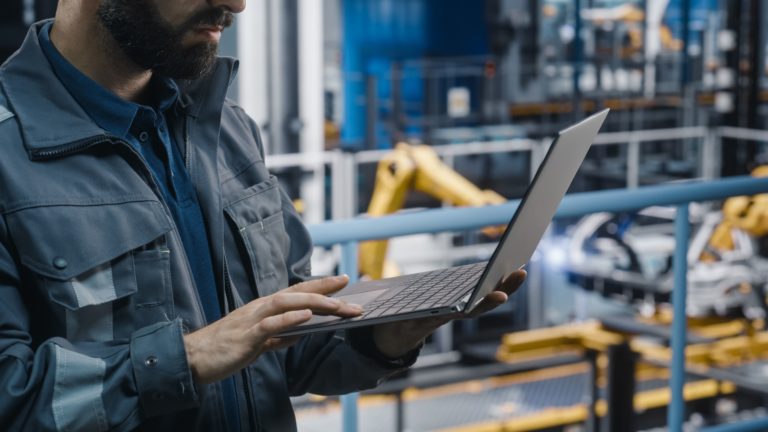
La gestion de la qualité dans l'industrie : Six sigma et SPC
La gestion de la qualité constitue un pilier fondamental dans l'optimisation des processus industriels. Deux méthodologies se distinguent particulièrement dans ce domaine : Six Sigma et le Contrôle Statistique des Processus (SPC). Ces approches permettent aux entreprises de garantir que leurs produits répondent systématiquement aux normes de qualité les plus exigeantes, tout en optimisant leurs ressources.
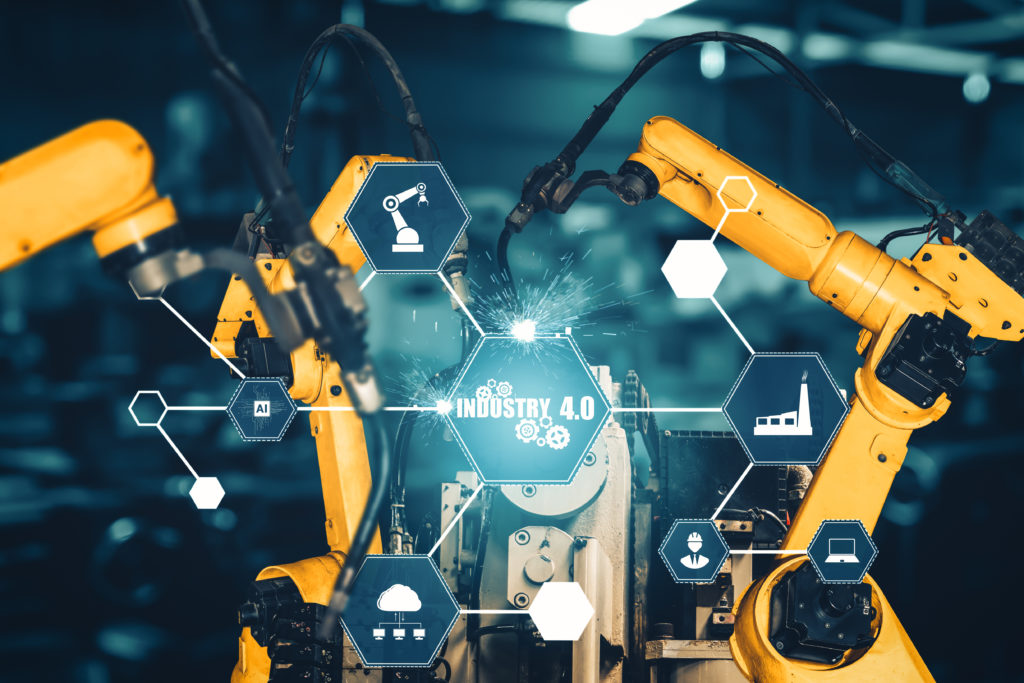
Six Sigma : L'excellence par la réduction des défauts
Principes fondamentaux
Six Sigma est une méthodologie rigoureuse développée initialement par Motorola dans les années 1980, puis popularisée par General Electric sous la direction de Jack Welch. Son objectif principal est de réduire drastiquement la variabilité et les défauts dans les processus de production.
