Analyse des coûts de production : les indicateurs clés à surveiller pour optimiser la performance opérationnelle
I. Comprendre les coûts de production
Les coûts de production représentent l’ensemble des dépenses engagées par une entreprise pour fabriquer ses produits ou fournir ses services. Ces coûts, qui constituent une composante essentielle de la structure financière, influencent directement la rentabilité et la compétitivité. Leur compréhension précise est donc une étape incontournable pour toute entreprise souhaitant optimiser sa performance.
1. Les composantes des coûts de production
Les coûts de production se décomposent en deux grandes catégories :
- Les coûts fixes : Ces dépenses restent constantes, indépendamment du volume produit. Elles incluent des éléments tels que les loyers, les salaires des employés administratifs ou encore l’amortissement des équipements industriels.
- Les coûts variables : Directement liés au volume de production, ces coûts fluctuent en fonction de l’activité. Ils comprennent les matières premières, l’énergie consommée, les consommables et les frais de transport.
À ces deux catégories s’ajoutent les coûts indirects, qui concernent des activités support nécessaires à la production mais non directement attribuables à un produit spécifique. Par exemple, les coûts de maintenance des machines ou les frais généraux.
2. Les indicateurs fondamentaux pour évaluer les coûts
Pour analyser les coûts de production, plusieurs indicateurs sont utilisés :
- Le coût moyen (CM) : Il mesure le coût total rapporté au nombre d’unités produites. Cet indicateur permet de suivre l’évolution des économies d’échelle et d’identifier le seuil à partir duquel la production devient plus rentable.
- Le coût marginal (Cm) : Ce paramètre indique le coût supplémentaire engendré par la production d’une unité supplémentaire. Très utile pour des prises de décision tactiques, il aide à déterminer si une augmentation de la production est économiquement viable.
- Le seuil de rentabilité : Correspondant au point où les revenus couvrent exactement les coûts totaux, cet indicateur est critique pour évaluer le niveau minimal de production nécessaire à l’équilibre financier.
3. Les défis liés à l’analyse des coûts
L’évolution constante des environnements économiques et technologiques complique la maîtrise des coûts. Par exemple, l’intégration de nouvelles technologies ou les variations des prix des matières premières nécessitent des ajustements réguliers. De plus, les coûts indirects, souvent plus difficiles à quantifier, représentent un défi pour les entreprises cherchant à affiner leurs calculs.
Une analyse rigoureuse de ces composantes et indicateurs est essentielle pour détecter les inefficacités, optimiser l’utilisation des ressources et, au final, renforcer la compétitivité dans un marché toujours plus exigeant.
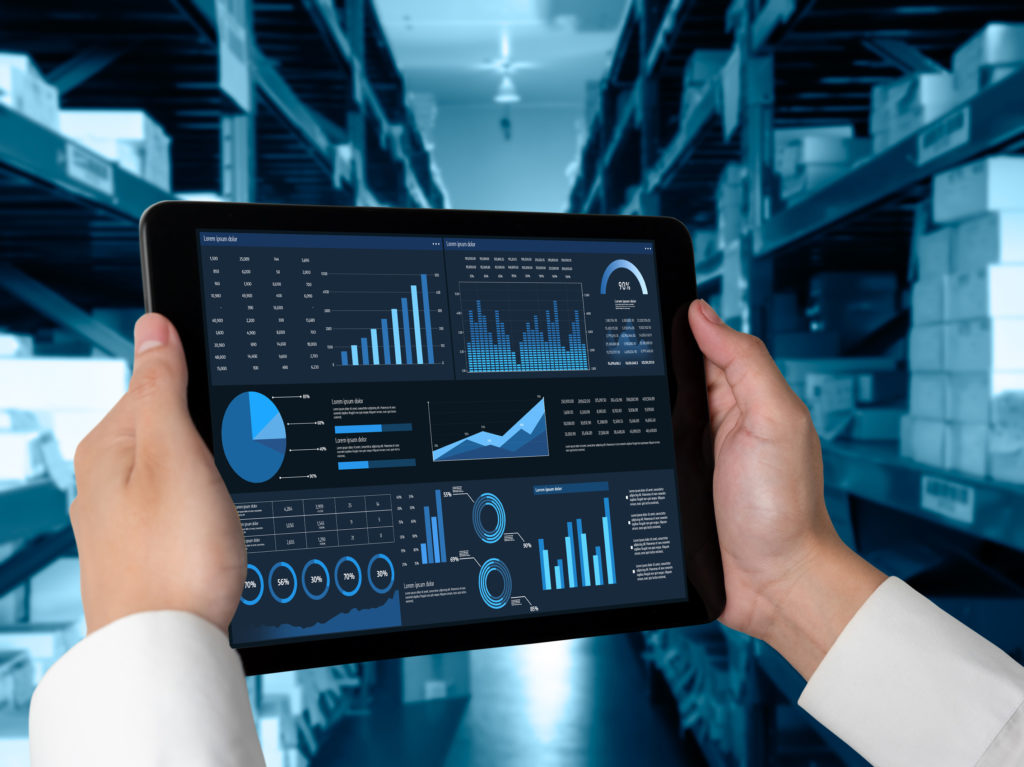
II. Les indicateurs clés à surveiller
