L'ordonnancement à capacité finie : Optimiser la production dans un monde aux ressources limitées
Introduction :
L'ordonnancement joue un rôle central dans l'optimisation des processus de fabrication. Parmi les diverses approches disponibles, l'ordonnancement à capacité finie se démarque comme une méthode particulièrement pertinente et efficace. Cette technique, qui tient compte des limitations réelles des ressources disponibles, offre une vision plus réaliste et pragmatique de la planification de production.
1. Définition de l'ordonnancement à capacité finie
L'ordonnancement à capacité finie est une approche sophistiquée de planification de production qui intègre les contraintes réelles des ressources disponibles dans l'élaboration des plans de production. Contrairement à l'ordonnancement à capacité infinie, qui suppose une disponibilité illimitée des ressources, cette méthode prend en compte les limitations concrètes en termes de machines, de main-d'œuvre, de matières premières, et même de temps.
Cette approche reflète la réalité opérationnelle des entreprises, où les ressources sont toujours limitées et doivent être gérées de manière optimale. Elle permet de créer des plannings de production réalistes et réalisables, en évitant la surcharge des ressources et en identifiant les goulots d'étranglement potentiels avant qu'ils ne perturbent la production.
L'ordonnancement à capacité finie va au-delà de la simple allocation de tâches ; il s'agit d'un processus dynamique qui équilibre en permanence les demandes de production avec les capacités disponibles, en tenant compte de multiples variables telles que les priorités des commandes, les temps de configuration, les compétences des opérateurs, et les spécificités des équipements.
2. Principes fondamentaux
Prise en compte des capacités réelles : Le système d’ordonnancement à capacité finie modélise avec précision les capacités de chaque ressource. Cela inclut non seulement la capacité maximale (par exemple, les heures de fonctionnement d’une machine), mais aussi les variations de capacité dues à la maintenance, aux pauses, ou aux changements d’équipe. Cette modélisation détaillée permet une planification plus précise et évite les surcharges irréalistes.
Allocation dynamique des ressources : L’allocation des ressources n’est pas statique mais s’ajuste en temps réel en fonction des changements de situation. Si une machine tombe en panne ou si une commande urgente arrive, le système réévalue l’allocation des ressources pour s’adapter à la nouvelle situation. Cette flexibilité permet de maintenir un planning optimal même face aux aléas quotidiens de la production.
Gestion des contraintes : L’ordonnancement à capacité finie intègre une multitude de contraintes qui reflètent la complexité réelle des environnements de production. Ces contraintes peuvent inclure :
- Les temps de configuration et de changement d’outils
- Les compétences spécifiques requises pour certaines tâches
- Les dépendances entre les différentes étapes de production
- Les priorités des commandes clients
- Les délais de livraison des matières premières
- Les règles de qualité et de sécurité
La prise en compte de ces contraintes permet de créer des plannings non seulement réalisables, mais aussi conformes aux exigences opérationnelles et stratégiques de l’entreprise.
Optimisation continue :
L’ordonnancement à capacité finie n’est pas un processus statique mais un cycle d’amélioration continue. Le plan de production est constamment révisé et ajusté pour refléter les changements de capacité, de demande, ou de priorités. Cette optimisation continue permet de maintenir l’efficacité de la production même dans des environnements très dynamiques.
3. Processus d'ordonnancement à capacité finie
Collecte des données :
La première étape cruciale consiste à rassembler toutes les informations pertinentes pour l’ordonnancement. Cela inclut :
- Les détails des commandes clients (quantités, spécifications, délais)
- L’inventaire des ressources disponibles (machines, outils, personnel)
- Les gammes opératoires détaillées pour chaque produit
- Les temps de traitement standards pour chaque opération
- Les contraintes spécifiques liées à la production (qualité, sécurité, réglementations)
La précision et l’exhaustivité de ces données sont essentielles pour la fiabilité du planning généré. De nombreuses entreprises utilisent des systèmes ERP (Enterprise Resource Planning) ou MES (Manufacturing Execution System) pour centraliser et gérer ces informations.
