Le concept du chemin capacitaire : définitions et enjeux
Le concept du chemin capacitaire
Les entreprises doivent non seulement maximiser leurs performances, mais aussi anticiper les transformations du marché et ajuster en permanence leurs stratégies. C’est dans ce cadre que le chemin capacitaire s’impose comme une méthode structurée et innovante, conçue pour aligner les ressources internes sur des objectifs stratégiques à long terme.
Le chemin capacitaire repose sur une série d’étapes méthodiques permettant d’identifier, planifier et optimiser les capacités industrielles.
Étape 1 : Cartographier les capacités existantes
Avant toute optimisation ou transformation, une entreprise doit commencer par comprendre et évaluer ses ressources. La cartographie des capacités permet de dresser un état des lieux précis des moyens disponibles, qu’ils soient humains, technologiques ou matériels. Cette démarche analytique constitue le socle sur lequel repose tout chemin capacitaire.
L’identification des ressources commence par une analyse détaillée des infrastructures de production, des compétences des équipes et des outils technologiques. Par exemple, l’utilisation de solutions telles qu’un logiciel, offre une vue centralisée des données en temps réel, facilitant ainsi l’évaluation des performances et des zones de blocage. Ces outils permettent de collecter, d’organiser et de visualiser les informations nécessaires pour un diagnostic complet.
Une fois les données collectées, il est essentiel de repérer les goulets d’étranglement. Ces points critiques, qu’ils soient dus à des processus inefficaces, à une sous-utilisation des équipements ou à des failles organisationnelles, peuvent freiner la productivité globale. L’analyse des flux de valeur (Value Stream Mapping) est ici particulièrement pertinente : elle permet de représenter visuellement l’ensemble des étapes de production et d’identifier les segments à optimiser.
L’évaluation des forces et des faiblesses internes peut être enrichie par une analyse SWOT, qui croise les ressources internes avec les opportunités et menaces externes. Une telle méthode aide à aligner les capacités de l’entreprise sur les exigences du marché et à préparer des stratégies adaptées.
L’apport des technologies numériques transforme également la cartographie des capacités. En intégrant des outils d’analyse avancée et des plateformes connectées, les entreprises peuvent surveiller en continu l’état de leurs équipements et anticiper les besoins en maintenance. Cette approche proactive minimise les interruptions et garantit une disponibilité optimale des ressources.
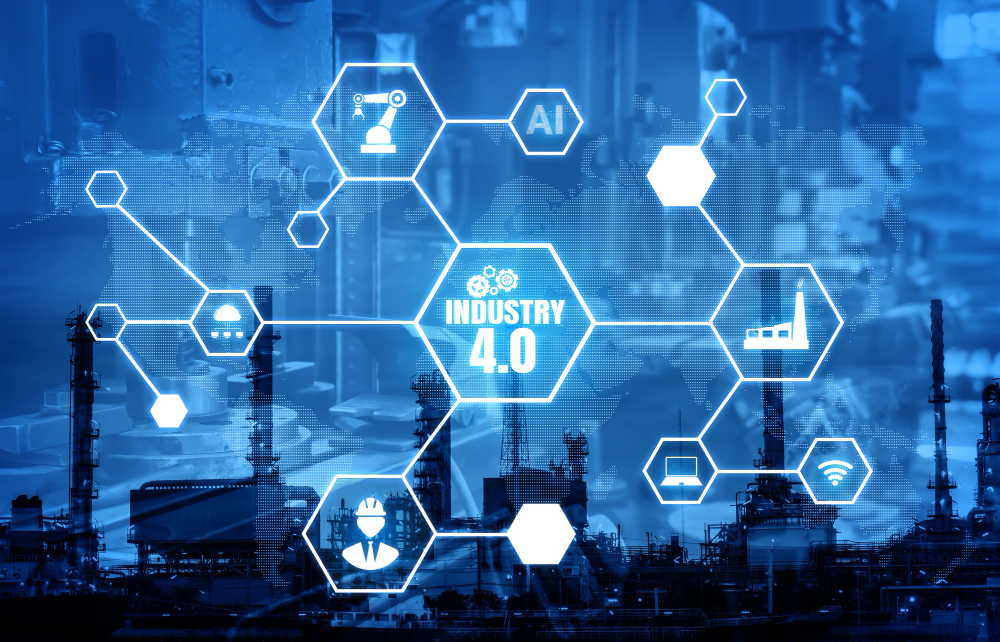
Étape 2 : Anticiper grâce à la planification stratégique
Une fois les capacités existantes cartographiées, l’étape suivante consiste à anticiper les évolutions possibles du marché et de l’environnement industriel. La planification capacitaire stratégique repose sur la construction de scénarios permettant d’anticiper les fluctuations de la demande, les innovations technologiques et les perturbations potentielles. Cette démarche pro-active assure que l’entreprise reste agile et compétitive face aux incertitudes.