Dans la quête de maîtrise des coûts de production, certains indicateurs s’imposent comme des outils indispensables pour éclairer la prise de décision. Ils permettent de comprendre en profondeur les dynamiques financières et opérationnelles qui influencent la rentabilité d’une entreprise.
1. Coût moyen et coût marginal : des piliers de l’analyse
Le coût moyen, ou coût unitaire, est un indicateur fondamental pour évaluer l’efficacité d’un système de production. Il se calcule en divisant le coût total par la quantité produite, donnant ainsi une mesure de la rentabilité par unité. Une baisse continue de ce coût, généralement liée à des économies d’échelle, est un signe de bonne gestion.
Le coût marginal, quant à lui, éclaire sur l’impact financier de la production d’une unité supplémentaire. Cet indicateur devient particulièrement pertinent lorsqu’une entreprise doit décider d’augmenter ou de réduire ses volumes de production. Une hausse du coût marginal au-delà du prix de vente peut signaler une saturation des capacités ou des inefficacités dans le processus.
2. Taux d’utilisation des capacités : une mesure de l’efficience
Le taux d’utilisation des capacités reflète le degré d’exploitation des ressources disponibles, comme les machines ou la main-d’œuvre. Un taux trop bas peut révéler un sous-investissement ou un problème de demande, tandis qu’un taux trop élevé peut entraîner des coûts supplémentaires liés à la maintenance accrue ou à une perte de qualité. L’objectif est de trouver un équilibre permettant d’optimiser les coûts sans compromettre la durabilité des actifs.
3. Coût par unité et économies d’échelle
L’analyse des économies d’échelle est cruciale pour identifier à quel moment l’augmentation des volumes de production réduit les coûts unitaires. Lorsque les coûts fixes se diluent sur une production croissante, le coût par unité baisse, améliorant ainsi la rentabilité. Toutefois, au-delà d’un certain seuil, des déséconomies d’échelle peuvent apparaître, marquées par une hausse des coûts variables ou une perte d’efficacité.
4. Retour sur investissement (ROI) et coûts d’opportunité
Le ROI, ou retour sur investissement, est un indicateur clé pour évaluer la rentabilité des dépenses en capital, comme l’acquisition de nouvelles technologies ou l’expansion des capacités de production. Parallèlement, le coût d’opportunité, souvent négligé, mesure les gains potentiels perdus en choisissant une option plutôt qu’une autre. Ces deux indicateurs aident à prioriser les investissements et à aligner les ressources sur les objectifs stratégiques.
5. La marge opérationnelle : reflet de la performance
En rapportant le résultat opérationnel au chiffre d’affaires, la marge opérationnelle mesure l’efficacité d’une entreprise à transformer ses revenus en bénéfices. Une baisse de cet indicateur peut signaler une hausse des coûts de production, nécessitant une intervention rapide pour réajuster les processus ou repenser les stratégies tarifaires.
