Comment réussir son changement d'ERP ? Les clés du succès dans le domaine industriel
Introduction
Le changement d'ERP (Enterprise Resource Planning) est un projet stratégique majeur pour toute entreprise, particulièrement dans le secteur industriel. Un ERP, ou Progiciel de Gestion Intégré (PGI) en français, est un système d'information qui permet de gérer et suivre au quotidien l'ensemble des informations et des services opérationnels d'une entreprise. Il couvre généralement un large spectre de fonctions telles que la gestion des achats, des stocks, de la production, de la logistique, des ressources humaines, de la comptabilité et des ventes. Dans l'industrie, l'ERP joue un rôle crucial en intégrant les processus de fabrication, de gestion de la chaîne d'approvisionnement et de planification de la production.
La décision de changer d'ERP est souvent motivée par plusieurs facteurs : l'obsolescence du système actuel, le besoin d'améliorer la performance opérationnelle, la nécessité de s'adapter à de nouvelles réglementations, ou encore le désir de soutenir la croissance de l'entreprise. Cependant, un tel projet est complexe et comporte des risques significatifs. Il nécessite une préparation minutieuse, une exécution rigoureuse et un suivi attentif pour garantir son succès. Cet article propose une analyse approfondie des étapes clés et des meilleures pratiques pour réussir un changement d'ERP dans le contexte industriel.
Évaluation des besoins et définition des objectifs
La première étape cruciale dans un projet de changement d’ERP est l’évaluation précise des besoins de l’entreprise et la définition claire des objectifs du projet. Cette phase implique une analyse approfondie des processus existants, l’identification des points faibles du système actuel et la détermination des améliorations souhaitées.
Dans le contexte industriel, cette évaluation doit prendre en compte les spécificités du secteur. Par exemple, il faut considérer les besoins en termes de gestion de la production, de traçabilité des produits, de gestion de la qualité, de maintenance des équipements, et de respect des normes industrielles. Il est également important d’anticiper les évolutions futures de l’entreprise, comme l’expansion vers de nouveaux marchés ou l’introduction de nouvelles lignes de produits.
Les objectifs du projet doivent être SMART (Spécifiques, Mesurables, Atteignables, Réalistes et Temporellement définis). Ils peuvent inclure des éléments tels que l’amélioration de la productivité, la réduction des coûts opérationnels, l’optimisation de la gestion des stocks, ou encore l’amélioration de la visibilité sur l’ensemble de la chaîne de valeur.
Toute votre gestion d'entreprise
dans un seul outil.
Constitution d'une équipe projet pluridisciplinaire
Le succès d’un projet de changement d’ERP repose en grande partie sur la qualité de l’équipe projet. Cette équipe doit être pluridisciplinaire, regroupant des représentants de tous les départements concernés : production, logistique, finance, ressources humaines, informatique, etc. Dans le contexte industriel, il est particulièrement important d’inclure des experts des processus de fabrication et de gestion de la chaîne d’approvisionnement.
L’équipe projet doit être dirigée par un chef de projet expérimenté, capable de gérer la complexité d’un tel projet et de coordonner efficacement les différentes parties prenantes. Il est également recommandé de nommer des « champions » dans chaque département, qui seront les relais du projet auprès de leurs collègues et faciliteront l’adoption du nouveau système.
Choix du nouvel ERP
Le choix du nouvel ERP est une décision cruciale qui aura des répercussions à long terme sur l’entreprise. Ce choix doit se faire sur la base d’une analyse approfondie des solutions disponibles sur le marché, en tenant compte des besoins spécifiques identifiés lors de la phase d’évaluation.
Dans le secteur industriel, il est important de privilégier des solutions qui offrent des fonctionnalités avancées en matière de gestion de la production, de planification, de gestion de la qualité et de maintenance. Des modules spécifiques comme la gestion de la production assistée par ordinateur (GPAO) ou le Manufacturing Execution System (MES) peuvent être particulièrement pertinents.
