Les enjeux de l'optimisation industrielle : de la suroptimisation à la sous-optimisation dans la gestion de la performance
Comprendre les enjeux de l'optimisation industrielle
Dans l'industrie, l'optimisation des processus est un levier essentiel pour améliorer les performances et répondre aux exigences croissantes en termes de qualité, de coûts et de délais. Les notions d'optimisation normale, forte et de suroptimisation révèlent les niveaux auxquels les entreprises ajustent leurs opérations afin d'atteindre un équilibre optimal entre les différentes variables influençant la production. Une optimisation efficace permet d'améliorer la productivité en utilisant les bons outils, les solutions adaptées, et une gestion rigoureuse des processus. La compréhension de ces concepts est ainsi indispensable pour ajuster les stratégies d'optimisation selon les besoins spécifiques de l'entreprise et ses objectifs de performance. Le suivi des indicateurs comme le Taux de Rendement Synthétique (TRS) joue un rôle déterminant dans cette démarche en fournissant des mesures précises de l'efficacité opérationnelle.
Suroptimisation : Les limites d'une performance maximale
La suroptimisation dans un contexte industriel se traduit par un ajustement excessif des paramètres de production dans le but de maximiser un indicateur particulier, souvent au détriment d'autres aspects du processus. Par exemple, en cherchant à maximiser la cadence d'une machine, le risque est d'accroître les taux de défaillance ou de réduire la qualité des produits finis en raison de l'usure prématurée des équipements. Une optimisation excessive entraîne souvent une baisse de la flexibilité, limitant la capacité de l'entreprise à adapter ses processus en fonction des variations de la demande. Le TRS, en tant qu'indicateur clé, permet de mesurer l'impact d'une suroptimisation sur la productivité réelle en prenant en compte non seulement la vitesse de production, mais aussi les arrêts et les défauts.
L'utilisation d'un logiciel de gestion de la production assistée par ordinateur (GPAO), tel que les solutions ERP comme Open-Prod, peut aider à identifier les effets de la suroptimisation. Les outils d'analyse fournis par ces logiciels permettent de détecter les ajustements excessifs et d'adopter une approche plus équilibrée dans la planification des opérations. Par exemple, la gestion des stocks peut être optimisée pour éviter les ruptures sans toutefois réduire les niveaux à un point qui compromettrait la continuité des opérations.
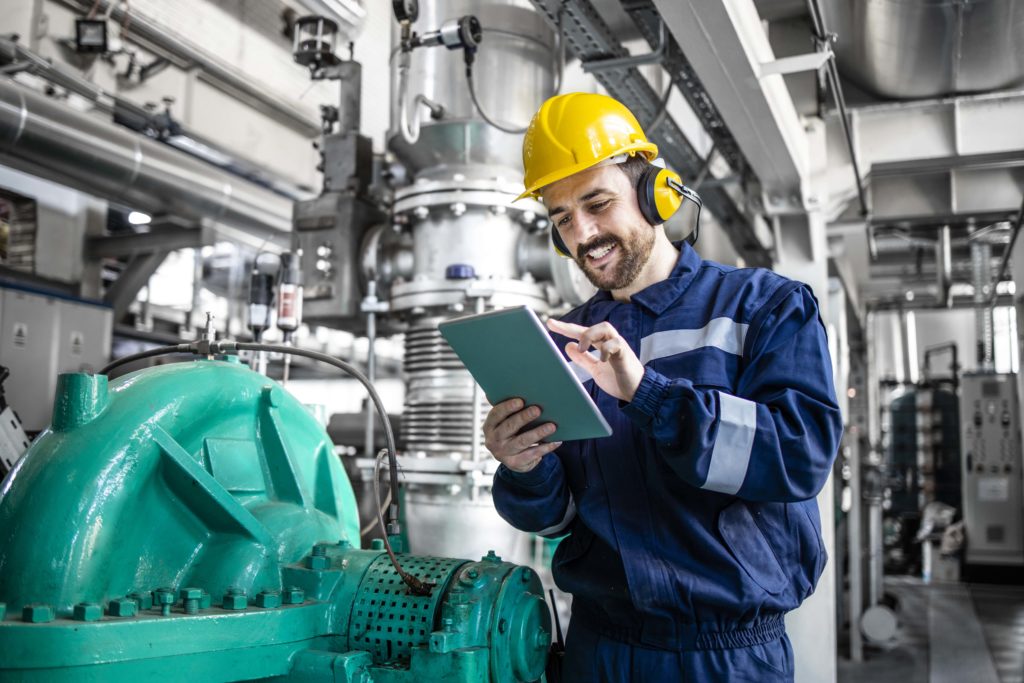
Optimisation forte : Trouver l'équilibre pour une performance élevée
L'optimisation forte vise à atteindre des niveaux de performance élevés tout en préservant la stabilité et la flexibilité du système de production. Elle repose sur une approche plus équilibrée, où l'ajustement des paramètres de production permet d'améliorer les indicateurs de performance sans pour autant compromettre la durabilité des équipements ni la qualité des produits. Pour atteindre ce niveau d'optimisation, il est nécessaire de combiner des données précises sur les performances des machines, les taux de production, les taux de rejet, et les coûts d'entretien. La mesure du TRS est essentielle pour suivre les améliorations et ajuster les processus en conséquence.
