensuite, le contrôle de la qualité occupe une place centrale dans l’optimisation des activités de production. La mise en œuvre de processus de contrôle qualité rigoureux permet de détecter et de corriger les défauts dès leur apparition, réduisant ainsi les rebuts et les retouches coûteuses. Par exemple, une entreprise pharmaceutique peut mettre en place des inspections visuelles et des tests de conformité tout au long du processus de fabrication pour garantir la qualité et la sécurité de ses produits.
Par ailleurs, une gestion proactive des ressources humaines et matérielles est indispensable pour maintenir un niveau élevé de performance opérationnelle. Cela implique de recruter, former et motiver les employés, ainsi que de maintenir et moderniser les équipements de production de manière régulière. Par exemple, une entreprise de fabrication mécanique peut investir dans des programmes de formation continue pour ses employés afin de maintenir leurs compétences à jour et d’optimiser l’utilisation des machines et des outils.
En résumé, la mise en œuvre de bonnes pratiques telles que la planification et l’ordonnancement efficaces, le contrôle de la qualité et la gestion proactive des ressources est essentielle pour atteindre une efficacité opérationnelle maximale dans les activités de production. Ces pratiques contribuent à réduire les coûts, à améliorer la qualité des produits et à renforcer la compétitivité des entreprises sur le marché industriel.
Mesurer et évaluer la performance des activités de production
Dans le cadre de l’optimisation des activités de production, il est indispensable de mettre en place des indicateurs de performance pertinents pour mesurer et évaluer l’efficacité des opérations. En tant qu’expert en transformation industrielle, j’accorde une grande importance à cette étape cruciale, car elle permet d’identifier les domaines à améliorer et de suivre les progrès réalisés dans l’optimisation des activités de production.
Un des indicateurs clés de performance (KPI) largement utilisé dans le domaine industriel est le taux de rendement global (TRG), également connu sous le nom d’OEE (Overall Equipment Effectiveness). Le TRG mesure l’efficacité globale des équipements de production en prenant en compte trois facteurs : la disponibilité (temps de fonctionnement réel par rapport au temps prévu), le rendement (quantité de produits fabriqués par rapport à la capacité maximale) et la qualité (pourcentage de produits conformes par rapport à la production totale). Par exemple, une entreprise automobile peut utiliser le TRG pour évaluer la performance de ses lignes de production et identifier les causes des temps d’arrêt et des baisses de rendement.
En plus du TRG, d’autres KPI peuvent être utilisés pour mesurer des aspects spécifiques des activités de production, tels que le taux de rotation des stocks, le temps de cycle, le taux de rebuts ou encore le respect des délais de livraison. Par exemple, une entreprise de fabrication de produits électroniques peut suivre le taux de rebuts pour évaluer l’efficacité de ses processus de fabrication et mettre en place des actions correctives pour réduire les défauts et les gaspillages.
Outre la mesure des KPI, l’utilisation d’outils d’analyse de données joue un rôle essentiel dans l’évaluation de la performance des activités de production. Les systèmes de gestion intégrés (ERP) et les logiciels de Business Intelligence (BI) permettent de collecter, analyser et visualiser les données opérationnelles en temps réel, facilitant ainsi la prise de décision et l’identification des tendances et des opportunités d’amélioration. Par exemple, une entreprise agroalimentaire peut utiliser un système ERP pour suivre les niveaux de stock, les coûts de production et les performances des fournisseurs, et ainsi optimiser sa chaîne d’approvisionnement et sa planification de production.
En conclusion, la mesure et l’évaluation de la performance des activités de production sont des étapes cruciales dans le processus d’optimisation industrielle. En utilisant des KPI pertinents et des outils d’analyse de données avancés, les entreprises peuvent identifier les inefficacités, prendre des décisions éclairées et mettre en œuvre des actions correctives pour améliorer continuellement leurs opérations et leur compétitivité sur le marché industriel.
Conclusion : L'avenir de l'optimisation des activités de production
En conclusion, l’optimisation des activités de production est un processus complexe et continu qui joue un rôle crucial dans la compétitivité et la pérennité des entreprises industrielles. Au cours de cet article, nous avons exploré les défis rencontrés dans l’optimisation, les stratégies clés et les bonnes pratiques pour améliorer l’efficacité opérationnelle, ainsi que les méthodes de mesure et d’évaluation de la performance.
L’avenir de l’optimisation des activités de production réside dans l’intégration de technologies émergentes telles que l’Internet des Objets (IoT), l’Intelligence Artificielle (IA) et la robotique avancée. Ces technologies permettent une automatisation accrue des processus, une optimisation en temps réel et une prise de décision basée sur les données, contribuant ainsi à une productivité accrue, une réduction des coûts et une meilleure qualité des produits.