Il faut également considérer la flexibilité et l’évolutivité de la solution, sa capacité à s’intégrer avec d’autres systèmes (comme les systèmes de contrôle industriel ou les outils de conception assistée par ordinateur), ainsi que les options de déploiement (on-premise, cloud ou hybride).
Le processus de sélection doit inclure des démonstrations détaillées, des visites de référence chez d’autres entreprises industrielles utilisant le système, et une évaluation approfondie des capacités de l’éditeur et de ses partenaires intégrateurs.
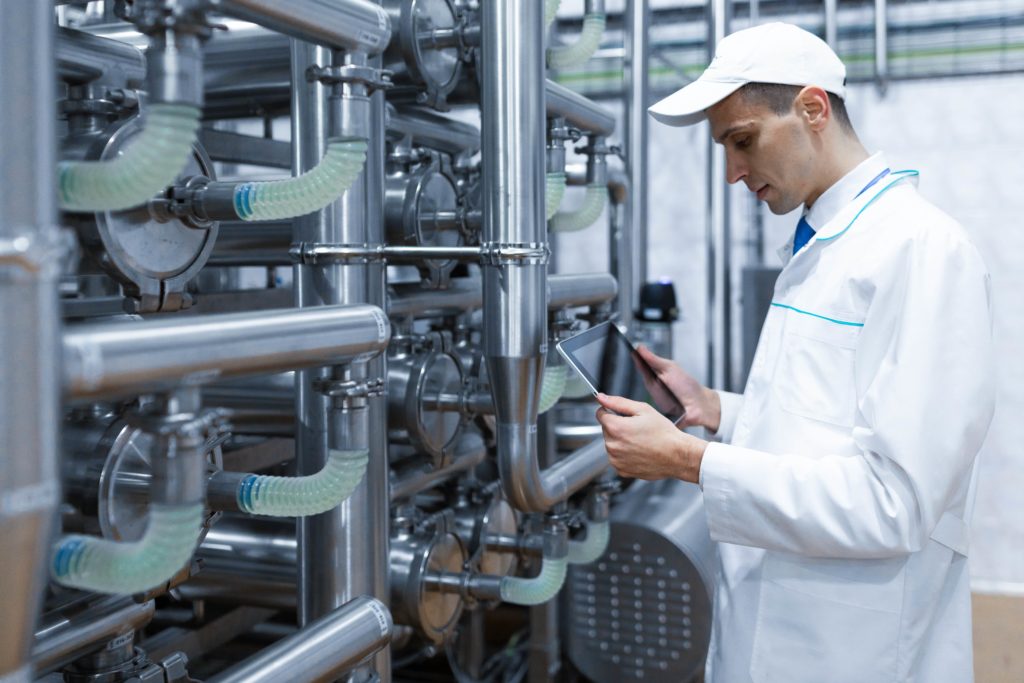
Planification détaillée du projet
Une fois l’ERP choisi, la planification détaillée du projet est essentielle. Cette planification doit couvrir toutes les phases du projet, de la préparation à la mise en production, en passant par la configuration, les tests et la formation des utilisateurs.
Dans le contexte industriel, il est crucial de planifier le déploiement de manière à minimiser les perturbations sur la production. Cela peut impliquer un déploiement par phases, en commençant par exemple par les fonctions support avant d’aborder les processus de production critiques.
Le plan de projet doit inclure un calendrier réaliste, une allocation claire des ressources, une définition précise des responsabilités, et des jalons bien définis. Il doit également prévoir des marges pour gérer les imprévus, qui sont inévitables dans un projet de cette envergure.
Préparation et nettoyage des données
La qualité des données est un facteur clé de succès pour un projet ERP. Avant la migration vers le nouveau système, il est essentiel de procéder à un nettoyage et à une standardisation des données existantes. Dans l’industrie, cela peut concerner des données critiques comme les nomenclatures produits, les gammes de fabrication, les données fournisseurs, ou encore les historiques de maintenance.