Les solutions logicielles ERP contribuent à cette démarche en intégrant les informations de diverses sources pour fournir une vue synthétique et actualisée de l'état du système de production. Par exemple, les fonctionnalités d'un ERP comme Open-Prod permettent de suivre les indicateurs de performance en temps réel, d'analyser les cycles de maintenance préventive et corrective, et d'ajuster les cadences de production en fonction des données collectées. Les outils proposés par ces logiciels facilitent l'optimisation de la gestion des ressources et de la planification des interventions sur les équipements, contribuant ainsi à une meilleure productivité.
Optimisation normale : Maintenir une performance acceptable avec des ressources limitées
L'optimisation normale consiste à maintenir un niveau de performance jugé acceptable, en tenant compte des contraintes de ressources, qu'elles soient matérielles, humaines ou financières. Ce type d'optimisation est souvent utilisé dans des environnements industriels où les marges d'amélioration sont limitées en raison des caractéristiques techniques des équipements ou des restrictions budgétaires. L'objectif est d'atteindre une efficacité opérationnelle suffisante pour garantir la satisfaction des exigences minimales en termes de qualité et de délais, tout en optimisant l'utilisation des ressources disponibles.
Dans ce cadre, la gestion des arrêts programmés et la planification des cycles de maintenance jouent un rôle central. Les mesures du TRS permettent de suivre l'impact des interventions sur les équipements et d'identifier les meilleures pratiques pour réduire les pertes de disponibilité. Les outils logiciels, tels que les ERP, offrent des solutions pour gérer ces arrêts de manière plus efficace. Ils permettent, par exemple, d'automatiser la planification des interventions et de s'assurer que les opérations de maintenance sont exécutées dans les délais les plus opportuns.
Sous-optimisation : Les risques d'une gestion insuffisante des performances
La sous-optimisation désigne une situation où le potentiel de performance des systèmes de production n'est pas pleinement exploité, souvent en raison d'une gestion inadéquate des ressources ou d'un manque d'investissement dans les technologies et les processus d'amélioration. Cela peut conduire à une baisse de la productivité, une augmentation des coûts de production, et une dégradation de la qualité des produits. Le TRS peut révéler des marges d'amélioration non exploitées, que ce soit dans l'optimisation des processus, la gestion des équipements, ou encore la planification de la production.
Les solutions logicielles comme Open-Prod fournissent des outils permettant d'identifier les sources de sous-optimisation et de mettre en œuvre des mesures correctives. En utilisant les données collectées sur les performances des équipements et les taux de production, il devient possible d'ajuster les stratégies d'amélioration pour combler les lacunes identifiées. Cela inclut, par exemple, le recours à la maintenance prédictive pour minimiser les arrêts imprévus et optimiser l'utilisation des machines.