La planification basée sur des scénarios débute par l’identification des principales variables pouvant influencer l’activité : les tendances du marché, les progrès technologiques, les contraintes environnementales et les dynamiques de la concurrence. Par exemple, dans une industrie où les cycles de vie des produits se raccourcissent, intégrer des outils d’analyse prédictive, comme ceux disponibles dans les ERP modernes tels qu’Open-Prod, peut offrir un avantage décisif en simulant différents scénarios de production et de demande.
Ces scénarios doivent également prendre en compte les ruptures technologiques susceptibles de redéfinir les besoins en capacités. L’introduction de technologies comme la fabrication additive ou les robots collaboratifs peut imposer une reconfiguration des chaînes de production. La méthode des scénarios prospectifs, qui consiste à modéliser plusieurs futurs possibles (croissance rapide, stagnation ou crise), offre une structure pour évaluer ces impacts.
Pour garantir la robustesse de cette planification, l’utilisation de technologies numériques avancées est essentielle. Les outils d’intelligence artificielle et de machine learning permettent de traiter de vastes quantités de données pour affiner les prévisions. Par exemple, une entreprise opérant dans un secteur sujet à des variations saisonnières peut utiliser ces solutions pour ajuster ses capacités en temps réel en fonction des prévisions de la demande.
La planification capacitaire ne se limite pas à répondre aux défis actuels ; elle vise également à créer des opportunités. En anticipant les besoins du marché et les transformations technologiques, l’entreprise peut adapter ses capacités pour répondre aux exigences futures, tout en optimisant les ressources nécessaires.
Étape 3 : Améliorer les performances par l’optimisation continue
Une fois les capacités cartographiées et les scénarios stratégiques définis, l’optimisation continue devient la pierre angulaire d’un chemin capacitaire efficace. Cette phase vise à maximiser l’efficacité des processus, à réduire les inefficacités et à garantir que l’entreprise maintienne un avantage compétitif durable dans un environnement changeant.
L’optimisation continue repose sur des principes éprouvés comme le Lean Management, qui met l’accent sur l’élimination des gaspillages et l’amélioration des flux. Les approches telles que le Kanban et le Juste-à-Temps (JAT) permettent d’ajuster les niveaux de production en fonction de la demande réelle, évitant ainsi les stocks inutiles et les délais coûteux. Ces méthodes, associées à des outils numériques comme les ERP intégrés, facilitent la fluidité des opérations en alignant les ressources sur les besoins immédiats.
L'intégration des technologies connectées est un des leviers majeurs de cette optimisation. Les capteurs IoT et les systèmes de surveillance en temps réel fournissent des données précises sur la performance des équipements et des chaînes de production. Par exemple, un capteur installé sur une machine peut détecter les variations anormales de performance, permettant une maintenance préventive avant qu’un problème ne devienne critique. Ces ajustements en temps réel réduisent non seulement les temps d’arrêt, mais augmentent également la productivité globale.
En parallèle, l’utilisation de plateformes collaboratives permet une meilleure coordination entre les équipes et les différentes étapes de production. Ces plateformes, souvent intégrées à des systèmes GPAO ou ERP, offrent une visibilité accrue sur les processus, permettant aux responsables de prendre des décisions éclairées et d’ajuster les priorités en fonction des besoins stratégiques.
