La synergie entre les logiciels de gestion de production et les principes du lean manufacturing
L’identification des gaspillages, pierre angulaire du lean manufacturing, trouve un allié puissant dans les capacités analytiques des logiciels de gestion de production. Ces systèmes, en collectant et en analysant en temps réel des données sur l’ensemble du processus de production, permettent de mettre en lumière les inefficacités souvent invisibles à l’œil nu. Prenons l’exemple de l’usine Bosch de Rodez, spécialisée dans la production de composants automobiles. En intégrant un système de gestion de production avancé à sa démarche lean, l’entreprise a pu identifier avec précision les sources de gaspillage dans son processus de fabrication d’injecteurs diesel. Le système a révélé des temps d’attente excessifs entre certaines étapes de production, permettant à Bosch de revoir son flux de travail et de réduire ces temps morts de 30%, augmentant ainsi significativement la productivité de l’usine.
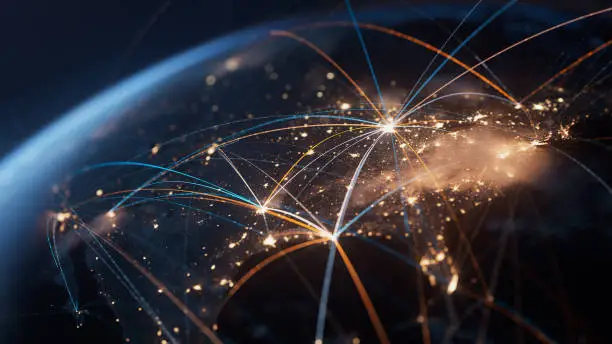
La standardisation des processus, autre pilier du lean manufacturing, bénéficie grandement de l’apport des logiciels de gestion de production. Ces outils permettent de définir, documenter et diffuser des procédures opérationnelles standardisées (SOP) à l’échelle de l’entreprise. L’exemple de Safran Aircraft Engines est particulièrement éloquent à cet égard. Le fabricant de moteurs d’avion a déployé un système de gestion de production intégré qui guide les opérateurs à travers chaque étape du processus de fabrication, assurant une exécution cohérente et de haute qualité. Cette standardisation numérique a non seulement réduit les variations de qualité, mais a également facilité la formation des nouveaux employés, réduisant le temps de montée en compétence de 25%.
La création d’une culture d’amélioration continue, essence même du kaizen dans le lean manufacturing, est catalysée par les capacités de collecte et d’analyse de données des logiciels de gestion de production. Ces systèmes fournissent une base factuelle pour l’identification des opportunités d’amélioration et le suivi des progrès réalisés. L’exemple de Schneider Electric est particulièrement instructif à cet égard. Dans son usine de Lexington, Kentucky, l’entreprise a mis en place un « Digital Lean Management System » qui combine les principes du lean avec une plateforme numérique de gestion de la production. Ce système permet aux équipes de visualiser en temps réel les KPIs de performance, de détecter rapidement les anomalies et de lancer des initiatives d’amélioration basées sur des données concrètes. Grâce à cette approche, Schneider Electric a pu réduire ses coûts de production de 20% et augmenter sa productivité de 15% en trois ans.
Toute votre gestion d'entreprise
dans un seul outil.
L‘intégration des logiciels de gestion de production dans une démarche lean permet également d’amplifier l’efficacité des outils traditionnels du lean manufacturing. Par exemple, le concept de Jidoka (automatisation avec une touche humaine) trouve une nouvelle dimension avec ces systèmes. Chez Toyota, pionnier du lean manufacturing, l’usine de Georgetown, Kentucky, a intégré son système andon (système d’alerte visuelle) à son logiciel de gestion de production. Désormais, non seulement les problèmes sont signalés visuellement sur la ligne, mais le système peut automatiquement ajuster la planification de la production pour minimiser l’impact des arrêts, optimisant ainsi la réactivité et la flexibilité de l’usine.
En conclusion, la synergie entre les logiciels de gestion de production et le lean manufacturing offre aux entreprises industrielles un puissant levier pour atteindre l’excellence opérationnelle. Les MES fournissent les outils technologiques nécessaires pour mettre en œuvre efficacement les principes du lean, offrant une visibilité en temps réel, une capacité d’analyse avancée et une agilité accrue dans la gestion des opérations. Cette combinaison permet aux entreprises de réduire les gaspillages, d’améliorer la qualité, d’augmenter la productivité et de répondre plus efficacement aux demandes du marché.