Analyse et gestion de la performance : Outils et indicateurs clés
L'amélioration de la performance industrielle repose sur une analyse continue et rigoureuse des données issues des systèmes de production. Les indicateurs tels que le TRS, les taux de rejet, et les temps d'arrêt des équipements sont essentiels pour identifier les goulots d'étranglement et les opportunités d'optimisation. Les logiciels de gestion tels que les ERP intègrent ces données, permettant une vue d'ensemble des performances tout en offrant des outils pour simuler différents scénarios d'amélioration.
La mesure en temps réel des indicateurs de performance offre aux gestionnaires une capacité d'analyse accrue, leur permettant d'ajuster rapidement les paramètres de production pour maximiser l'efficacité. Les solutions logicielles jouent ici un rôle crucial en automatisant la collecte et le traitement des données. Cette réactivité est particulièrement utile dans le cadre de l'industrie 4.0, où les systèmes cyber-physiques nécessitent une coordination précise entre les différentes composantes de l'usine. L'ERP Open-Prod, en intégrant les données de bord de ligne, permet d'adopter des stratégies d'amélioration plus dynamiques et adaptées aux conditions réelles de l'usine.
Toute votre gestion d'entreprise
dans un seul outil.
La gestion des arrêts et l'amélioration continue : Un cycle de révision permanente
La gestion des arrêts, qu'ils soient programmés ou imprévus, représente un défi constant pour les entreprises cherchant à optimiser leurs performances industrielles. Les stratégies de réduction des temps d'arrêt doivent être intégrées dans un cycle d'amélioration continue où chaque arrêt est analysé afin d'identifier les causes sous-jacentes et les solutions possibles. Les outils d'analyse fournis par les logiciels de gestion permettent d'affiner les stratégies de maintenance et d'amélioration, garantissant une utilisation optimale des équipements et une productivité accrue.
La démarche d'amélioration continue implique une révision régulière des procédures de production, la mise à jour des protocoles de maintenance, et l'ajustement des paramètres opérationnels en fonction des données historiques et en temps réel. Les solutions logicielles ERP, en consolidant ces informations, facilitent la mise en œuvre de ces pratiques et contribuent à l'atteinte d'une efficacité opérationnelle accrue. Les indicateurs de mesure comme le TRS permettent de suivre l'évolution des performances et d'ajuster les stratégies d'amélioration en fonction des résultats obtenus.
Vers une optimisation maîtrisée et durable des processus industriels
L'optimisation industrielle ne se résume pas à maximiser un unique indicateur de performance, mais nécessite une approche globale et équilibrée. Les différents niveaux d'optimisation – de la suroptimisation à la sous-optimisation – doivent être envisagés en fonction des objectifs de performance, des ressources disponibles, et de la capacité à réagir aux variations du contexte industriel. L'utilisation d'outils logiciels comme les solutions ERP d'Open-Prod et de stratégies d'amélioration continue permet d'ajuster les paramètres de production et de gestion des équipements, favorisant une optimisation maîtrisée et durable. Les mesures comme le TRS aident à piloter ces ajustements en temps réel pour garantir des performances stables et évolutives.
En savoir plus
Retrouvez l’ensemble de nos ressources pour accroître vos connaissances sur l’ERP pour le domaine industriel.