L’optimisation continue passe également par la formation et l’implication des collaborateurs. En adoptant une approche participative, où chaque employé est encouragé à identifier des opportunités d’amélioration, l’entreprise peut bénéficier d’un flux constant d’innovations. Par exemple, intégrer des outils visuels comme les tableaux de bord interactifs facilite la communication des objectifs et la transparence des résultats, renforçant ainsi l’engagement des équipes.
Toute votre gestion d'entreprise
dans un seul outil.
Étape 4 : Automatisation et transformation numérique
La révolution numérique et l’automatisation s’imposent comme des piliers incontournables pour les entreprises industrielles cherchant à optimiser leurs capacités. En s’appuyant sur des technologies avancées, ces innovations transforment non seulement les processus internes, mais aussi les modèles opérationnels.
L’automatisation répond à la nécessité de réduire les tâches répétitives et d’augmenter la productivité. Les robots collaboratifs, ou cobots, illustrent parfaitement cette mutation. Intégrés aux chaînes de production, ils assistent les opérateurs dans les tâches complexes, alliant précision mécanique et expertise humaine. Résultat : des cycles de production accélérés et une qualité améliorée, tout en renforçant la sécurité des employés.
Parallèlement, la transformation numérique redéfinit le pilotage industriel. Des solutions dédiées aux entreprises industrielles, telles que l’ERP Open-Prod, jouent un rôle central dans cette mutation. En offrant une vision en temps réel des stocks, des capacités de production et des ressources disponibles, ces solutions permettent une gestion fine des processus.
L’Industrie 4.0 et des technologies dédiées, comme les jumeaux numériques, permettent aux entreprises de franchir un cap supplémentaire dans leur recherche d’optimisation. Ces répliques virtuelles des infrastructures industrielles permettent de simuler des scénarios complexes sans interrompre les opérations. Une entreprise peut, par exemple, modéliser une montée en charge soudaine pour tester la résilience de ses capacités et ajuster ses stratégies.
La fabrication additive, souvent qualifiée d’impression 3D, joue également un rôle crucial. En rendant possible la production à la demande de pièces spécifiques, elle réduit les stocks et accélère les délais de mise sur le marché. Associée à une approche locale de la fabrication, elle favorise une logistique allégée et une empreinte environnementale réduite.
La fabrication additive, souvent qualifiée d’impression 3D, joue également un rôle crucial. En rendant possible la production à la demande de pièces spécifiques, elle réduit les stocks et accélère les délais de mise sur le marché. Associée à une approche locale de la fabrication, elle favorise une logistique allégée et une empreinte environnementale réduite.
Étape 5 : Évaluation et ajustement du chemin capacitaire
La réussite d’une stratégie capacitaire repose sur sa capacité à évoluer. L’évaluation régulière des performances et l’ajustement des processus en fonction des objectifs stratégiques sont des étapes cruciales pour garantir la pérennité et la pertinence du chemin capacitaire.
Cette évaluation s’appuie sur des indicateurs clés de performance (KPI) rigoureusement définis. Parmi les métriques les plus courantes figurent le taux d’utilisation des équipements, les délais de production, les coûts opérationnels ou encore les niveaux de stock. Ces données offrent une vue d’ensemble des résultats obtenus et permettent d’identifier les points de friction ou les zones nécessitant des améliorations.
Les boucles de rétroaction sont essentielles pour intégrer ces données dans une logique d’amélioration continue. En recueillant les retours des collaborateurs, des clients et des partenaires, l’entreprise peut affiner ses processus et mieux aligner ses capacités sur les attentes du marché. Par exemple, un suivi régulier des retours clients sur les délais de livraison peut mettre en lumière des inefficacités dans la chaîne logistique, invitant ainsi à des ajustements spécifiques.
La mise en œuvre de cycles PDCA (Plan-Do-Check-Act) structure ces efforts. Cette méthodologie itérative permet de tester des solutions, d’en analyser les impacts, puis d’affiner les stratégies en conséquence. Elle s’intègre parfaitement aux outils numériques modernes, tels que les ERP et les plateformes de collaboration, qui facilitent la collecte et l’analyse des données en temps réel.
