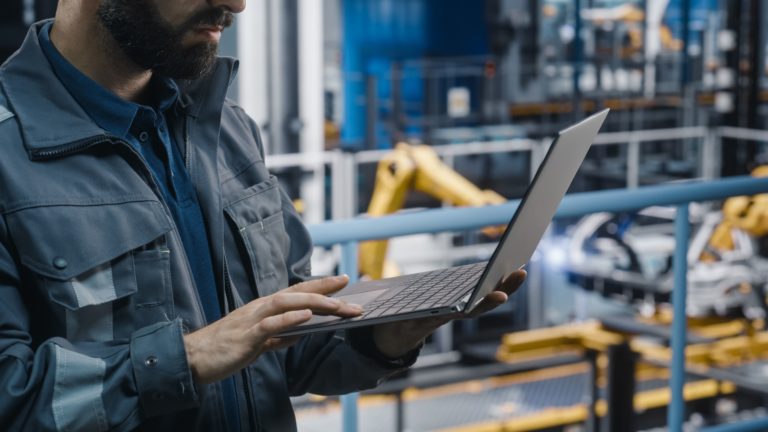
Méthodes de gestion logistique et de flux : Just-in-time et théorie des contraintes
Dans l'environnement industriel contemporain, l'optimisation des flux logistiques représente un enjeu stratégique majeur pour maintenir la compétitivité des entreprises. Deux approches se distinguent particulièrement par leur efficacité et leur impact sur les performances : le Just-In-Time (JIT) et la Théorie des Contraintes (TOC). Ces méthodologies, bien que distinctes dans leurs principes, partagent l'objectif commun d'améliorer l'efficience opérationnelle et de maximiser la valeur créée.

Le Just-In-Time : L'art de produire au bon moment
Origines et principes fondamentaux
Le Just-In-Time (JIT), ou production à flux tendu, est une méthodologie développée au Japon par Toyota dans les années 1950 sous l'impulsion de Taiichi Ohno. Ce concept révolutionnaire repose sur un principe simple mais puissant : produire uniquement ce qui est nécessaire, quand c'est nécessaire, et dans les quantités nécessaires.
Contrairement aux approches traditionnelles qui privilégient la production en grandes séries pour réaliser des économies d'échelle, le JIT vise à synchroniser parfaitement la production avec la demande réelle. Cette synchronisation permet d'éliminer les sept gaspillages identifiés par le Système de Production Toyota :
- La surproduction
- Les temps d’attente
- Les transports inutiles
- Les traitements inappropriés
- Les stocks excédentaires
- Les mouvements inutiles
- Les défauts et retouches
Le système JIT peut être résumé par la formule "5Z" : zéro défaut, zéro délai, zéro papier, zéro panne et zéro stock.
Mise en œuvre et outils associés
L'implémentation du JIT s'appuie sur plusieurs techniques et outils complémentaires :
Le système Kanban, élément central du JIT, utilise des cartes ou signaux visuels pour déclencher la production ou l'approvisionnement uniquement lorsque cela est nécessaire.
Ce mécanisme de flux tiré garantit que chaque poste ne produit que ce qui est demandé par le poste en aval, évitant ainsi toute accumulation de stock intermédiaire.
La réduction des temps de changement (technique SMED - Single Minute Exchange of Die) permet de diminuer drastiquement les temps de mise en course des machines, rendant économiquement viable la production en petites séries. L'aménagement cellulaire des ateliers facilite quant à lui la circulation des produits en réduisant les distances de transport.
Le lissage de la production (Heijunka) vise à répartir uniformément la charge de travail, tant en volume qu'en variété, pour éviter les pics et les creux d'activité. Enfin, la standardisation des processus établit les meilleures pratiques pour chaque opération, garantissant constance et qualité.