Cette phase implique souvent un travail fastidieux de vérification, de correction et d’enrichissement des données. Il est important de définir des règles claires de gouvernance des données et de mettre en place des processus pour maintenir la qualité des données à long terme.
Configuration et personnalisation du système
La configuration du nouvel ERP doit refléter les processus métier de l’entreprise. Dans le secteur industriel, cela peut impliquer la configuration de flux de production complexes, de règles de planification sophistiquées, ou encore de processus de contrôle qualité spécifiques.
Il est généralement recommandé de limiter les personnalisations au strict nécessaire, car elles peuvent compliquer les mises à jour futures et augmenter les coûts de maintenance. Cependant, dans certains cas, des personnalisations peuvent être nécessaires pour répondre à des besoins spécifiques de l’industrie. Il faut alors s’assurer que ces personnalisations sont bien documentées et qu’elles peuvent être maintenues à long terme.
Tests approfondis
La phase de tests est cruciale pour garantir le bon fonctionnement du système avant sa mise en production. Elle doit couvrir tous les aspects du système, des fonctionnalités de base aux scénarios métier les plus complexes.
Dans le contexte industriel, il est particulièrement important de tester les processus critiques comme la planification de la production, la gestion des ordres de fabrication, ou encore la traçabilité des produits. Des tests de charge doivent également être effectués pour s’assurer que le système peut gérer les volumes de transactions prévus.
Les tests doivent impliquer les utilisateurs finaux, qui sont les mieux placés pour valider l’adéquation du système avec leurs besoins quotidiens. Cette phase permet également d’identifier les éventuels ajustements nécessaires avant le déploiement.
Formation des utilisateurs
La formation des utilisateurs est un élément clé pour l’adoption réussie du nouveau système. Dans l’industrie, où les processus peuvent être complexes et où les enjeux opérationnels sont élevés, une formation approfondie est particulièrement importante.
La formation doit être adaptée aux différents profils d’utilisateurs (opérateurs, planificateurs, responsables de production, etc.) et couvrir non seulement les aspects techniques du système, mais aussi les nouveaux processus métier. Il est souvent utile de former des « super-utilisateurs » dans chaque département, qui pourront ensuite servir de relais pour former et assister leurs collègues.
Des supports de formation variés (manuels, tutoriels vidéo, sessions pratiques) doivent être mis à disposition pour répondre aux différents styles d’apprentissage. Il est également important de prévoir des formations de rappel et un support continu après le déploiement.
Gestion du changement
La gestion du changement est un aspect crucial mais souvent sous-estimé des projets ERP. Elle vise à faciliter l’adoption du nouveau système par les utilisateurs et à minimiser les résistances au changement.
Dans le contexte industriel, où les habitudes de travail peuvent être profondément ancrées, la gestion du changement revêt une importance particulière. Elle doit commencer dès le début du projet, avec une communication claire sur les objectifs et les bénéfices attendus du nouveau système.
Il est important d’impliquer les utilisateurs tout au long du projet, de recueillir leurs retours et de les prendre en compte. Des « ambassadeurs du changement » peuvent être désignés dans chaque service pour promouvoir le projet et accompagner leurs collègues.
La gestion du changement doit également anticiper les impacts organisationnels du nouveau système. Dans l’industrie, cela peut impliquer des modifications des rôles et des responsabilités, voire des changements dans l’organisation du travail sur les lignes de production.
Mise en production et support post-déploiement
La mise en production du nouveau système est une étape critique qui doit être minutieusement planifiée. Dans l’industrie, où les arrêts de production peuvent avoir des conséquences financières importantes, le timing de la bascule doit être soigneusement choisi (par exemple pendant une période creuse ou un arrêt planifié).
Un plan de bascule détaillé doit être élaboré, définissant précisément les étapes de la mise en production, les responsabilités de chacun, et les procédures de retour en arrière en cas de problème majeur. Une équipe de support doit être mobilisée pour répondre rapidement aux problèmes éventuels lors des premiers jours d’utilisation.