Définition des priorités :
L’établissement de règles de priorité est une étape clé qui influence directement l’ordre de traitement des tâches. Ces règles peuvent être basées sur divers critères :
- Date d’échéance (priorité aux commandes les plus urgentes)
- Importance du client
- Rentabilité de la commande
- Minimisation des temps de configuration
- Optimisation de l’utilisation des ressources critiques
Les entreprises peuvent définir des règles complexes combinant plusieurs de ces critères pour refléter au mieux leurs objectifs stratégiques et opérationnels.
Allocation des ressources :
Cette étape consiste à attribuer les tâches aux ressources disponibles en respectant toutes les contraintes identifiées. Le processus d’allocation prend en compte :
- La disponibilité des ressources à chaque instant
- Les compétences requises pour chaque tâche
- Les temps de configuration et de changement d’outils
- Les dépendances entre les tâches
- Les contraintes de capacité de chaque ressource
L’objectif est de maximiser l’utilisation des ressources tout en respectant les délais et les priorités définis.
Création du planning :
Sur la base de l’allocation des ressources, un planning détaillé est généré. Ce planning indique :
- Quand chaque tâche doit commencer et se terminer
- Quelle ressource est assignée à chaque tâche
- Les temps de configuration et de transition entre les tâches
- Les périodes d’inactivité prévues pour chaque ressource
Le planning est généralement visualisé sous forme de diagramme de Gantt, offrant une représentation claire et intuitive de l’ordonnancement.
Optimisation et ajustement :
Une fois le planning initial créé, il est soumis à un processus d’optimisation visant à :
- Maximiser l’utilisation des ressources
- Minimiser les temps d’inactivité
- Réduire les retards de livraison
- Équilibrer la charge de travail entre les ressources
Des algorithmes d’optimisation complexes sont souvent utilisés pour cette étape, explorant de multiples scénarios pour trouver la meilleure configuration possible.
4. Avantages de l'ordonnancement à capacité finie
Réalisme accru :
L’ordonnancement à capacité finie offre une vision beaucoup plus précise et réaliste de la capacité de production réelle de l’entreprise. Cette précision permet de :
- Éviter les promesses de livraison irréalistes aux clients
- Identifier précocement les périodes de sous-capacité ou de surcapacité
- Faciliter la prise de décisions stratégiques concernant les investissements en capacité
Meilleure utilisation des ressources :
En optimisant l’allocation des tâches, cette méthode permet :
- Une réduction significative des temps d’inactivité des machines et du personnel
- Une meilleure synchronisation entre les différentes étapes de production
- Une diminution des stocks intermédiaires grâce à une production plus fluide
Réduction des retards :
La prise en compte précise des capacités et des contraintes permet de :
- Identifier et résoudre les goulots d’étranglement avant qu’ils n’impactent la production
- Anticiper les problèmes potentiels et prendre des mesures préventives
- Réagir rapidement aux perturbations imprévues en réajustant le planning
Amélioration de la précision des délais :
Grâce à une planification plus réaliste, les entreprises peuvent :
- Fournir des dates de livraison plus fiables aux clients
- Améliorer la satisfaction client en respectant les engagements pris
- Réduire les coûts liés aux retards et aux pénalités
Flexibilité accrue :
L’ordonnancement à capacité finie offre une grande adaptabilité, permettant :
- Une réponse rapide aux changements de priorités ou d’urgences
- Une intégration facile des commandes de dernière minute
- Une adaptation dynamique aux fluctuations de capacité (pannes, absences, etc.)