Parallèlement, la durabilité et la responsabilité sociale seront des éléments de plus en plus importants dans l’optimisation des activités de production. Les entreprises devront intégrer des pratiques éco-responsables dans leurs opérations, telles que la réduction des déchets, l’utilisation d’énergies renouvelables et la promotion de conditions de travail sûres et équitables. Ces initiatives non seulement répondent aux attentes croissantes des consommateurs et des régulateurs en matière de durabilité, mais elles contribuent également à renforcer la réputation et la marque de l’entreprise.
Enfin, la collaboration et l’innovation seront essentielles pour relever les défis futurs de l’optimisation des activités de production. Les entreprises doivent encourager une culture de l’innovation et de l’amélioration continue, en favorisant l’échange d’idées et de meilleures pratiques à travers des réseaux de partenaires et d’experts. En travaillant ensemble pour relever ces défis, les entreprises peuvent prospérer dans un environnement industriel en constante évolution et assurer leur succès à long terme.
Ces articles pourraient vous intéresser
En savoir plus
Retrouvez l’ensemble de nos ressources pour accroître vos connaissances sur l’ERP pour le domaine industriel.
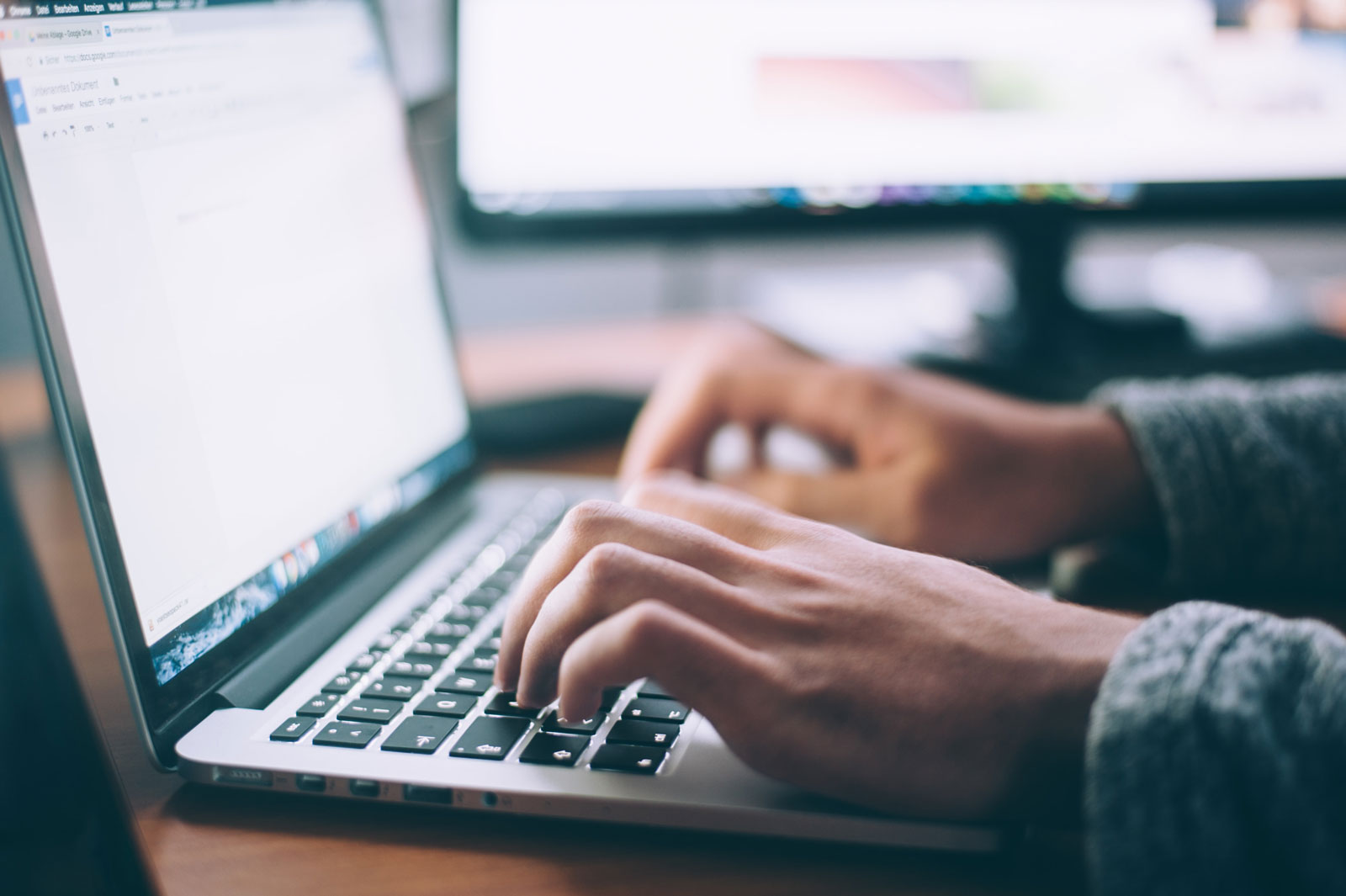
Retrouvez l’ensemble des réponses fonctionnelles de l’ERP Open-Prod aux différents secteurs industriels.