Après la mise en production, un suivi attentif est nécessaire pour s’assurer que le système fonctionne comme prévu et que les utilisateurs s’adaptent bien. Des ajustements peuvent être nécessaires pour optimiser les processus ou résoudre des problèmes imprévus.
Évaluation et optimisation continue
Une fois le nouveau système en place, il est important de mettre en place un processus d’évaluation et d’optimisation continue. Cela implique de suivre régulièrement des indicateurs de performance clés (KPI) pour mesurer les bénéfices réels du nouveau système par rapport aux objectifs initiaux.
Dans le contexte industriel, ces KPI peuvent inclure des métriques telles que le taux de service client, les niveaux de stock, les temps de cycle de production, ou encore la précision des prévisions. Il est également important de recueillir régulièrement les retours des utilisateurs pour identifier les axes d’amélioration.
L’optimisation continue peut impliquer des ajustements de configuration, des formations complémentaires, ou même l’ajout de nouvelles fonctionnalités pour répondre à l’évolution des besoins de l’entreprise.
Conclusion
Le changement d’ERP dans le secteur industriel est un projet complexe qui nécessite une approche méthodique et une attention particulière à de nombreux aspects. De l’évaluation initiale des besoins à l’optimisation continue post-déploiement, chaque étape joue un rôle crucial dans le succès du projet.
La réussite d’un tel projet repose sur une combinaison de facteurs techniques et humains. Une planification minutieuse, une équipe projet compétente, un choix judicieux de la solution, une préparation rigoureuse des données et des tests approfondis sont essentiels. Mais tout aussi importantes sont la formation des utilisateurs, la gestion efficace du changement et l’implication continue des parties prenantes.
Dans le contexte spécifique de l’industrie, il est crucial de prendre en compte les enjeux particuliers du secteur, comme la gestion de processus de production complexes, les exigences de traçabilité, ou encore l’intégration avec les systèmes de contrôle industriel. Le nouveau système doit non seulement répondre aux besoins actuels de l’entreprise, mais aussi être suffisamment flexible pour s’adapter aux évolutions futures du secteur, comme l’industrie 4.0 ou l’Internet des objets industriel.
Enfin, il est important de garder à l’esprit qu’un changement d’ERP n’est pas une fin en soi, mais un moyen d’améliorer la performance globale de l’entreprise. Le véritable succès se mesure à long terme, dans la capacité du nouveau système à soutenir efficacement les opérations quotidiennes et à contribuer à la réalisation des objectifs stratégiques de l’entreprise.
En suivant ces principes et en adaptant l’approche aux spécificités de leur contexte, les entreprises industrielles peuvent maximiser leurs chances de réussir leur changement d’ERP et d’en tirer tous les bénéfices attendus.
En savoir plus
Retrouvez l’ensemble de nos ressources pour accroître vos connaissances sur l’ERP pour le domaine industriel.