Le terme "Six Sigma" fait référence à un niveau de performance où 99,99966% des produits sont exempts de défauts, ce qui correspond à seulement 3,4 défauts par million d'opportunités (DPMO). Pour atteindre ce niveau d'excellence, la méthode s'appuie sur une approche structurée et des outils statistiques avancés.
La méthodologie DMAIC
Au cœur de Six Sigma se trouve le processus DMAIC, un cadre d'amélioration en cinq étapes:
- Définir : Identification précise du problème, des attentes du client et des objectifs du projet
- Mesurer : Collecte de données fiables et évaluation des performances actuelles du processus
- Analyser : Utilisation d’outils statistiques pour identifier les causes racines des problèmes
- Améliorer : Développement et implémentation de solutions optimisées
- Contrôler : Mise en place de mécanismes pour maintenir les améliorations dans le temps
Cette approche systématique permet d'éliminer la subjectivité dans la résolution de problèmes en favorisant les décisions basées sur des données concrètes.
Outils et techniques associés
Six Sigma emploie un vaste arsenal d'outils analytiques pour l'amélioration des processus. Le diagramme de Pareto permet d'identifier les problèmes prioritaires en montrant que 80% des défauts proviennent souvent de 20% des causes. L'analyse des causes racines approfondit la compréhension des dysfonctionnements en remontant jusqu'à leur origine fondamentale. Les plans d'expériences structurent les tests pour évaluer l'impact de multiples variables simultanément, optimisant ainsi les processus complexes.
L'AMDEC (Analyse des Modes de Défaillance, de leurs Effets et de leur Criticité) anticipe les défaillances potentielles d'un produit ou processus. Les cartes de contrôle visualisent la stabilité des processus dans le temps, tandis que les analyses de capabilité mesurent leur aptitude à respecter les spécifications. Les tests d'hypothèses et analyses de régression complètent cet arsenal en validant statistiquement les relations entre variables et en construisant des modèles prédictifs fiables.
Applications industrielles
Six Sigma trouve des applications particulièrement pertinentes dans plusieurs contextes industriels critiques. Dans la résolution de problèmes qualité complexes et récurrents, cette méthodologie permet d'identifier et d'éliminer les causes profondes de défauts persistants qui résistent aux approches traditionnelles. Pour l'optimisation des processus de production à haute valeur ajoutée, Six Sigma offre un cadre structuré permettant d'atteindre des niveaux de performance exceptionnels dans des environnements où chaque défaut représente un coût significatif.
La méthode excelle également dans la réduction des coûts liés à la non-qualité (retours, reprises, rebuts, garanties) en attaquant systématiquement leurs sources. Enfin, Six Sigma améliore la satisfaction client en garantissant une qualité constante et prévisible des produits et services, réduisant ainsi les variations qui constituent la principale source d'insatisfaction. Des entreprises comme Toyota, Amazon et Honeywell ont intégré avec succès cette méthodologie pour transformer leurs opérations et atteindre l'excellence opérationnelle.
Toute votre gestion d'entreprise
dans un seul outil.
SPC (Statistical Process Control) : La maîtrise statistique des processus
Principes et objectifs
Le Contrôle Statistique des Processus (SPC) est une méthode de surveillance et de contrôle des processus de production basée sur des principes statistiques. Développée par Walter Shewhart dans les années 1920, cette approche part du principe qu'aucun processus n'est parfaitement stable et que des variations naturelles existent toujours.
L'objectif principal du SPC est de distinguer les variations normales (causes communes) des variations anormales (causes spéciales) pour intervenir uniquement lorsque nécessaire, évitant ainsi le sur-ajustement des processus.
Fonctionnement et implémentation
Le SPC repose principalement sur l'utilisation de cartes de contrôle, qui sont des représentations graphiques permettant de visualiser l'évolution d'un paramètre dans le temps par rapport à des limites statistiquement déterminées.