6. Les indicateurs environnementaux et sociaux
Dans un contexte où les réglementations et attentes des parties prenantes évoluent, les coûts liés aux impacts environnementaux et sociaux gagnent en importance. Des indicateurs tels que la consommation d’énergie par unité produite ou les émissions de CO₂ peuvent désormais influencer la performance opérationnelle et doivent être intégrés dans l’analyse.
La surveillance régulière de ces indicateurs permet de détecter rapidement les inefficacités, d’anticiper les risques et de saisir les opportunités d’optimisation. En combinant ces outils avec une stratégie dynamique, les entreprises peuvent transformer leurs coûts de production en un levier de compétitivité.
III. Méthodes pour optimiser les coûts
L’optimisation des coûts de production est un défi complexe qui nécessite une approche méthodique et stratégique. Les entreprises qui réussissent à réduire leurs coûts tout en maintenant ou en améliorant la qualité de leurs produits adoptent des méthodes combinant innovation, gestion proactive et intégration technologique.
1. Automatisation et digitalisation des processus
L’automatisation joue un rôle central dans l’optimisation des coûts, notamment en réduisant les dépenses liées à la main-d’œuvre et en minimisant les erreurs humaines. Par exemple, des technologies comme les robots industriels ou les systèmes de convoyage automatisés permettent d’accélérer les cycles de production tout en améliorant leur fiabilité.
La digitalisation, quant à elle, permet une gestion plus fine des processus. Les solutions ERP (Enterprise Resource Planning) modernes intègrent des outils de suivi en temps réel qui aident les entreprises à identifier rapidement les inefficacités. Ces systèmes peuvent surveiller des indicateurs tels que la consommation énergétique ou les taux de rejet, offrant ainsi des leviers d’ajustement immédiats.
2. Optimisation des chaînes d’approvisionnement
La gestion efficace des matières premières et des consommables est cruciale pour réduire les coûts variables. En améliorant la planification des approvisionnements grâce à des outils prédictifs, les entreprises peuvent éviter les surstocks coûteux ou les ruptures de chaîne.
Les partenariats stratégiques avec les fournisseurs offrent également une opportunité d’optimisation. En négociant des contrats à long terme ou en mutualisant les volumes avec d’autres acteurs, les entreprises peuvent réduire significativement leurs coûts d’achat.
3. Maintenance préventive des équipements
Les interruptions de production dues à des pannes imprévues entraînent souvent des coûts élevés, non seulement en termes de réparation, mais aussi en raison des retards dans les livraisons ou des pénalités contractuelles. Une stratégie de maintenance préventive, soutenue par des technologies IoT (Internet des Objets), permet de surveiller l’état des équipements et d’intervenir avant qu’une panne ne se produise. Cette approche réduit les coûts fixes et prolonge la durée de vie des actifs.
4. Réduction des déchets et amélioration de l’efficacité énergétique
L’adoption de méthodes Lean Manufacturing, centrées sur la réduction des gaspillages, constitue un levier efficace pour optimiser les coûts. Qu’il s’agisse de minimiser les rebuts, de recycler les matériaux ou d’améliorer les flux de production, chaque gain contribue directement à la rentabilité.
En parallèle, l’efficacité énergétique devient une priorité croissante. Investir dans des équipements à faible consommation ou adopter des sources d’énergie renouvelable permet de réduire les coûts d’exploitation tout en répondant aux exigences environnementales croissantes.
5. Innovation dans les procédés de production
Les innovations technologiques, telles que l’impression 3D ou les technologies de fabrication additive, offrent des opportunités uniques pour réduire les coûts de production. Ces procédés permettent de produire des pièces complexes avec moins de matière première et de réduire les délais entre la conception et la fabrication.
L’introduction de technologies modulaires ou flexibles favorise également une adaptation rapide aux évolutions du marché, évitant ainsi les surcoûts liés à des processus trop rigides.
6. Formation et engagement des équipes
Les collaborateurs jouent un rôle clé dans l’optimisation des coûts. En les formant à l’utilisation des nouvelles technologies et en les sensibilisant aux pratiques d’amélioration continue, les entreprises peuvent renforcer leur efficacité opérationnelle. Des équipes engagées sont également plus susceptibles de proposer des solutions innovantes et de contribuer à la réduction des gaspillages.