En savoir plus
Retrouvez l’ensemble de nos ressources pour accroître vos connaissances sur l’ERP pour le domaine industriel.
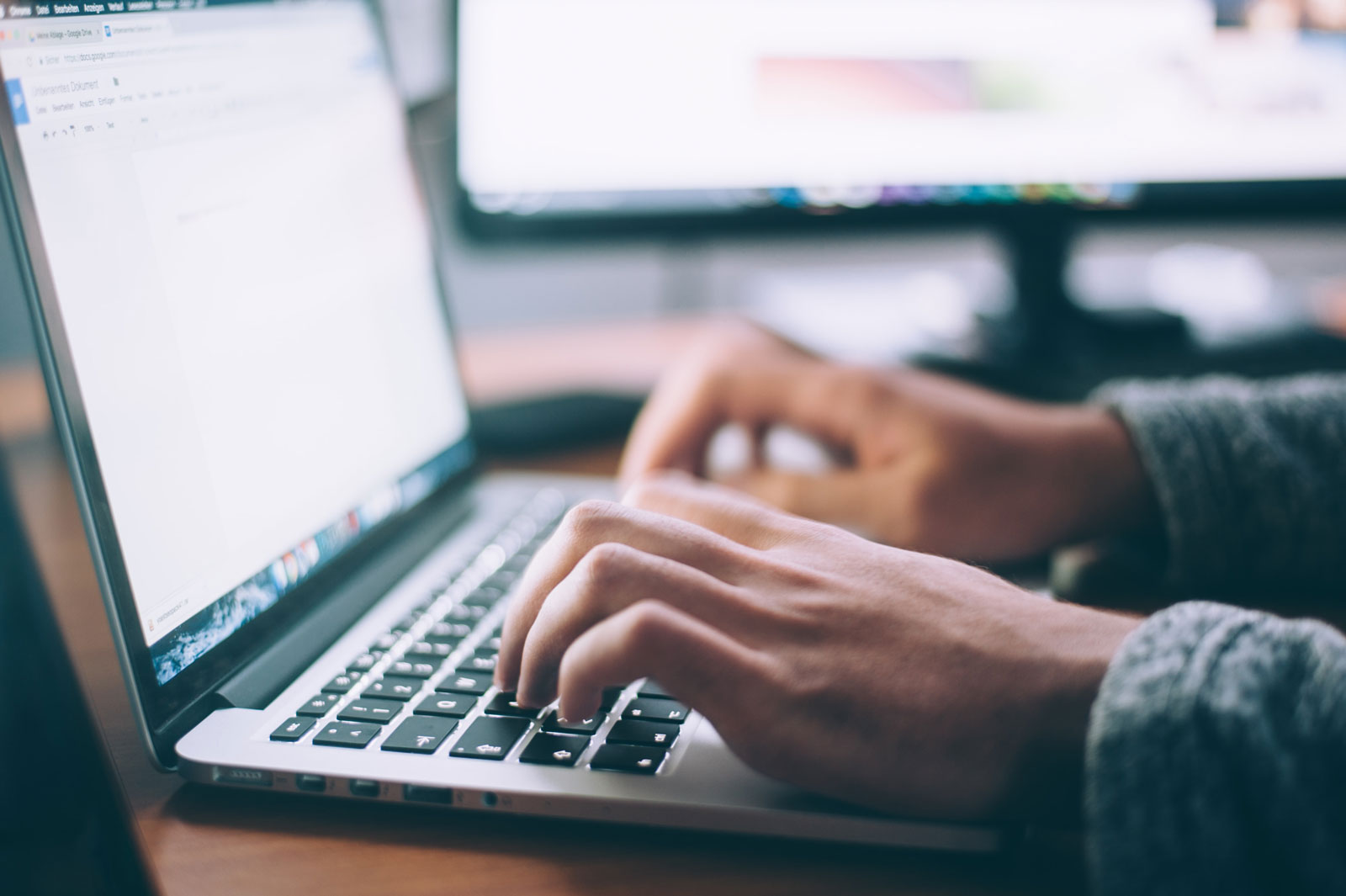
Retrouvez l’ensemble des réponses fonctionnelles de l’ERP Open-Prod aux différents secteurs industriels.