Le processus d'implémentation du SPC comprend généralement :
- La sélection des caractéristiques critiques à surveiller
- La collecte systématique de données d’échantillonnage
- Le calcul des limites de contrôle basées sur la variabilité naturelle du processus
- La création et l’analyse des cartes de contrôle
- La mise en place d’actions correctives en cas de détection d’anomalies
Types de cartes de contrôle
Différentes cartes de contrôle sont utilisées selon la nature des données :
- Cartes X-R : pour surveiller la moyenne et l’étendue de variables continues
- Cartes X-S : pour les grands échantillons, utilisant l’écart-type
- Cartes p et np : pour les attributs (conformes/non-conformes)
- Cartes c et u : pour le comptage de défauts
Avantages et applications
Le SPC offre plusieurs avantages majeurs dans la gestion de la qualité industrielle. La détection précoce des dérives constitue son principal atout, permettant d'identifier les anomalies avant qu'elles n'impactent la qualité finale des produits, réduisant ainsi les coûts de non-conformité. Cette approche proactive diminue considérablement le besoin d'inspections et contrôles en fin de production, ce qui représente une économie substantielle en temps et ressources.
En fournissant une base objective pour les décisions d'ajustement des processus, le SPC élimine les interventions arbitraires ou émotionnelles qui peuvent déstabiliser davantage les systèmes de production. De plus, l'utilisation systématique des cartes de contrôle crée une documentation continue et une traçabilité des performances des processus, facilitant les audits qualité et l'identification des tendances à long terme. Cette méthode est particulièrement efficace dans les industries de production continue comme l'agroalimentaire, la chimie, la pharmacie ou la métallurgie, où la stabilité des processus est cruciale.
Complémentarité des approches
Six Sigma et SPC ne sont pas mutuellement exclusifs mais plutôt complémentaires. Alors que le SPC se concentre sur la surveillance en temps réel des processus pour détecter rapidement les anomalies, Six Sigma offre un cadre plus large pour l'amélioration structurelle des processus et la résolution des problèmes complexes.
De nombreuses entreprises intègrent ces deux méthodologies dans un système global de gestion de la qualité. Le SPC assure une surveillance quotidienne des processus et génère des alertes immédiates lorsque des variations anormales sont détectées, permettant une intervention rapide pour maintenir la stabilité opérationnelle. En parallèle, Six Sigma intervient de manière plus approfondie pour résoudre les problèmes systémiques identifiés par le SPC, en s'attaquant aux causes fondamentales et en améliorant durablement la conception même des processus.
Cette synergie entre surveillance continue et amélioration structurelle permet d'établir une culture d'amélioration continue tout en maintenant une stabilité opérationnelle au quotidien. Les données collectées par le SPC alimentent naturellement les projets Six Sigma, tandis que les améliorations apportées par ces derniers se traduisent par des processus plus stables et plus faciles à surveiller via le SPC.
Conclusion
La gestion de la qualité à travers des méthodologies comme Six Sigma et SPC représente un investissement stratégique pour les entreprises industrielles. Au-delà de la simple conformité aux normes, ces approches offrent des avantages compétitifs significatifs en termes de réduction des coûts, d'amélioration de la satisfaction client et d'optimisation des ressources.
Dans un environnement économique où la qualité constitue un facteur différenciant majeur, la maîtrise de ces méthodologies devient un levier essentiel pour assurer la pérennité et la croissance des organisations manufacturières.