Les audits réguliers jouent également un rôle clé dans cette étape. Ils permettent de comparer les objectifs initialement fixés avec les résultats obtenus, tout en identifiant les écarts à combler. Cette approche garantit une gestion proactive des capacités, évitant ainsi que les inefficacités ne s’installent durablement.
Au-delà des processus, cette étape inclut une réflexion stratégique sur l’adéquation des capacités avec les transformations du marché. L’émergence de nouvelles technologies ou de nouveaux modèles économiques peut exiger des révisions plus profondes, comme l’adoption de solutions d’Industrie 4.0 ou la réallocation de ressources vers des secteurs en croissance.
Etape 6 : Les bénéfices concrets du chemin capacitaire
Adopter une stratégie basée sur le chemin capacitaire ne se résume pas à améliorer la gestion des ressources : c’est une transformation qui impacte directement la compétitivité et la résilience des entreprises industrielles. Les résultats obtenus témoignent de l’efficacité de cette approche structurée et méthodique.
L’un des premiers bénéfices est la réduction des coûts opérationnels. En optimisant les flux de production, en éliminant les inefficacités et en intégrant des outils technologiques avancés comme les ERP ou les systèmes de GPAO, les entreprises réduisent sensiblement leurs dépenses. Par exemple, la suppression des stocks inutiles ou la mise en place de solutions de maintenance prédictive permet de limiter les pertes et d’améliorer la rentabilité.
Cette stratégie offre également une flexibilité accrue, en réponse aux évolutions rapides des cycles économiques et les demandes des clients. Dès lors, la capacité d’une entreprise à ajuster ses capacités en temps réel devient un atout stratégique. L’utilisation de technologies connectées et de plateformes collaboratives facilite cette agilité, permettant une adaptation rapide aux fluctuations du marché.
En anticipant les évolutions grâce à des outils prédictifs, les entreprises se prémunissent également contre les interruptions de production ou les pénuries de ressources. Cette approche proactive renforce leur résilience face aux crises, qu’il s’agisse de perturbations dans les chaînes d’approvisionnement ou de changements imprévus dans la demande.
L’impact positif sur la compétitivité des entreprises est indéniable. En s’appuyant sur une planification capacitaire rigoureuse, les entreprises peuvent non seulement répondre plus rapidement aux besoins des clients, mais aussi proposer des solutions sur-mesure, ce qui renforce leur attractivité sur des marchés de plus en plus concurrentiels.
Le chemin capacitaire, une vision pour l’industrie de demain
En combinant diagnostic précis, anticipation des évolutions, optimisation continue et intégration des technologies numériques, cette approche offre aux entreprises les moyens de maximiser leur efficacité tout en s’adaptant aux exigences du marché.
Cette démarche dépasse le simple cadre opérationnel pour devenir un véritable levier de compétitivité. Elle permet de transformer les défis industriels – qu’ils soient économiques, technologiques ou environnementaux – en opportunités concrètes. En adoptant le chemin capacitaire, les entreprises ne se contentent pas de répondre aux exigences du présent ; elles se positionnent pour bâtir un avenir pérenne, fondé sur l’agilité, l’innovation et la résilience.
Alors que les bouleversements économiques et les transitions technologiques redéfinissent les équilibres, le chemin capacitaire devient un outil indispensable pour les entreprises industrielles.
En savoir plus
Retrouvez l’ensemble de nos ressources pour accroître vos connaissances sur l’ERP pour le domaine industriel.
