L'évolution des logiciels de gestion de production : vers l'usine intelligente du futur
La quatrième révolution industrielle redessine profondément les contours de la production manufacturière. Les logiciels de gestion de production sont aujourd'hui à la croisée d'une transformation technologique sans précédent, prome
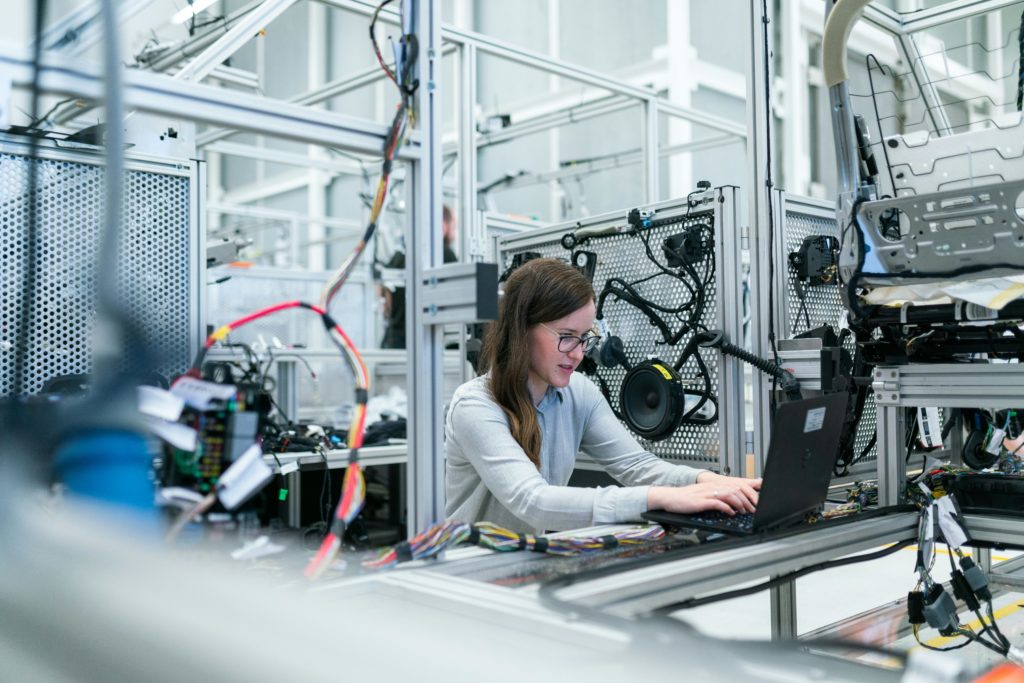
Les systèmes de production à l'ère numérique
Les logiciels de gestion de production, tels que les MES (Manufacturing Execution System) ou ERP (Enterprise Resource Planning), ont longtemps été le pivot central des opérations industrielles. Leur rôle historique de coordination et d'optimisation des activités de fabrication se trouve aujourd'hui confronté à des défis majeurs : personnalisation croissante des produits, cycles de production accélérés et concurrence mondiale intensifiée.
Cette mutation s'opère grâce à l'intégration de technologies émergentes qui transforment radicalement la conception même de la production. L'intelligence artificielle (IA) et l'apprentissage automatique deviennent les catalyseurs d'une nouvelle génération de systèmes capables de dépasser les limitations des approches conventionnelles. Ces technologies offrent désormais la capacité de simuler des processus cognitifs complexes, d'analyser des volumes massifs de données et de prendre des décisions autonomes en temps réel.
L'interconnexion totale : quand les machines communiquent
L'Internet des objets industriel (IIoT) constitue la colonne vertébrale de cette révolution technologique. Cette interconnexion permet de créer un écosystème numérique où chaque équipement, chaque capteur et chaque système devient un nœud communicant. Le concept de jumeau numérique prend tout son sens : l'usine devient un organisme vivant et intelligent, capable d'auto-adaptation et d'apprentissage continu.
Les capacités offertes par cette interconnexion sont révolutionnaires. Un système peut désormais :
- Détecter et prédire les pannes avant qu’elles ne surviennent
- Réaffecter dynamiquement les ressources de production
- Optimiser les processus en fonction de multiples variables
- Ajuster instantanément les lignes de production
Ces systèmes auto-adaptatifs utilisent des algorithmes d'apprentissage par renforcement pour expérimenter continuellement de nouvelles configurations, générant ainsi des méthodes de production potentiellement plus efficaces que celles imaginées par les ingénieurs humains.
Toute votre gestion d'entreprise
dans un seul outil.
Les défis humains de la transformation technologique
L'automatisation croissante soulève des questions cruciales concernant l'emploi et l'évolution des compétences. Contrairement aux craintes d'une substitution totale des travailleurs, l'usine du futur repose sur une collaboration renouvelée entre l'homme et la machine.
