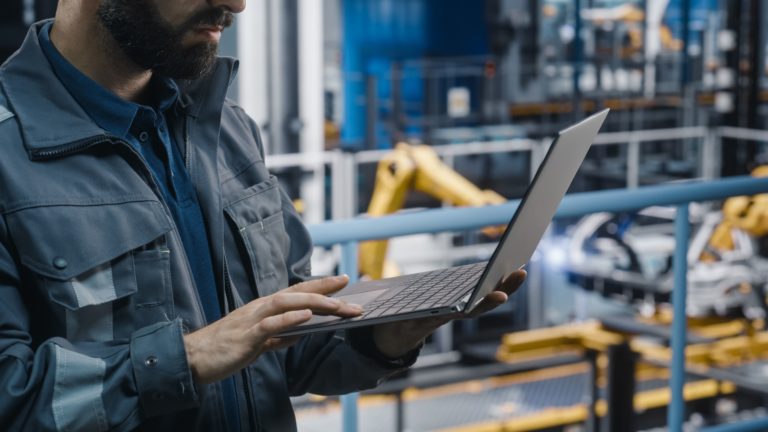
La maintenance industrielle : Garantir la performance optimale des équipements
Dans l'environnement industriel compétitif actuel, la disponibilité et la fiabilité des équipements constituent un avantage concurrentiel déterminant. Deux méthodologies se distinguent particulièrement dans ce domaine : la Total Productive Maintenance (TPM) et l'Analyse des Causes Racines (RCA). Ces approches complémentaires permettent aux entreprises de maximiser le rendement de leurs installations tout en minimisant les coûts associés aux pannes et dysfonctionnements.
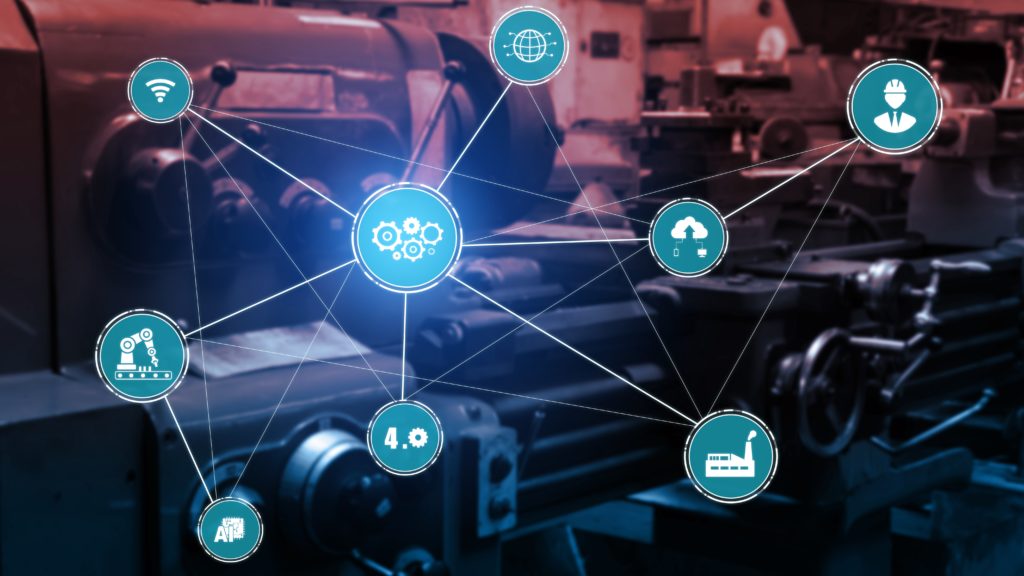
La TPM : Une approche globale de la maintenance
Principes et fondements
La Total Productive Maintenance (TPM) est une méthodologie développée au Japon dans les années 1970, notamment par Toyota, qui révolutionne l'approche traditionnelle de la maintenance. Contrairement aux méthodes classiques qui séparent production et maintenance, la TPM implique l'ensemble des acteurs de l'entreprise dans une démarche d'amélioration continue des équipements.
Le concept repose sur huit piliers fondamentaux :
- La maintenance autonome
- L’amélioration ciblée
- La maintenance planifiée
- La formation et l’éducation
- La maintenance préventive dès la conception
- La qualité maintenance
- La TPM dans les services administratifs
- La sécurité, l’hygiène et l’environnement
L'objectif ultime de la TPM est d'éliminer les "six grandes pertes" qui affectent l'efficacité des équipements : pannes, réglages, micro-arrêts, ralentissements, défauts et pertes au démarrage.
L'OEE : Mesurer pour améliorer
Au cœur de la TPM se trouve un indicateur clé de performance : l'Overall Equipment Effectiveness (OEE) ou Taux de Rendement Synthétique (TRS). Cet indicateur composite mesure l'efficacité globale d'un équipement en combinant trois dimensions essentielles :
- La disponibilité (ratio du temps de fonctionnement sur le temps disponible)
- La performance (cadence réelle par rapport à la cadence théorique)
- La qualité (proportion de produits conformes)
OEE = Disponibilité × Performance × Qualité
L'OEE permet non seulement de quantifier les performances actuelles, mais aussi d'identifier précisément les domaines d'amélioration prioritaires. Dans une entreprise de classe mondiale, l'OEE cible se situe généralement au-dessus de 85%.