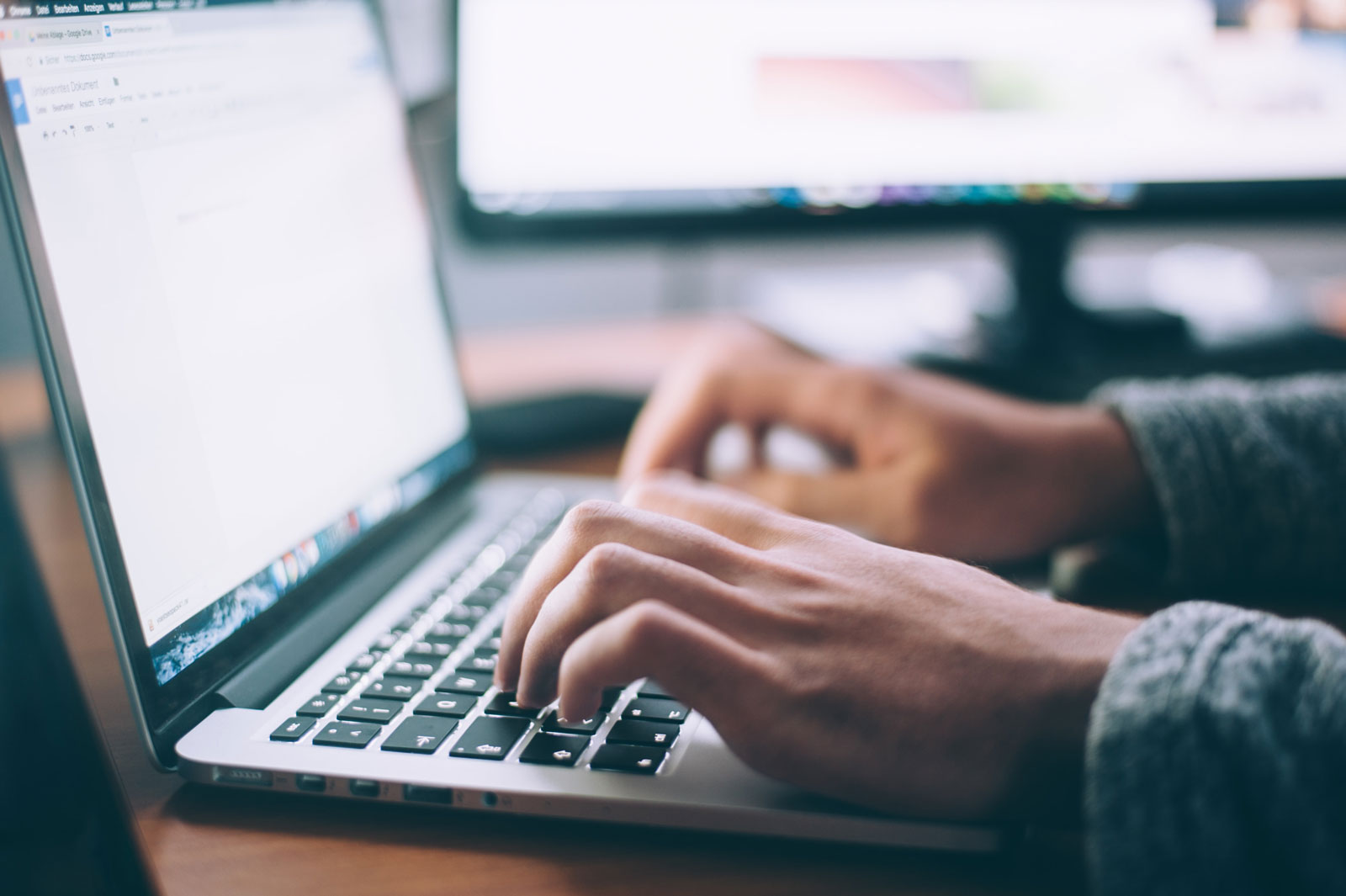
Retrouvez l’ensemble des réponses fonctionnelles de l’ERP Open-Prod aux différents secteurs industriels.