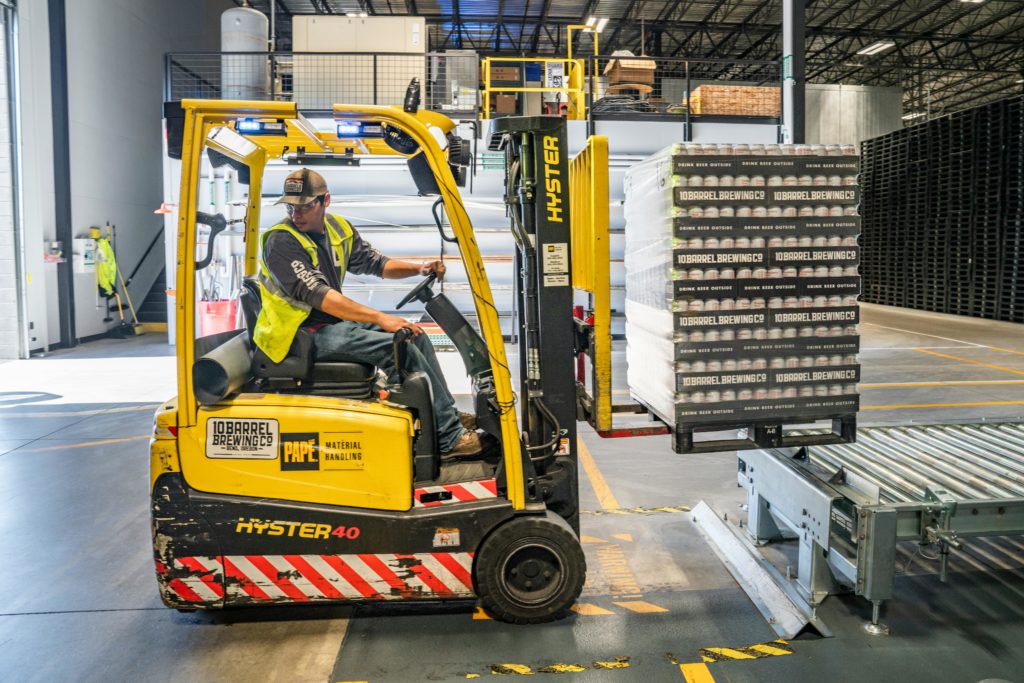
5. Défis et considérations
Complexité de mise en œuvre :
L’implémentation d’un système d’ordonnancement à capacité finie peut être complexe et exigeante. Elle nécessite :
- Une analyse approfondie des processus de production existants
- Une collecte exhaustive et précise des données sur les ressources et les opérations
- Une modélisation détaillée des contraintes et des règles de production
- Une formation approfondie du personnel à l’utilisation du nouveau système
Cette complexité peut se traduire par des projets de mise en œuvre longs et coûteux.
Besoin en technologie :
L’ordonnancement à capacité finie repose généralement sur des logiciels spécialisés capables de gérer la complexité des calculs impliqués. Cela implique :
- Des investissements significatifs en logiciels et en infrastructure IT
- La nécessité d’intégrer le système d’ordonnancement avec les autres systèmes de l’entreprise (ERP, MES, etc.)
- Un besoin en compétences techniques pour maintenir et faire évoluer le système
Résistance au changement :
L’introduction d’un système d’ordonnancement à capacité finie peut rencontrer une résistance au sein de l’organisation, notamment :
- De la part des planificateurs habitués à des méthodes plus traditionnelles
- Des opérateurs qui peuvent percevoir le système comme une perte d’autonomie
- Des managers qui doivent adapter leurs pratiques de gestion
Surmonter cette résistance nécessite une gestion du changement efficace et une communication claire sur les bénéfices du nouveau système.
Maintenance continue :
Pour rester efficace, un système d’ordonnancement à capacité finie nécessite une maintenance constante :
- Mise à jour régulière des données sur les ressources et les processus
- Ajustement des règles et des contraintes en fonction de l’évolution de l’entreprise
- Surveillance continue de la performance du système et optimisation des paramètres
Cette maintenance représente un investissement continu en temps et en ressources
6. Applications dans l'industrie
Fabrication discrète :
L’ordonnancement à capacité finie est particulièrement adapté aux industries de fabrication discrète, telles que :
- L’industrie automobile : gestion de lignes d’assemblage complexes, coordination de multiples fournisseurs
- L’aérospatiale : planification de la production d’avions et de composants avec des cycles longs et des contraintes strictes
- L’électronique : optimisation de la production de composants avec des temps de cycle courts et des changements fréquents
Dans ces industries, la méthode permet d’optimiser l’utilisation des équipements coûteux et de gérer efficacement les chaînes d’approvisionnement complexes.
Industrie de process :
Bien que traditionnellement moins utilisé dans les industries de process, l’ordonnancement à capacité finie trouve de plus en plus d’applications dans ce domaine :
- Industrie chimique : planification des campagnes de production, gestion des contraintes de nettoyage entre les lots
- Industrie agroalimentaire : optimisation des lignes de production avec des contraintes de périssabilité des matières premières
- Industrie mécatronique : synchronisation des processus de production complexes impliquant des systèmes mécaniques, électroniques et informatiques avec des ressources limitées.