Toute votre gestion d'entreprise
dans un seul outil.
Mise en œuvre et bénéfices
L'implémentation de la TPM suit généralement un processus structuré :
Phase préparatoire : Sensibilisation du management et formation des équipes
Introduction : Communication de la démarche à l'ensemble du personnel
Implémentation : Déploiement progressif des huit piliers
Les bénéfices d'une démarche TPM réussie sont multiples :
- Réduction significative des pannes (souvent 80% à 90%)
- Augmentation de la productivité (20% à 30% en moyenne)
- Diminution des défauts qualité
- Réduction des accidents de travail
- Engagement accru des opérateurs
- Diminution des coûts de maintenance
Des entreprises comme Procter & Gamble, Heineken ou ArcelorMittal ont obtenu des résultats spectaculaires grâce à la mise en œuvre rigoureuse de la TPM.
RCA : L'art de résoudre les problèmes à la source
Principes et méthodologie
L'Analyse des Causes Racines (Root Cause Analysis ou RCA) est une approche méthodique visant à identifier et corriger les causes fondamentales des problèmes, plutôt que de traiter simplement leurs symptômes. Particulièrement efficace dans le domaine de la maintenance industrielle, la RCA permet d'éviter la récurrence des pannes en s'attaquant à leur origine profonde.
La démarche RCA se déroule typiquement en cinq étapes :
- Définition du problème : Caractérisation précise de l’incident ou dysfonctionnement
- Collecte des données : Rassemblement exhaustif des faits et observations
- Identification des causes potentielles : Exploration systématique des facteurs contributifs
- Détermination des causes racines : Analyse approfondie pour isoler les facteurs fondamentaux
- Développement et implémentation des solutions : Actions correctives ciblées
Le diagramme d'Ishikawa : Un outil puissant
Parmi les nombreux outils utilisés dans le cadre d'une RCA, le diagramme d'Ishikawa (également appelé diagramme en arêtes de poisson ou diagramme de cause à effet) occupe une place prépondérante. Développé par Kaoru Ishikawa dans les années 1960, cet outil visuel permet d'organiser les causes potentielles d'un problème en catégories structurées.
Dans sa forme classique, le diagramme explore six dimensions (les "6M") :
- Main-d’œuvre (facteurs humains)
- Méthodes (procédures et processus)
- Machines (équipements)
- Matières (matières premières et consommables)
- Milieu (environnement de travail)
- Mesure (contrôles et indicateurs)
Cette approche systématique garantit qu'aucune piste potentielle n'est négligée lors de l'analyse.
Applications industrielles
La RCA trouve des applications dans de nombreux contextes industriels :
- Analyse post-panne d’équipements critiques
- Investigation suite à des incidents qualité récurrents
- Optimisation de processus sous-performants
- Résolution de problèmes de sécurité
Par exemple, dans une usine sidérurgique, une RCA menée suite à des ruptures fréquentes d'un convoyeur pourrait révéler que la cause racine n'est pas une défaillance mécanique (symptôme), mais une surcharge systématique due à un paramétrage incorrect du système d'alimentation (cause racine). Cette distinction permet d'implémenter une solution durable plutôt qu'un simple correctif temporaire.
Synergie entre TPM et RCA
Les approches TPM et RCA sont naturellement complémentaires et se renforcent mutuellement lorsqu'elles sont intégrées dans une stratégie globale de maintenance :
- La TPM fournit le cadre organisationnel et culturel propice à l’excellence opérationnelle
- La RCA apporte les outils analytiques nécessaires pour résoudre les problèmes complexes
Dans un environnement industriel mature, la RCA devient un composant essentiel du pilier "amélioration ciblée" de la TPM, permettant d'éliminer méthodiquement les causes de défaillances identifiées par le suivi de l'OEE.
L'évolution vers la maintenance prédictive
Si la TPM et la RCA constituent des approches éprouvées, l'avenir de la maintenance industrielle s'oriente de plus en plus vers les techniques prédictives. Grâce à l'Internet des Objets Industriel (IIoT), au big data et à l'intelligence artificielle, les entreprises peuvent désormais anticiper les défaillances avant qu'elles ne surviennent.
Ces technologies permettent de passer :
- D’une maintenance préventive systématique (basée sur le temps)
- À une maintenance conditionnelle (basée sur l’état)
- Puis à une maintenance prédictive (basée sur des modèles prédictifs)
Cette évolution ne remplace pas les méthodologies TPM et RCA, mais les enrichit en apportant de nouvelles capacités d'analyse et d'anticipation.
Conclusion
La maintenance industrielle moderne, portée par des méthodologies éprouvées comme la TPM et la RCA, constitue un levier stratégique de performance pour les entreprises manufacturières. Au-delà des aspects techniques, ces approches impliquent une transformation culturelle profonde, plaçant l'équipement au cœur des préoccupations de l'ensemble des acteurs de l'entreprise.