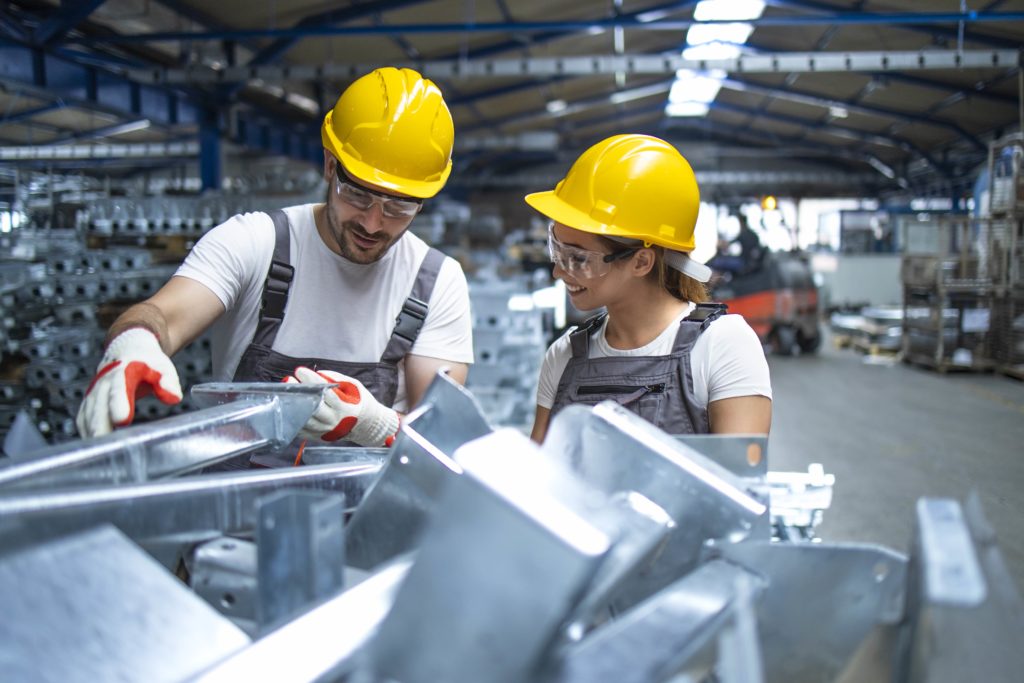
Découvrez les +200 modules d’Open-Prod conçus pour répondre aux besoins des entreprises industrielles.
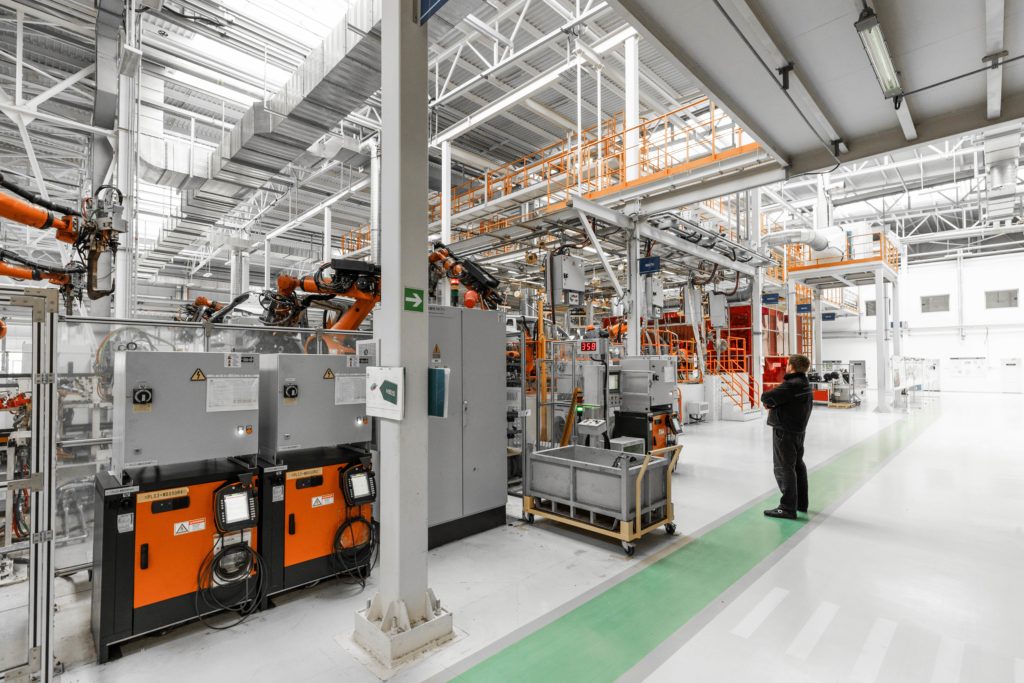