Dans ces secteurs, la méthode aide à maximiser l’utilisation des installations coûteuses tout en respectant les contraintes de qualité et de sécurité.
Secteur des services :
L’ordonnancement à capacité finie s’étend également au secteur des services :
- Centres d’appels : optimisation de l’allocation des agents en fonction des pics d’appels prévus
- Hôpitaux : planification des interventions chirurgicales et gestion des ressources médicales
- Maintenance : organisation des équipes de maintenance pour des interventions planifiées et réactives
Dans ces contextes, la méthode permet d’améliorer la qualité de service tout en optimisant l’utilisation des ressources humaines.
7. Techniques et outils d'ordonnancement à capacité finie
Algorithmes d’optimisation :
Les systèmes d’ordonnancement à capacité finie utilisent des algorithmes sophistiqués pour trouver la meilleure allocation des ressources. Ces algorithmes peuvent inclure :
- Des méthodes heuristiques pour trouver rapidement des solutions acceptables
- Des algorithmes génétiques qui « évoluent » vers des solutions optimales
- Des techniques de programmation linéaire pour résoudre des problèmes d’allocation complexes
- Des méthodes de recherche locale pour affiner les solutions
Ces algorithmes permettent de traiter des problèmes d’ordonnancement extrêmement complexes impliquant de nombreuses variables et contraintes.
Simulation :
Les techniques de simulation sont souvent utilisées en complément de l’ordonnancement pour :
- Tester différents scénarios de production avant leur mise en œuvre réelle
- Évaluer l’impact de changements dans les ressources ou les processus
- Identifier les goulots d’étranglement potentiels et les opportunités d’amélioration
Les simulations peuvent être basées sur des modèles déterministes ou stochastiques, selon le niveau de variabilité et d’incertitude dans l’environnement de production.
Intelligence artificielle :
L’intégration de l’IA et du machine learning dans l’ordonnancement à capacité finie ouvre de nouvelles perspectives :
- Prédiction plus précise des temps de traitement basée sur l’historique de production
- Identification automatique des patterns et des anomalies dans les données de production
- Optimisation dynamique et en temps réel des plannings en fonction des conditions changeantes
Ces technologies permettent une adaptation plus rapide et plus intelligente aux fluctuations de la demande et des capacités.
Visualisation des données :
Les outils de visualisation jouent un rôle crucial dans l’ordonnancement à capacité finie :
- Les diagrammes de Gantt offrent une représentation claire des tâches planifiées et de leur séquence
- Les tableaux de bord interactifs permettent aux utilisateurs de visualiser rapidement l’état de la production
- Les graphiques de charge montrent l’utilisation des ressources au fil du temps
- Les cartes thermiques peuvent mettre en évidence les périodes de sur ou sous-utilisation des capacités
Ces outils visuels facilitent la compréhension et l’analyse des plannings complexes, aidant les décideurs à prendre des décisions éclairées.
Toute votre gestion d'entreprise
dans un seul outil.
Conclusion :
L'ordonnancement à capacité finie représente une approche sophistiquée et réaliste de la planification de production. En prenant en compte les limitations réelles des ressources, cette méthode permet aux entreprises d'optimiser leur production, d'améliorer leur efficacité opérationnelle et de mieux répondre aux attentes des clients. Bien que sa mise en œuvre puisse être complexe, les avantages en termes de précision, de flexibilité et d'utilisation des ressources en font un outil inestimable dans le paysage industriel moderne.
À mesure que la technologie continue d'évoluer, l'ordonnancement à capacité finie deviendra encore plus puissant et accessible, offrant aux entreprises de toutes tailles la possibilité de gérer efficacement leurs opérations dans un environnement de plus en plus compétitif et dynamique. Les gestionnaires et les ingénieurs de production doivent donc rester attentifs aux développements dans ce domaine pour maintenir leur avantage concurrentiel et répondre aux défis futurs de la production.
En savoir plus
Retrouvez l’ensemble de nos ressources pour accroître vos connaissances sur l’ERP pour le domaine industriel.