Dans un contexte d'industrie 4.0, l'intégration de ces méthodologies avec les technologies numériques avancées ouvre de nouvelles perspectives d'optimisation. Les entreprises qui parviendront à combiner efficacement l'expertise humaine et l'intelligence artificielle dans leur stratégie de maintenance seront les mieux positionnées pour maximiser la disponibilité de leurs équipements et, par conséquent, leur compétitivité globale.
Pour les responsables industriels, l'enjeu n'est plus simplement de réparer les pannes, mais de créer un environnement où les équipements peuvent fonctionner à leur plein potentiel, sans interruption non planifiée. C'est précisément ce que permettent d'accomplir la TPM et la RCA lorsqu'elles sont déployées avec rigueur et persévérance.
Découvrir nos autres dossiers
Retrouvez l’ensemble de nos articles sur l’IA, son rôle et ses enjeux dans l’industrie du futur
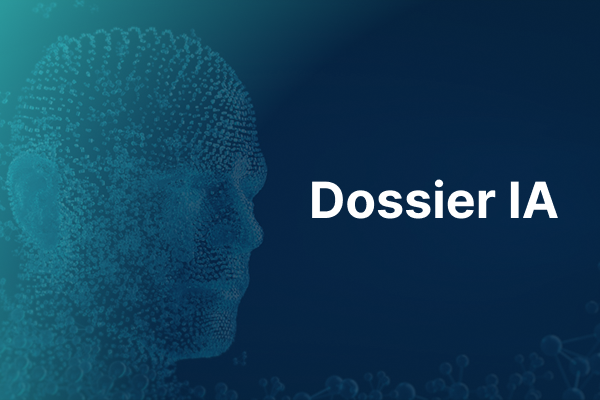
Retrouvez l’ensemble de nos articles sur l’IIoT, son rôle et ses enjeux dans l’industrie du futur
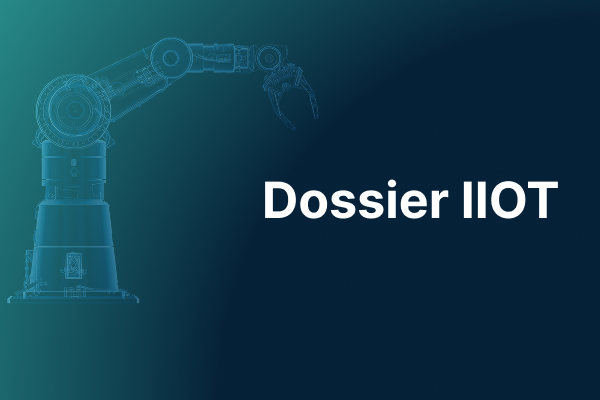
Découvrez Open-Prod au travers d'une présentation de 90 minutes, et découvrez comment un ERP adapté dédié aux entreprises industrielles peut transformer durablement vos processus pour vous permettre d'accroître vos performances.
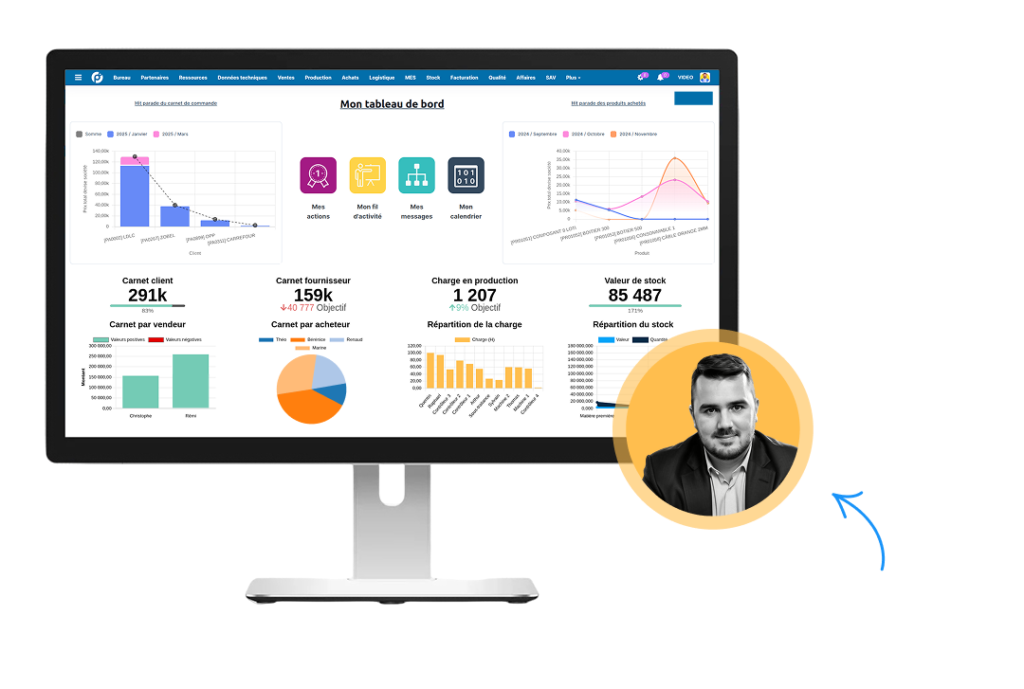