Grâce à ces méthodes, les entreprises peuvent transformer leurs coûts de production en un avantage stratégique. L’optimisation des coûts ne se limite pas à une réduction des dépenses, mais s’inscrit dans une logique d’amélioration continue, combinant innovation, durabilité et performance.
IV. Cas pratiques : interpréter et ajuster les coûts
L’analyse des coûts de production ne peut se limiter à des calculs théoriques. Elle doit être mise en pratique pour guider les décisions opérationnelles et stratégiques. Les cas pratiques permettent de démontrer comment les entreprises peuvent surveiller, analyser et ajuster leurs coûts afin d’améliorer leur rentabilité.
1. Analyse comparative des scénarios : avec ou sans subvention
Prenons l’exemple d’une entreprise devant investir dans une nouvelle machine de production. Dans le premier scénario, l’achat est entièrement financé par un emprunt bancaire, entraînant des frais financiers élevés et un amortissement sur dix ans. Dans le second scénario, une subvention réduit le montant emprunté, diminuant ainsi le coût global.
En analysant ces deux cas, l’entreprise constate que, bien que la subvention ait un impact marginal sur le coût de production unitaire, elle améliore la trésorerie et facilite le remboursement de l’emprunt. Ce type d’analyse souligne l’importance d’intégrer tous les paramètres financiers, y compris les incitations publiques, dans l’évaluation des coûts.
2. Impact des taux d’utilisation des capacités
Un autre cas courant est l’évaluation de l’utilisation des capacités d’une ligne de production. Supposons qu’une entreprise fonctionne à 60 % de sa capacité nominale. Ce sous-emploi entraîne une dilution insuffisante des coûts fixes, ce qui alourdit le coût moyen par unité produite. En optimisant la planification pour atteindre un taux de 85 %, l’entreprise peut réduire ce coût moyen, rendant ses produits plus compétitifs.
3. Ajustement des processus en fonction des coûts marginaux
Le coût marginal est un indicateur clé pour décider d’augmenter ou de réduire la production. Une entreprise fabriquant des composants électroniques peut constater que, au-delà d’un certain volume, l’augmentation des heures supplémentaires et la maintenance accélérée des équipements entraînent une hausse disproportionnée des coûts. Cette analyse permet de fixer un seuil de production optimal au-delà duquel il devient plus rentable d’investir dans une nouvelle capacité que d’accroître la production existante.
4. Optimisation énergétique et réduction des déchets
Dans un contexte où les coûts énergétiques augmentent, un fabricant de biens industriels décide de surveiller en détail la consommation d’électricité de ses machines. En identifiant les équipements les plus énergivores et en les remplaçant par des modèles plus performants, il réduit sa facture énergétique de 15 %, tout en diminuant son empreinte environnementale. Parallèlement, l’analyse des déchets générés par la production permet de recycler certains matériaux, transformant ce qui était une charge en une source de revenus.
5. Réallocation des ressources après analyse des données
Avec un ERP performant, une entreprise textile détecte que certaines étapes de la production consomment plus de main-d’œuvre qu’attendu, entraînant des retards et des coûts supplémentaires. En réorganisant les flux et en automatisant partiellement certaines tâches, elle réduit de 20 % ses coûts de main-d’œuvre et améliore la ponctualité des livraisons.
Toute votre gestion d'entreprise
dans un seul outil.
Leçons tirées des cas pratiques
Ces exemples illustrent comment une analyse rigoureuse des coûts de production permet d’éclairer les décisions et d’optimiser les performances. L’utilisation d’outils tels que des ERP modernes et des indicateurs clés, combinée à une démarche proactive, garantit que chaque ajustement contribue à la rentabilité globale. Au-delà des chiffres, il s’agit d’une approche stratégique visant à transformer les défis en opportunités.
V. Perspectives pour une gestion optimale des coûts
L’évolution rapide des technologies, l’intensification de la concurrence mondiale et les impératifs environnementaux redéfinissent les règles du jeu industriel. Dans ce contexte, la gestion des coûts de production ne se limite plus à une simple rationalisation des dépenses : elle devient un levier stratégique pour l’innovation, la durabilité et la croissance.