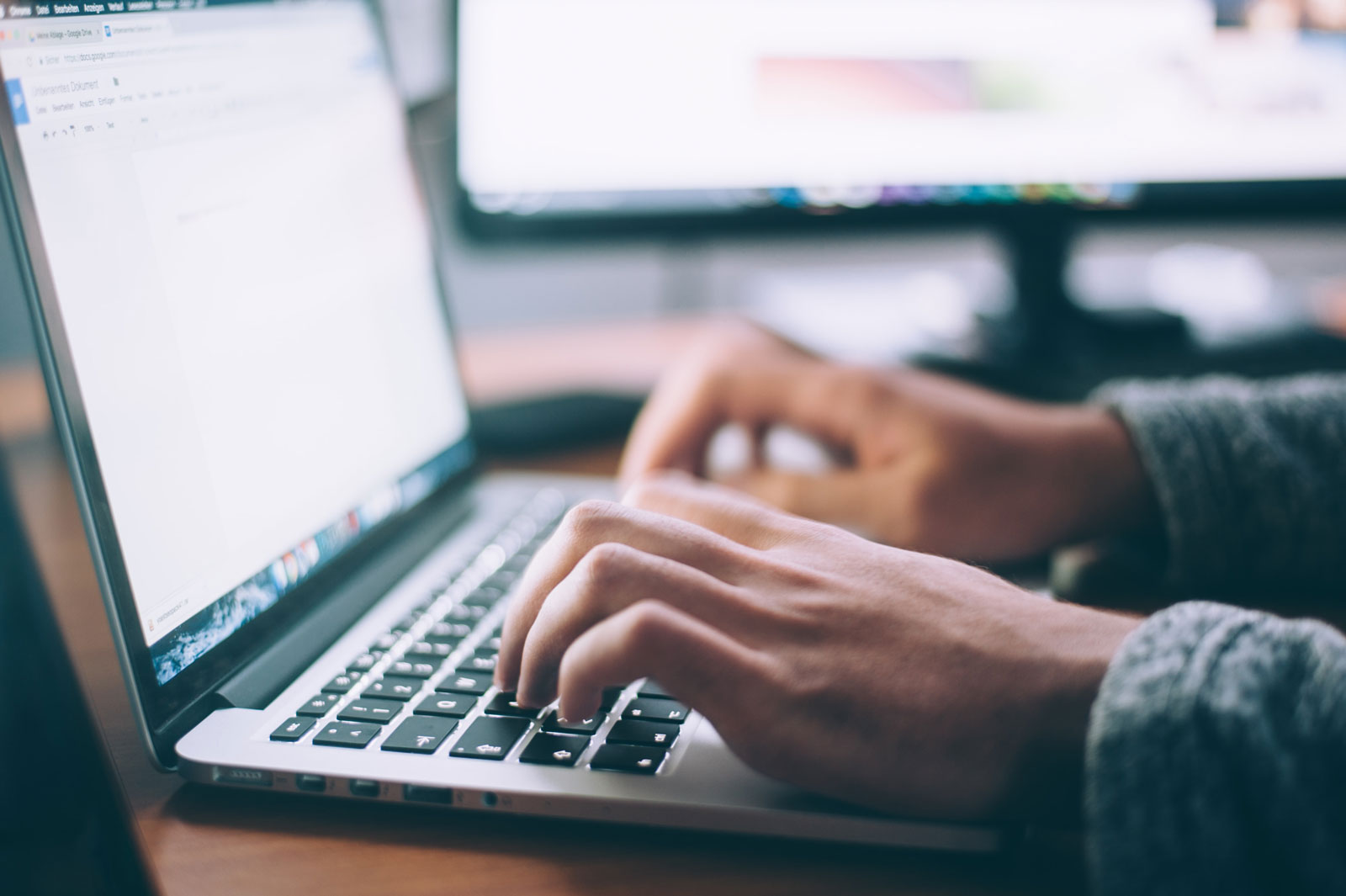
Retrouvez l’ensemble des réponses fonctionnelles de l’ERP Open-Prod aux différents secteurs industriels.