Découvrir nos autres dossiers
Retrouvez l’ensemble de nos articles sur l’IA, son rôle et ses enjeux dans l’industrie du futur
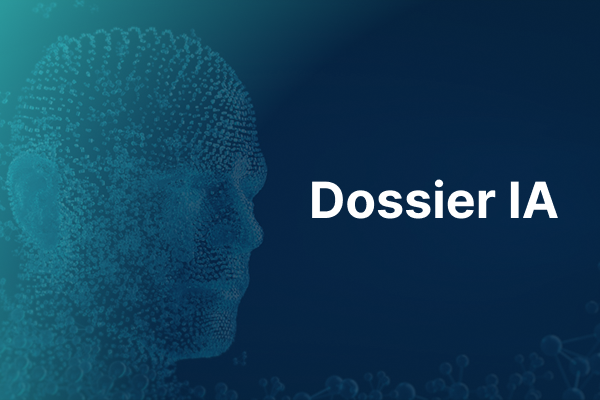
Retrouvez l’ensemble de nos articles sur l’IIoT, son rôle et ses enjeux dans l’industrie du futur
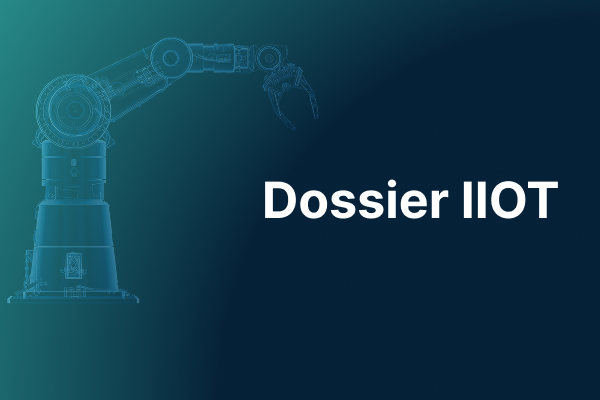
Découvrez Open-Prod au travers d'une présentation de 90 minutes, et découvrez comment un ERP adapté dédié aux entreprises industrielles peut transformer durablement vos processus pour vous permettre d'accroître vos performances.
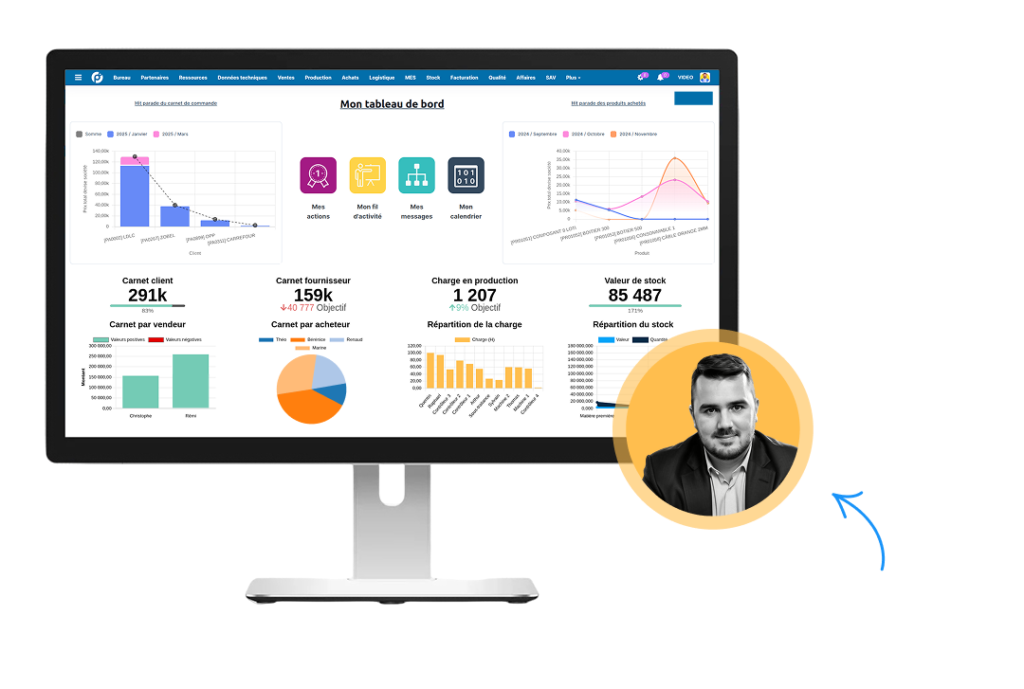