Cette transformation implique une redéfinition profonde des métiers industriels, avec l'émergence de nouveaux profils axés sur :
- L’analyse de données
- La programmation de systèmes d’IA
- La maintenance d’équipements connectés
- La résolution de problèmes complexes
Les défis humains de la transformation technologique
Au-delà de la performance technologique, cette révolution interroge notre modèle de production dans sa globalité. L'usine intelligente n'est pas qu'un défi technique, mais un projet de société qui nécessite une réflexion éthique et stratégique.
Les enjeux sont multiples : sécurisation des systèmes numériques, gestion des données, impact environnemental, répartition équitable des bénéfices technologiques. Les logiciels de nouvelle génération intégreront des algorithmes d'optimisation énergétique, faciliteront les pratiques de production circulaire et contribueront à une industrie plus durable.
La clé résidera dans la capacité des acteurs - industriels, chercheurs, décideurs politiques et société civile - à collaborer et à construire ensemble ce nouveau paradigme. L'objectif est de créer un modèle industriel plus intelligent, plus flexible et plus humain, capable de répondre aux défis complexes d'un monde en mutation constante.
En savoir plus
Retrouvez l’ensemble de nos ressources pour accroître vos connaissances sur l’ERP pour le domaine industriel.
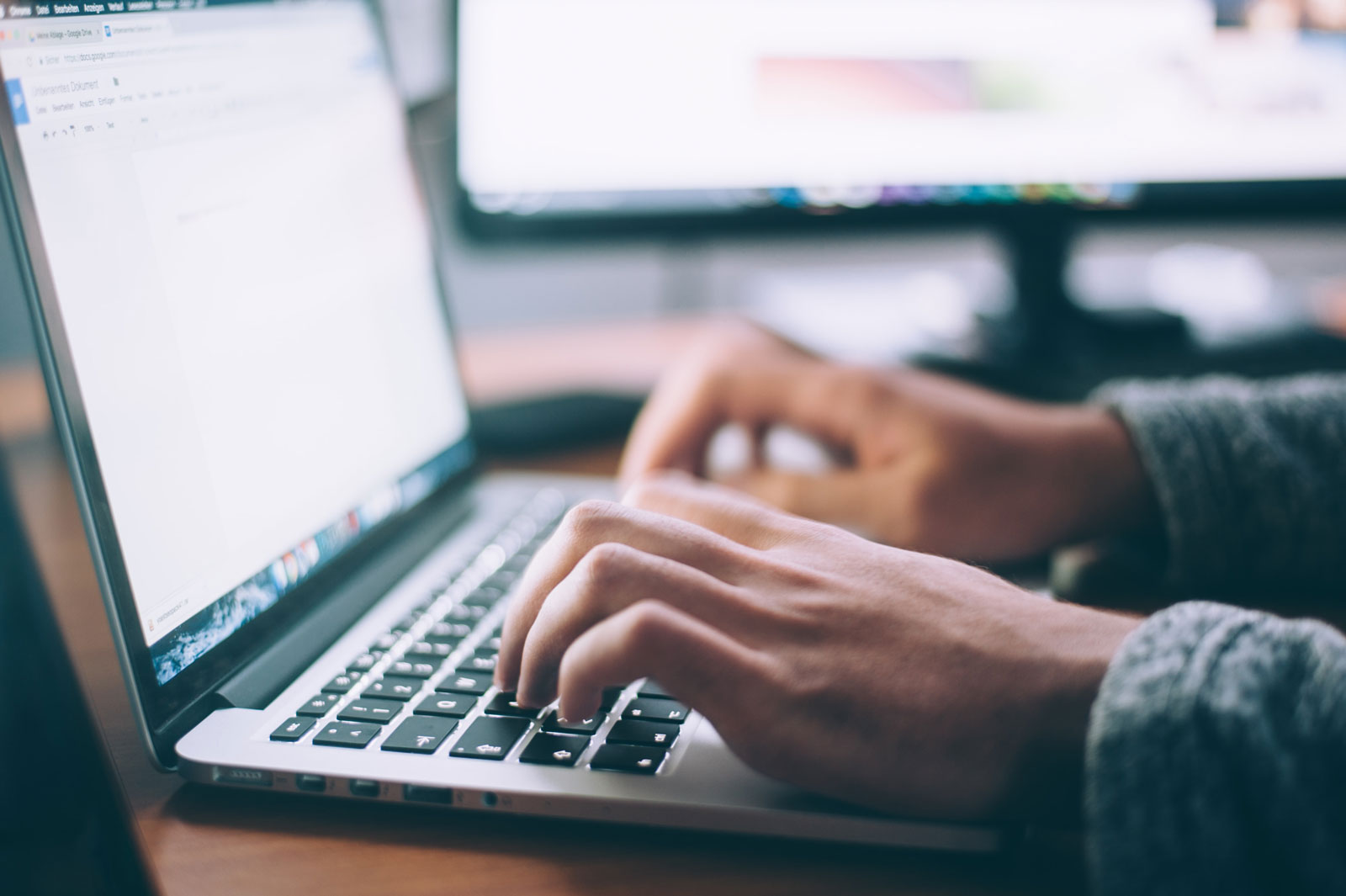
Retrouvez l’ensemble des réponses fonctionnelles de l’ERP Open-Prod aux différents secteurs industriels.