Bénéfices et défis
Les avantages du JIT pour une entreprise sont multiples et significatifs :
La réduction drastique des niveaux de stocks (matières premières, en-cours et produits finis) libère le capital immobilisé et réduit les coûts de stockage. L'amélioration de la qualité découle naturellement de la détection immédiate des problèmes, puisque l'absence de stocks tampons rend visible tout dysfonctionnement. La flexibilité accrue permet de s'adapter rapidement aux évolutions de la demande, tandis que l'optimisation de l'espace de production résulte de la diminution des zones de stockage.
Cependant, le JIT présente également des défis considérables :
La dépendance envers les fournisseurs exige une relation de partenariat solide et fiable. La vulnérabilité aux perturbations peut paralyser toute la chaîne de production en cas d'imprévus (comme l'ont démontré la crise COVID-19 et diverses catastrophes naturelles). La nécessité d'une discipline rigoureuse impose une transformation culturelle profonde dans l'entreprise.
Application contemporaine
Aujourd'hui, le JIT évolue vers des formes plus sophistiquées intégrant les technologies numériques. L'Internet des Objets Industriel (IIoT) permet désormais une surveillance en temps réel des flux et des stocks. Les systèmes d'information avancés facilitent la coordination entre clients et fournisseurs, tandis que l'intelligence artificielle offre des capacités prédictives pour anticiper les variations de la demande.
Des entreprises comme Zara dans le textile, Dell dans l'informatique ou Tesla dans l'automobile ont adapté les principes du JIT à leurs contextes spécifiques, démontrant la versatilité et la pérennité de cette approche.
Toute votre gestion d'entreprise
dans un seul outil.
La Théorie des Contraintes : Optimiser le système dans sa globalité
Fondements conceptuels
La Théorie des Contraintes (Theory of Constraints - TOC) a été développée par le physicien israélien Eliyahu Goldratt dans les années 1980 et exposée dans son ouvrage emblématique "Le But". Cette approche systémique repose sur une métaphore simple mais puissante : la résistance d'une chaîne est déterminée par son maillon le plus faible.
Selon la TOC, chaque système possède au moins une contrainte qui limite sa performance globale. Une contrainte (ou goulot d'étranglement) représente toute ressource dont la capacité est inférieure à la demande qui lui est adressée. Il peut s'agir d'une machine, d'un poste de travail, d'une compétence spécifique, ou même d'une politique d'entreprise inadaptée.
L'originalité de la TOC réside dans son approche holistique : plutôt que d'optimiser chaque composant indépendamment, elle propose de se concentrer sur l'amélioration des contraintes du système pour maximiser la performance globale.
Processus d'amélioration continue
La TOC s'articule autour d'un processus d'amélioration continue en cinq étapes :
- Identifier la contrainte : Déterminer le facteur qui limite actuellement la performance du système.
- Exploiter la contrainte : Tirer le maximum de la ressource contrainte sans investissement majeur.
- Subordonner tout le reste à la décision précédente : Aligner l’ensemble du système pour soutenir l’exploitation optimale de la contrainte.
- Élever la contrainte : Si nécessaire, investir pour augmenter la capacité de la ressource contrainte.
- Revenir à l’étape 1 : Une fois la contrainte éliminée, identifier la nouvelle contrainte qui apparaît.
Ce cycle encourage une amélioration continue du système en ciblant systématiquement le facteur limitant.
Outils et techniques
La TOC propose plusieurs outils pour son application pratique :
Le Drum-Buffer-Rope (Tambour-Tampon-Corde) est une méthode de planification et de contrôle de la production qui synchronise l'ensemble du système autour de la contrainte. Le tambour représente le rythme imposé par la contrainte, le tampon protège la contrainte contre les perturbations, et la corde assure que les matériaux sont libérés au bon moment.
La méthode des Thinking Processes fournit un ensemble d'outils logiques pour analyser et résoudre des problèmes complexes. Le Throughput Accounting (comptabilité du débit) propose quant à lui une approche comptable alternative adaptée aux principes de la TOC, avec trois métriques principales : le débit (throughput), les stocks (inventory) et les dépenses d'exploitation (operating expenses).