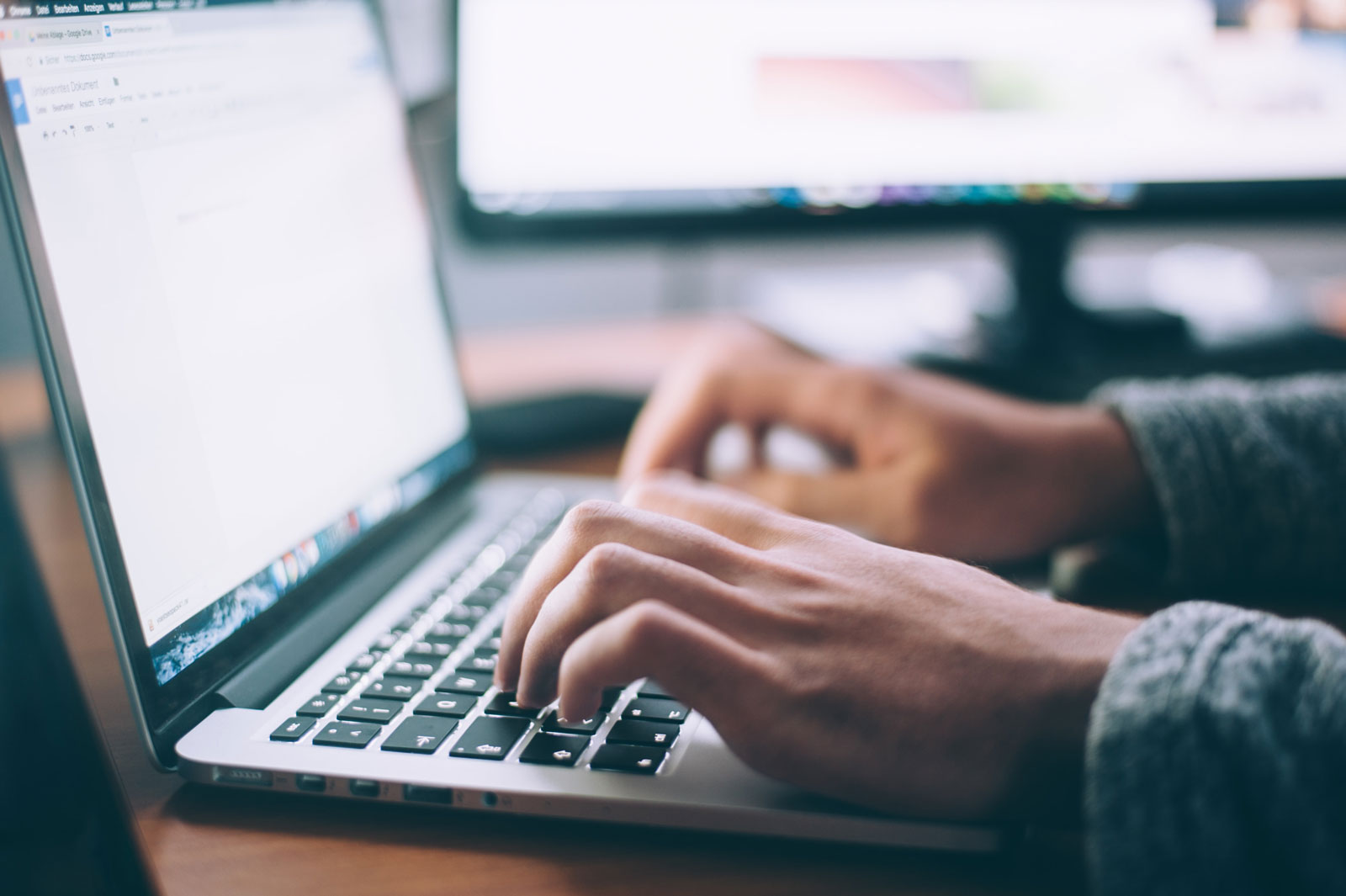
Retrouvez l’ensemble des réponses fonctionnelles de l’ERP Open-Prod aux différents secteurs industriels.