1. Intégration des nouvelles technologies
La transition vers l’industrie 4.0 ouvre des perspectives prometteuses pour la gestion des coûts. Des technologies comme l’Internet des Objets (IoT), le Big Data et l’intelligence artificielle permettent de collecter et d’analyser en temps réel des volumes massifs de données. Ces outils offrent une visibilité accrue sur les flux de production, permettant d’identifier rapidement les inefficacités et de prendre des décisions basées sur des faits.
Par exemple, un ERP intelligent peut intégrer des algorithmes prédictifs pour anticiper les besoins en maintenance, réduire les temps d’arrêt imprévus et optimiser l’utilisation des ressources. Ces technologies transforment les coûts fixes et variables en opportunités d’amélioration continue.
2. Vers une gestion axée sur la durabilité
Les attentes croissantes en matière de responsabilité environnementale et sociale modifient également la gestion des coûts. Les entreprises doivent désormais intégrer des indicateurs environnementaux et sociaux dans leur analyse financière, tels que la consommation énergétique par unité produite ou les émissions de gaz à effet de serre.
Investir dans des équipements écoénergétiques ou adopter des processus plus respectueux de l’environnement peut représenter un surcoût initial, mais ces initiatives génèrent des économies substantielles à long terme. Elles permettent également de renforcer l’attractivité des entreprises auprès des investisseurs et des clients sensibles aux questions de durabilité.
3. L’humain au cœur de l’optimisation des coûts
Si les technologies jouent un rôle clé, les collaborateurs restent essentiels pour garantir le succès des initiatives d’optimisation. Former les équipes aux nouvelles technologies et les impliquer dans les démarches d’amélioration continue crée un cercle vertueux. Les retours des employés permettent d’identifier des inefficacités que les systèmes automatisés ne détectent pas toujours.
De plus, les entreprises qui cultivent une culture d’innovation et d’engagement réussissent mieux à mobiliser leurs talents pour relever les défis liés à la réduction des coûts, tout en maintenant des standards de qualité élevés.
4. Anticiper les évolutions du marché
Dans un environnement économique en constante mutation, les entreprises doivent faire preuve d’agilité pour rester compétitives. La gestion des coûts de production doit inclure une anticipation des fluctuations des prix des matières premières, des variations des taux de change et des nouvelles réglementations.
Les outils de simulation et les modèles prédictifs permettent de scénariser ces évolutions et d’ajuster les stratégies en conséquence. Par exemple, une entreprise peut modéliser l’impact d’une hausse des prix de l’énergie sur ses marges et prendre des mesures préventives pour limiter cet effet.
5. Vers une approche intégrée et collaborative
La gestion des coûts de production ne peut plus être envisagée de manière isolée. Une collaboration étroite avec les fournisseurs, les clients et les partenaires logistiques permet d’optimiser l’ensemble de la chaîne de valeur. Par exemple, la mutualisation des ressources ou la co-innovation avec des partenaires peut réduire les coûts tout en améliorant l’efficacité opérationnelle.
Les ERP modernes favorisent cette intégration en offrant des interfaces collaboratives qui alignent les objectifs des différents acteurs de la chaîne de valeur.
Une gestion des coûts pour l’avenir
La gestion optimale des coûts de production repose sur une combinaison d’innovations technologiques, d’approches collaboratives et d’un engagement en faveur de la durabilité. En intégrant ces éléments dans leur stratégie, les entreprises peuvent transformer les défis actuels en opportunités de croissance et de compétitivité. La clé réside dans une vision proactive, soutenue par des outils adaptés et une culture tournée vers l’amélioration continue.
En savoir plus
Retrouvez l’ensemble de nos ressources pour accroître vos connaissances sur l’ERP pour le domaine industriel.