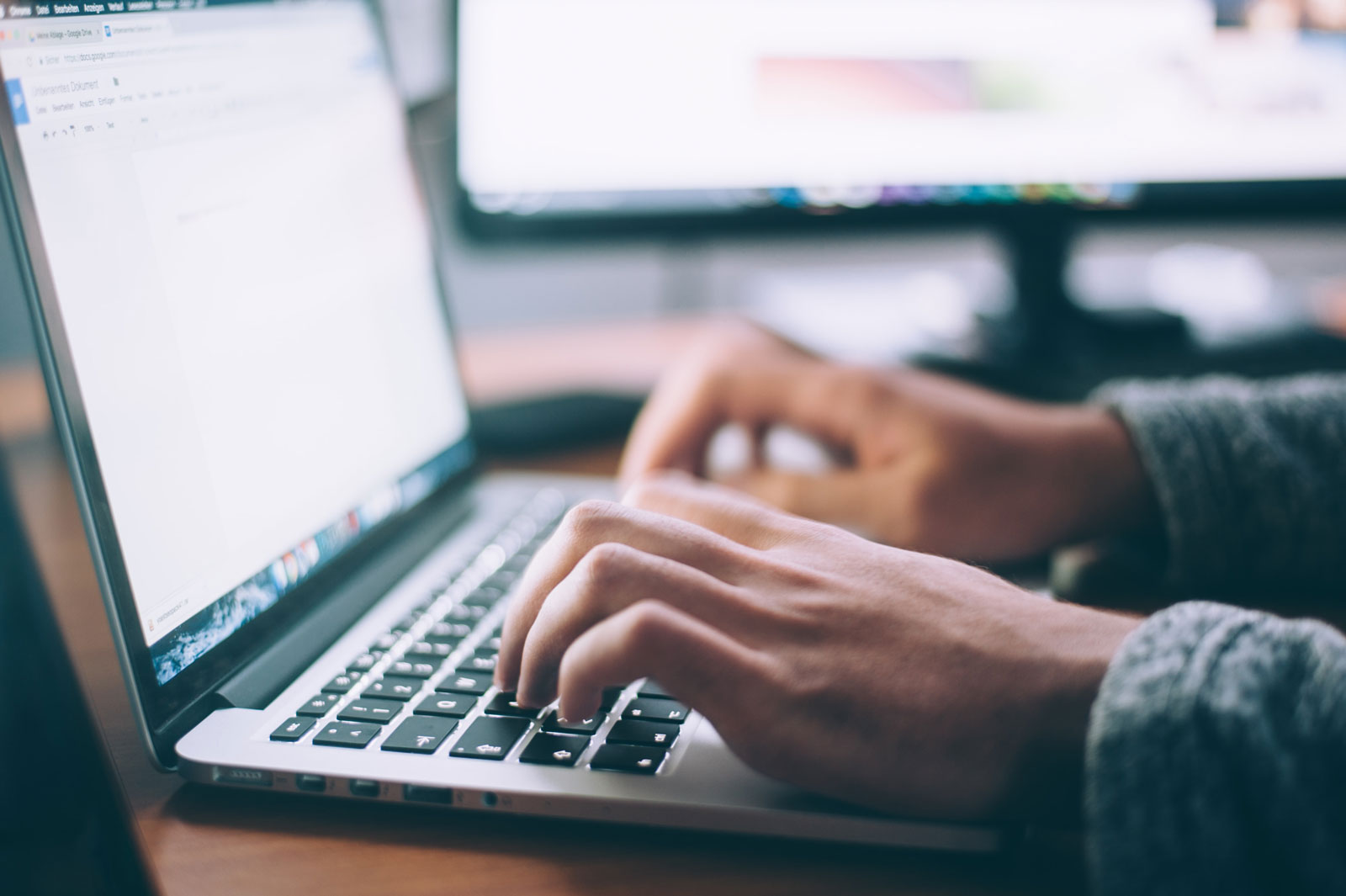
Retrouvez l’ensemble des réponses fonctionnelles de l’ERP Open-Prod aux différents secteurs industriels.