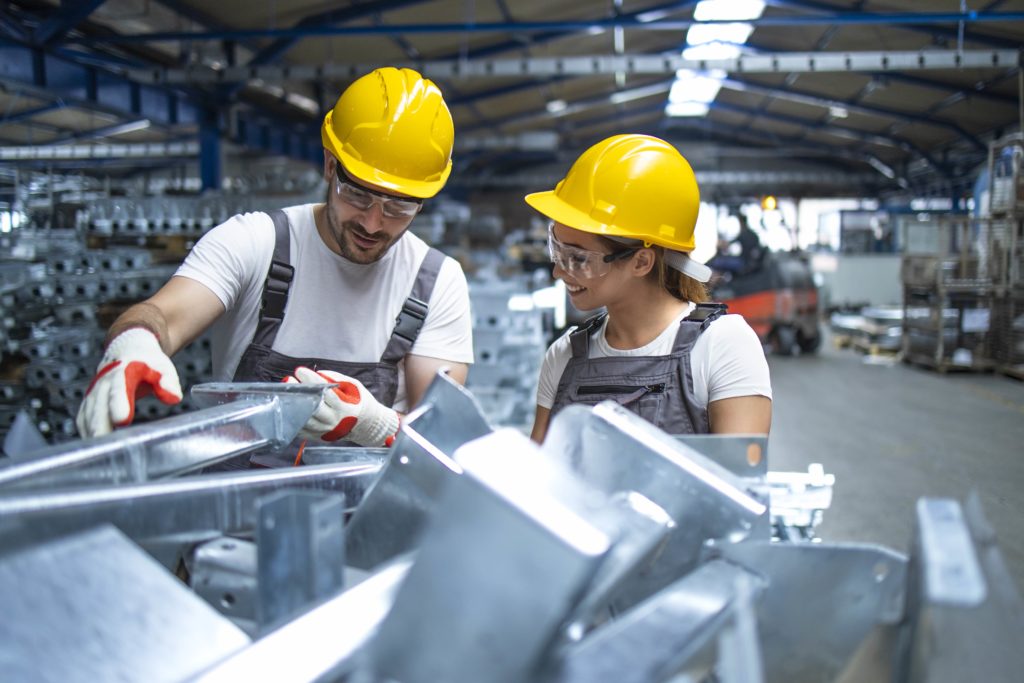
Découvrez les +200 modules d’Open-Prod conçus pour répondre aux besoins des entreprises industrielles.
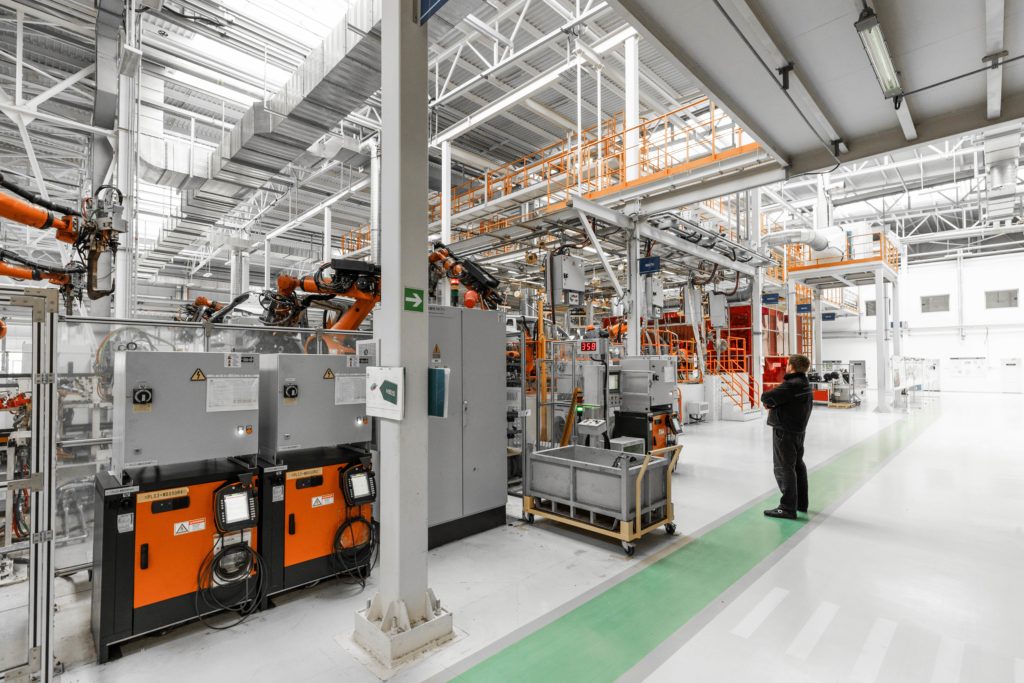