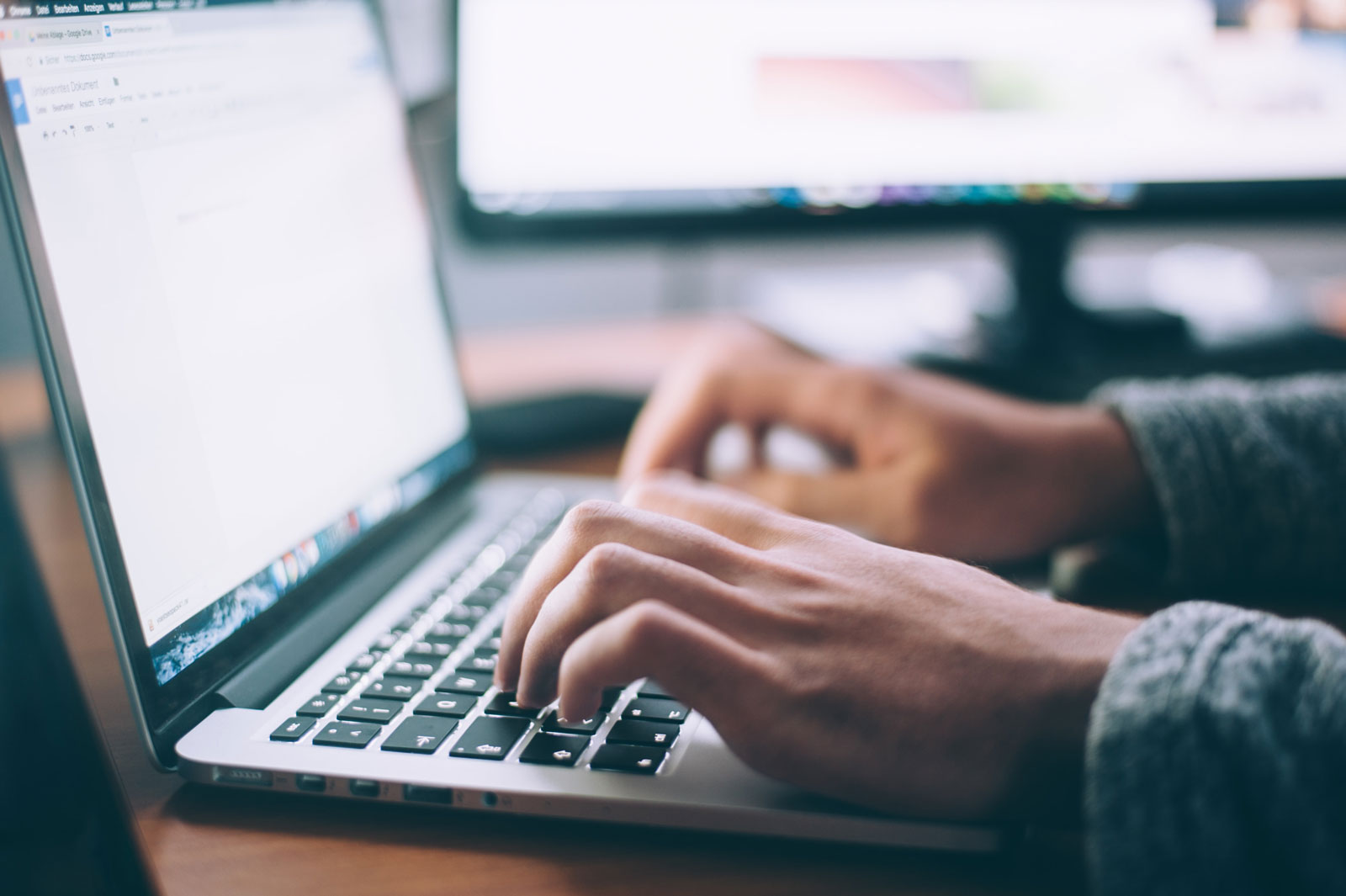
Retrouvez l’ensemble des réponses fonctionnelles de l’ERP Open-Prod aux différents secteurs industriels.