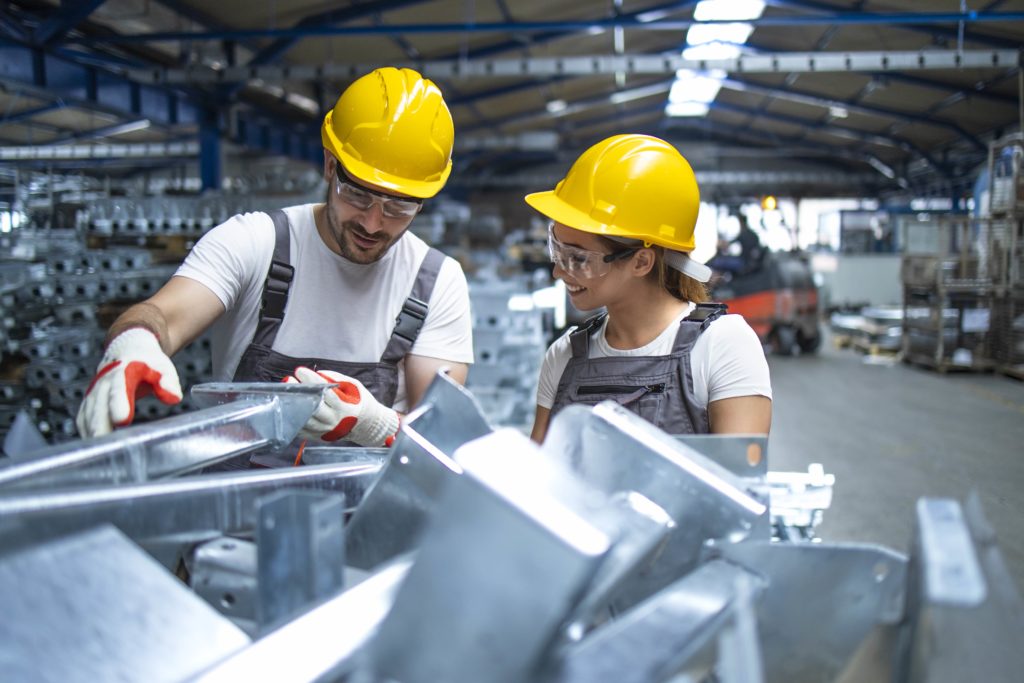
Découvrez les +200 modules d’Open-Prod conçus pour répondre aux besoins des entreprises industrielles.
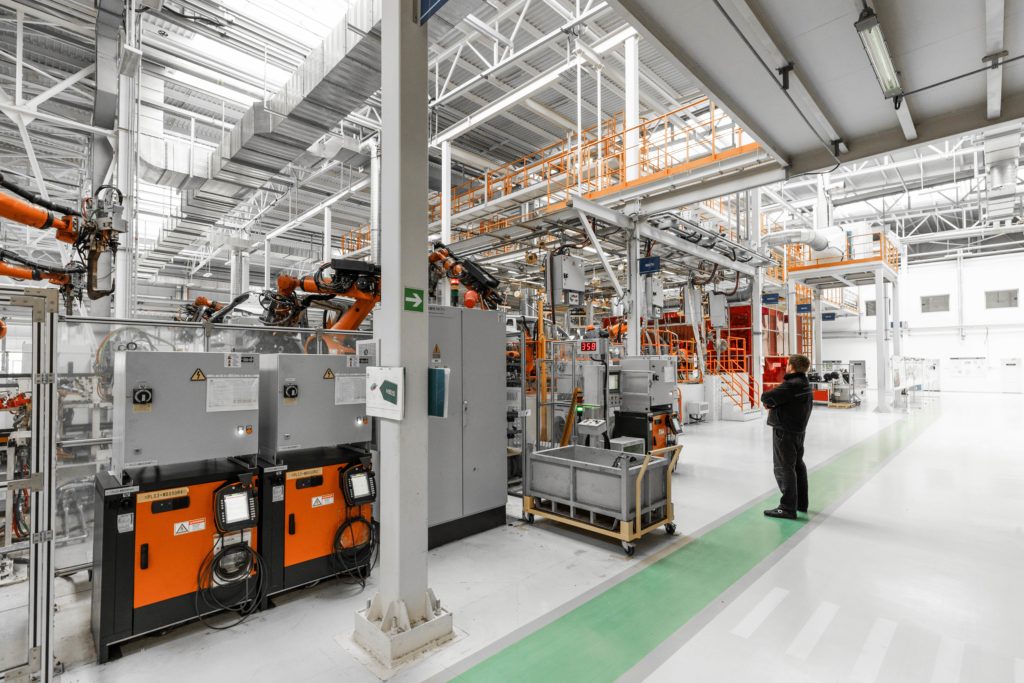