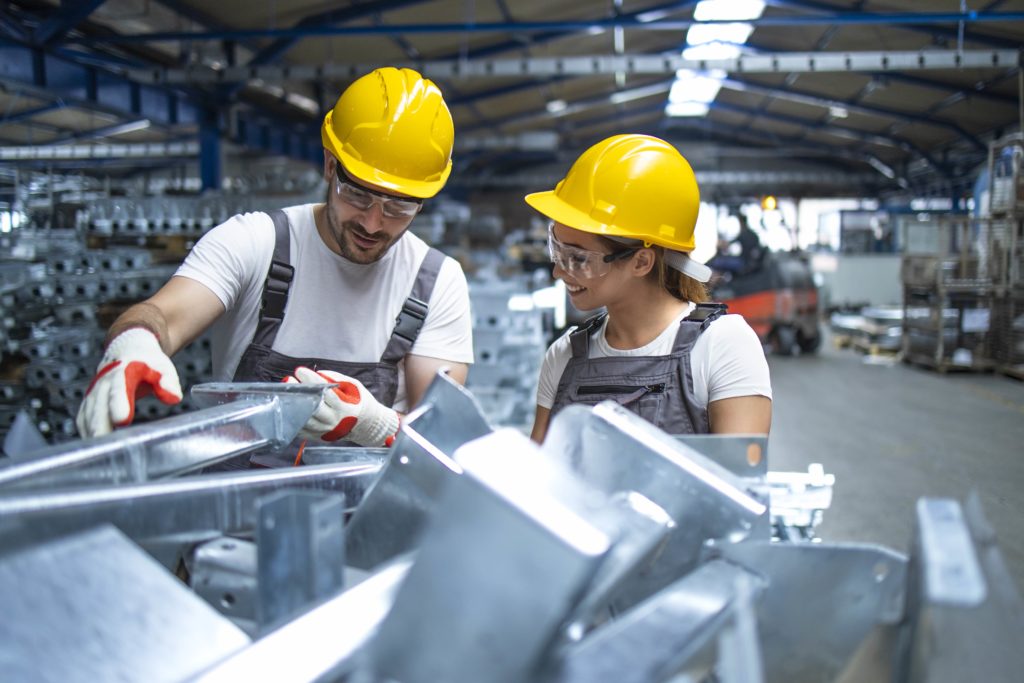
Découvrez les +200 modules d’Open-Prod conçus pour répondre aux besoins des entreprises industrielles.
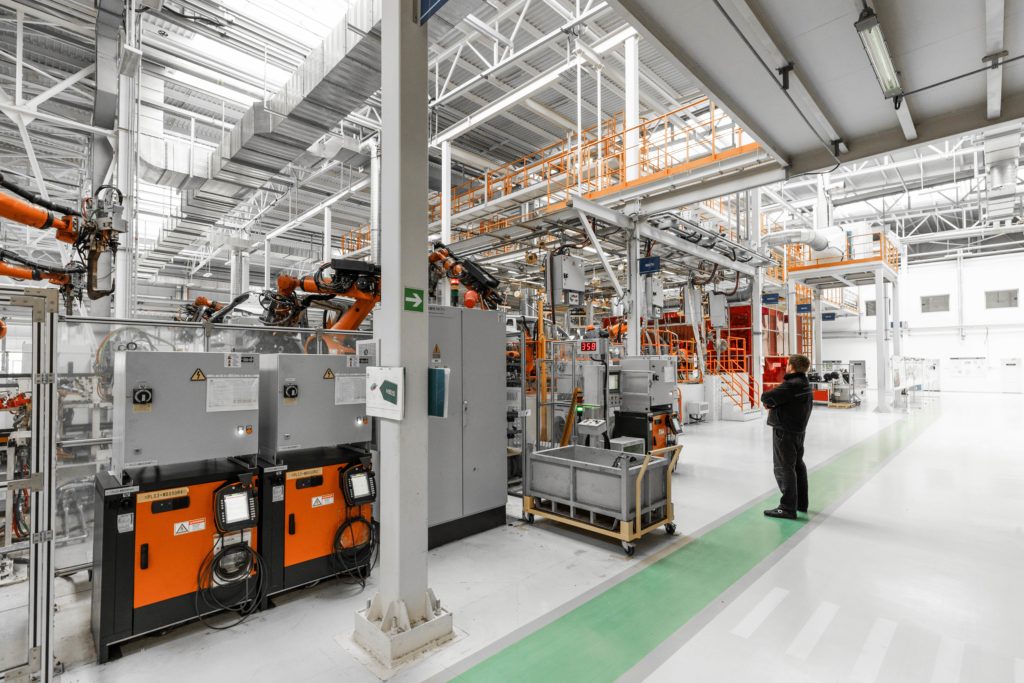