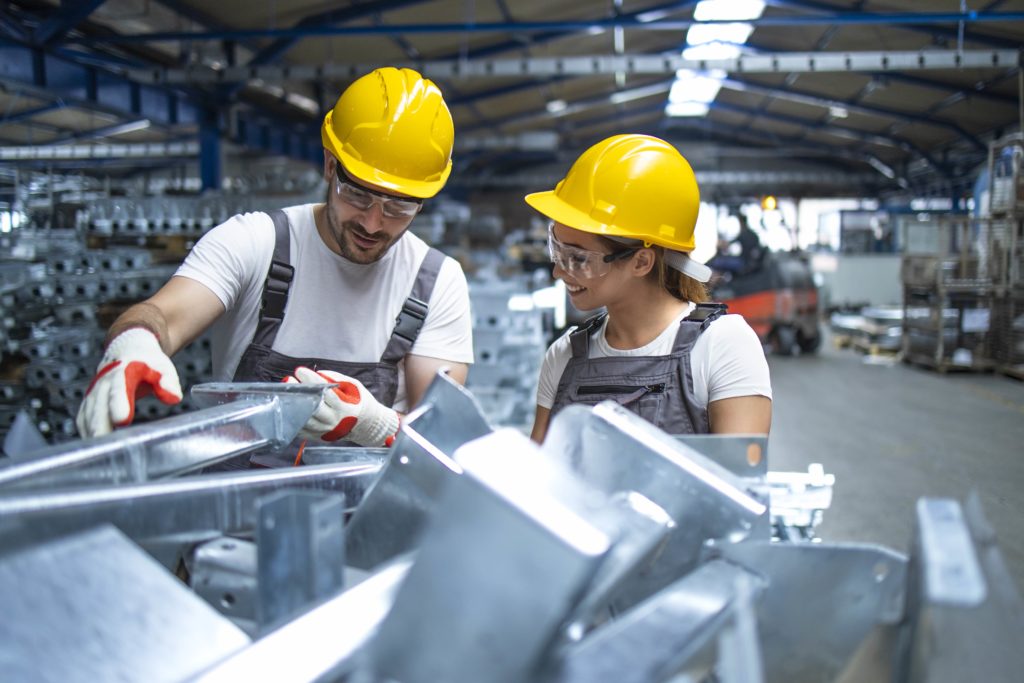
Découvrez les +200 modules d’Open-Prod conçus pour répondre aux besoins des entreprises industrielles.
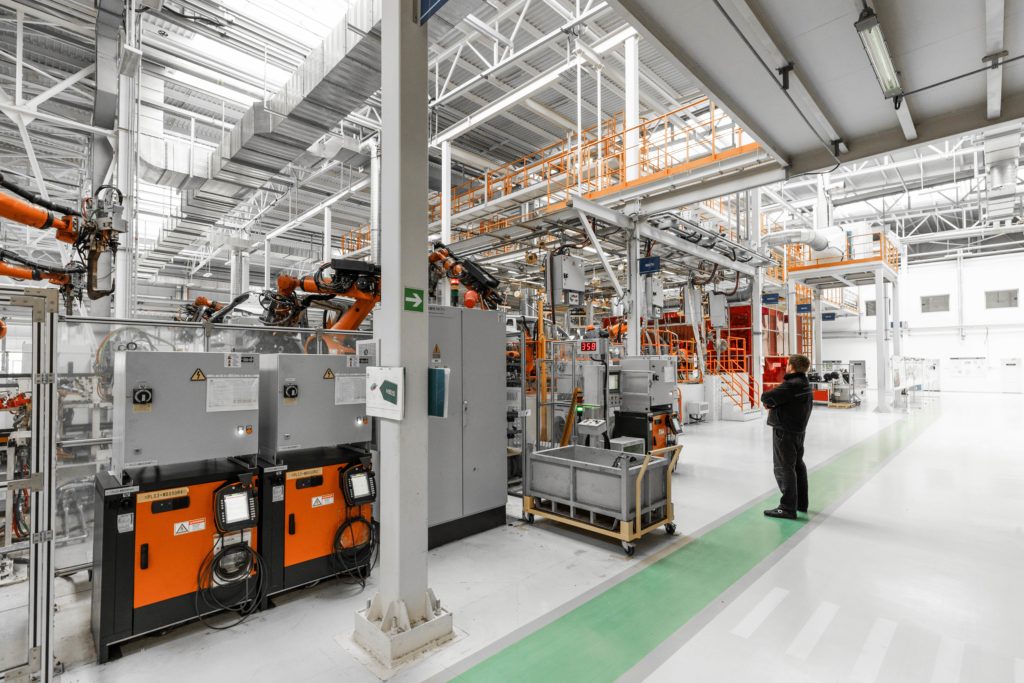