Applications et bénéfices
La TOC trouve des applications dans de nombreux domaines industriels :
Dans la production, elle permet d'optimiser les flux en fonction des contraintes identifiées, augmentant ainsi le débit global. En gestion de projet, la méthode de la Chaîne Critique (Critical Chain Project Management) améliore le respect des délais en gérant efficacement les ressources critiques et les marges de sécurité. Dans la distribution, la TOC propose des modèles de réapprovisionnement basés sur la consommation réelle plutôt que sur des prévisions.
Les bénéfices typiques d'une implémentation réussie incluent :
- Augmentation significative du débit (20% à 50%)
- Réduction des délais de fabrication et de livraison
- Diminution des stocks
- Amélioration de la ponctualité
- Simplification de la gestion
Des entreprises comme Boeing, Amazon ou Lucent Technologies ont appliqué avec succès les principes de la TOC pour surmonter leurs limitations opérationnelles.
Complémentarité entre JIT et TOC
Bien que développées indépendamment et reposant sur des philosophies différentes, le JIT et la TOC peuvent être considérés comme complémentaires plutôt que concurrents.
Le JIT excelle dans l'élimination systématique des gaspillages à travers l'ensemble du processus, créant un flux régulier et fluide. La TOC, quant à elle, focalise l'attention sur les points critiques qui limitent la performance globale, orientant les efforts d'amélioration là où ils auront le plus d'impact.
Dans une approche intégrée, la TOC peut fournir la direction stratégique en identifiant les contraintes du système, tandis que le JIT peut être déployé tactiquement pour optimiser les flux autour de ces contraintes.
Évolution vers l'Industrie 4.0
L'émergence des technologies de l'Industrie 4.0 ouvre de nouvelles perspectives pour ces méthodologies :
La digitalisation des chaînes d'approvisionnement facilite l'implémentation du JIT en améliorant la visibilité et la coordination entre les acteurs. Les jumeaux numériques et la simulation permettent d'identifier et d'analyser les contraintes de manière plus précise et dynamique. L'intelligence artificielle peut suggérer des ajustements en temps réel pour optimiser les flux en fonction des variations de la demande ou des perturbations opérationnelles.
Conclusion
Le Just-In-Time et la Théorie des Contraintes représentent deux approches complémentaires pour l'optimisation des flux logistiques et industriels. Tandis que le JIT propose une élimination systématique des gaspillages pour créer un flux tendu et réactif, la TOC offre une méthode structurée pour identifier et exploiter les leviers d'amélioration les plus impactants.
Dans un contexte économique caractérisé par la volatilité des marchés et l'intensification de la concurrence, ces méthodologies s'avèrent plus pertinentes que jamais. Leur intégration aux technologies numériques émergentes pourrait constituer un facteur déterminant de compétitivité pour les entreprises industrielles du XXIe siècle.
Pour les dirigeants et responsables opérationnels, le défi consiste désormais à adopter ces approches non pas comme de simples techniques d'optimisation, mais comme des philosophies managériales transformantes, capables de redéfinir fondamentalement la façon dont les flux sont gérés au sein de leurs organisations.