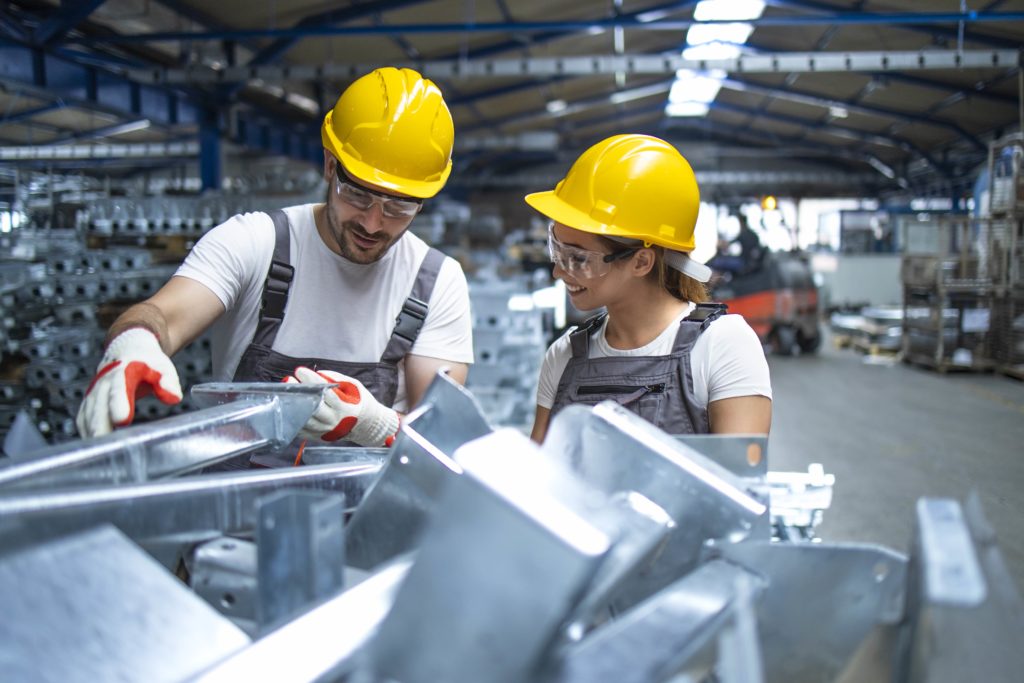
Découvrez les +200 modules d’Open-Prod conçus pour répondre aux besoins des entreprises industrielles.
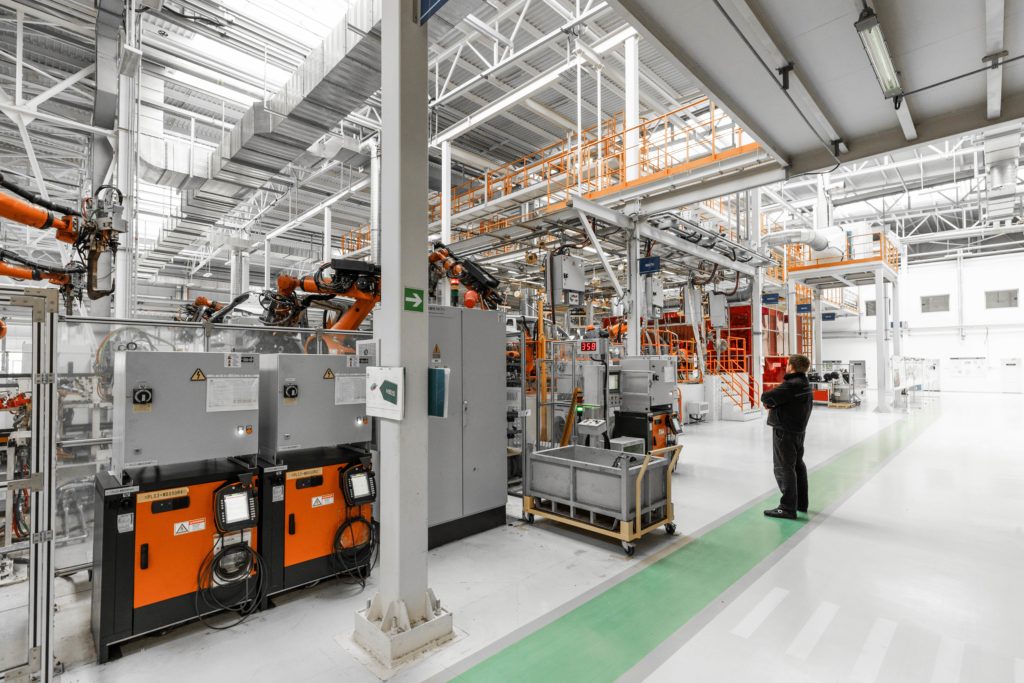