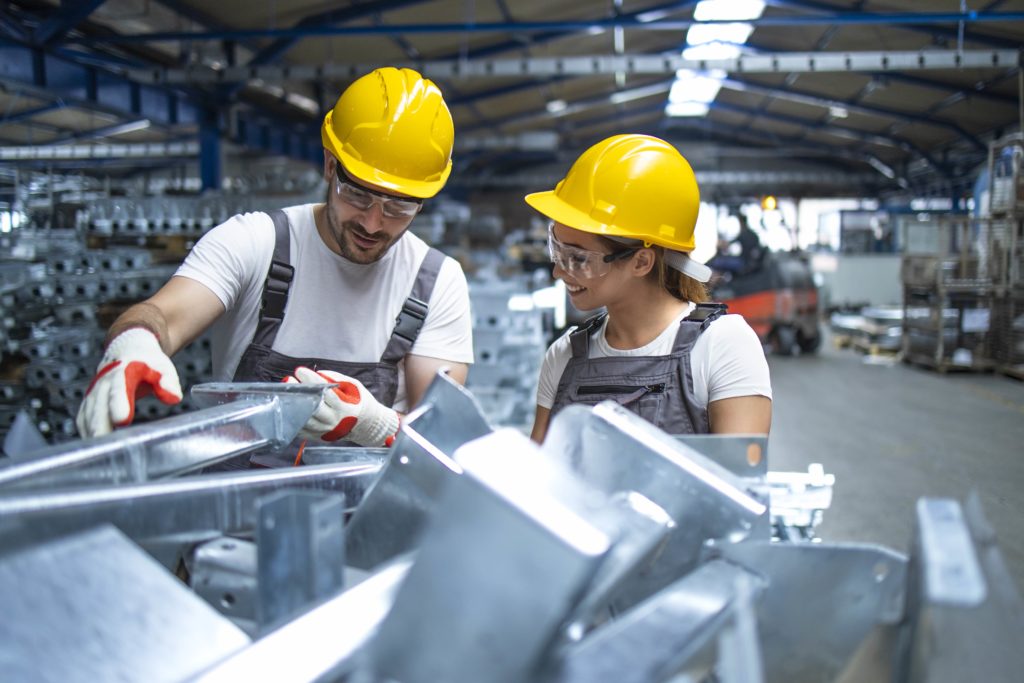
Découvrez les +200 modules d’Open-Prod conçus pour répondre aux besoins des entreprises industrielles.
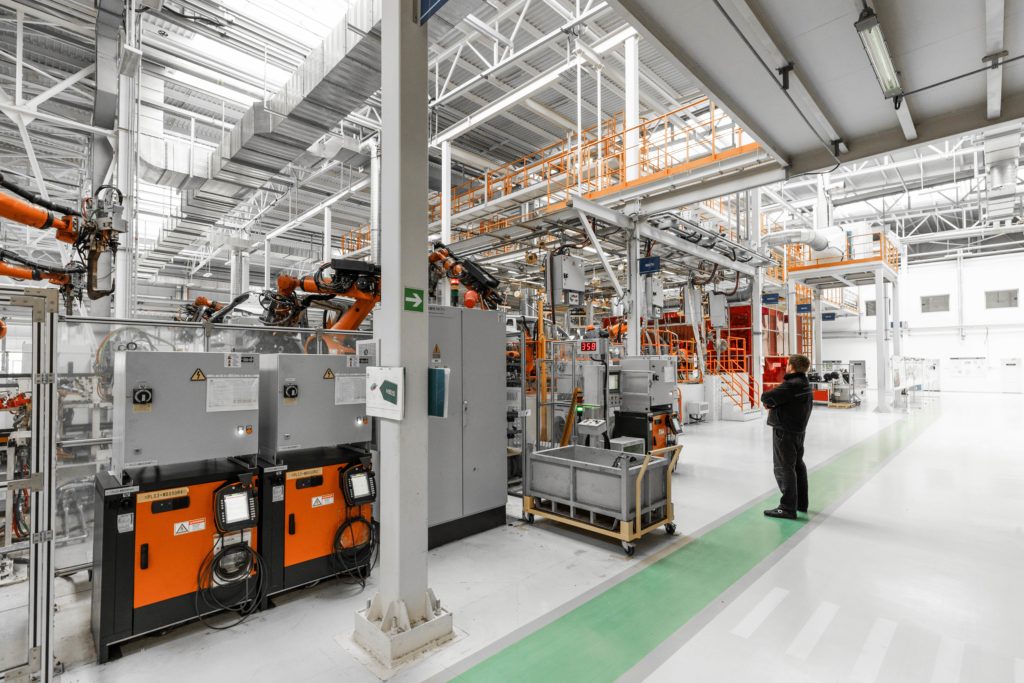