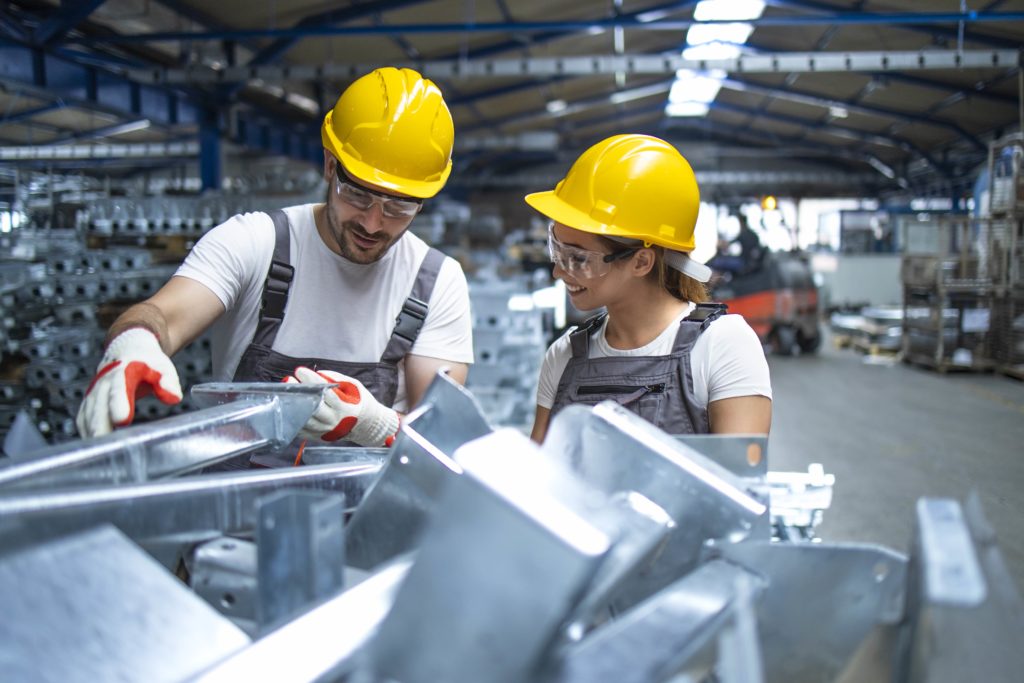
Découvrez les +200 modules d’Open-Prod conçus pour répondre aux besoins des entreprises industrielles.
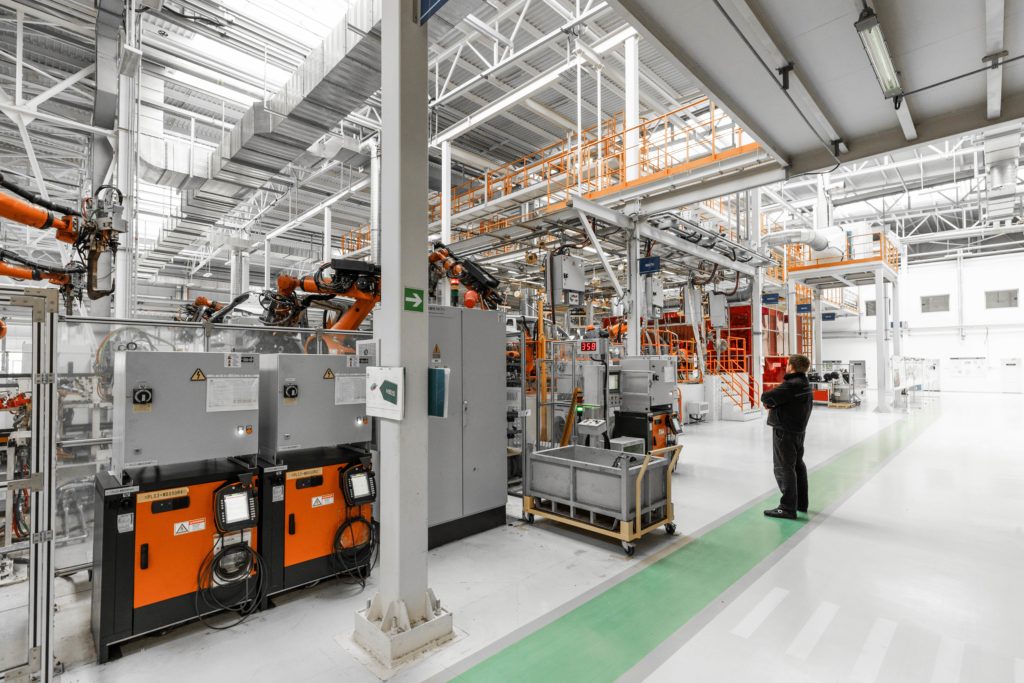