Découvrir nos autres dossiers
Retrouvez l’ensemble de nos articles sur l’IA, son rôle et ses enjeux dans l’industrie du futur
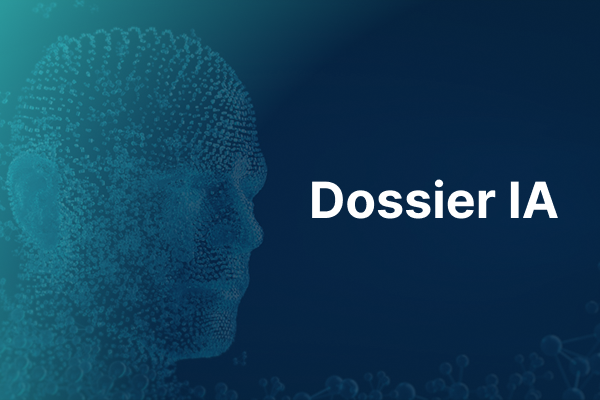
Retrouvez l’ensemble de nos articles sur l’IIoT, son rôle et ses enjeux dans l’industrie du futur
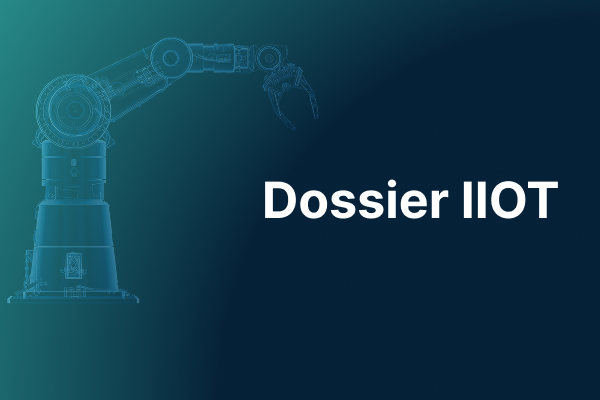
Découvrez Open-Prod au travers d'une présentation de 90 minutes, et découvrez comment un ERP adapté dédié aux entreprises industrielles peut transformer durablement vos processus pour vous permettre d'accroître vos performances.
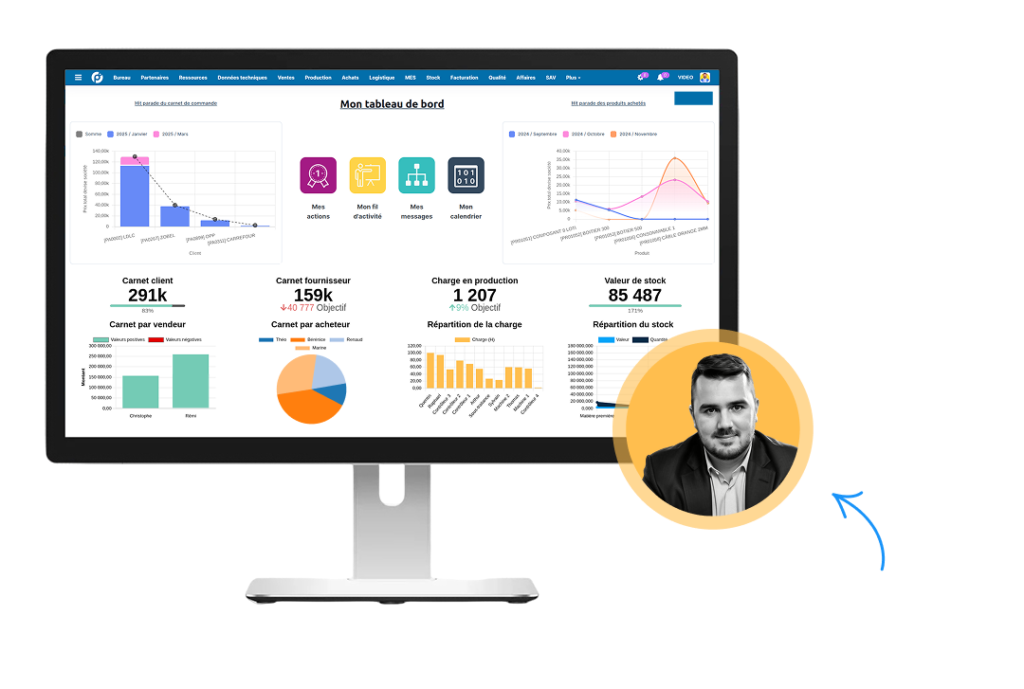