Technologies et digitalisation du pilotage industriel
L’industrie moderne est un organisme vivant. Chaque machine, chaque opérateur, chaque flux de production interagit dans un système complexe où l’efficacité dépend de la précision du pilotage. Mais ce qui faisait autrefois la force des ateliers – l’expérience, la planification rigoureuse, la réactivité humaine – ne suffit plus. La transformation numérique a bouleversé les règles du jeu.
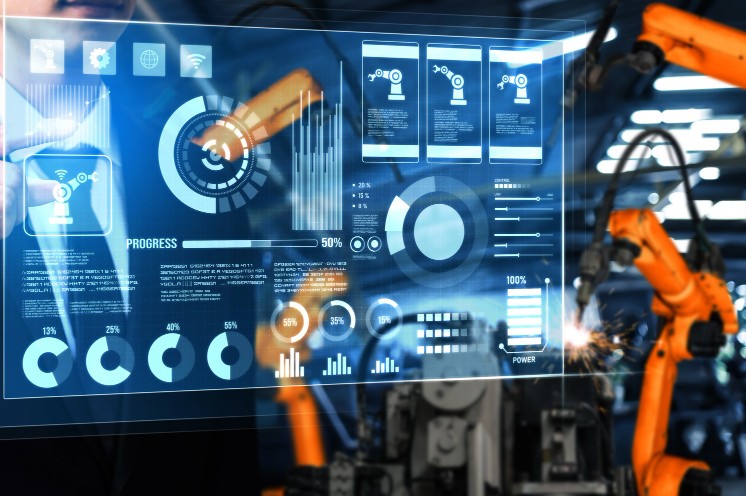
Aujourd’hui, l’usine ne fonctionne plus en vase clos. Elle est connectée, intelligente et capable d’anticiper les imprévus avant même qu’ils ne surviennent. Cette révolution repose sur un triptyque technologique incontournable : les systèmes MES intégrés aux ERP et GPAO, l’Internet des Objets pour le pilotage en temps réel et l’intelligence artificielle pour une production prédictive. Mais derrière ces promesses, un défi persiste : l’interopérabilité des systèmes.
MES et intégration ERP/GPAO : le cerveau de la production
Pendant longtemps, l’usine a fonctionné comme un archipel d’îlots technologiques. Chaque service – planification, production, logistique, maintenance – disposait de ses propres outils, souvent déconnectés les uns des autres. Puis est venu le temps des systèmes MES (Manufacturing Execution System), véritables chefs d’orchestre du pilotage industriel.
Un MES assure le lien entre l’ERP et l’atelier de production. Il collecte en temps réel les données issues des machines, des stocks, des opérateurs, puis ajuste instantanément les flux de production en fonction des objectifs définis. Intégré à un ERP/GPAO, il devient un levier stratégique. Là où un ERP structure l’ensemble des ressources de l’entreprise (achats, stocks, ressources humaines), le MES optimise la gestion des opérations en temps réel.
Avec des solutions comme Open-Prod, cette synergie prend tout son sens. Les industriels bénéficient d’une vue panoramique sur leurs processus, capables de réagir immédiatement aux incidents et d’affiner leur planification à la minute près. Loin des tableurs et des ajustements manuels d’autrefois, l’usine devient un espace où la prise de décision s’appuie sur des données fiables et instantanées.
Internet des Objets (IoT) et pilotage en temps réel : une usine qui parle
Imaginez une ligne de production où chaque machine, chaque convoyeur, chaque poste de travail dialogue en continu. Une pièce en cours d’usinage peut signaler un défaut avant même qu’il ne devienne critique. Une machine peut s’auto-diagnostiquer et demander une intervention de maintenance avant de tomber en panne. C’est exactement ce que permet l’Internet des Objets (IoT) dans l’usine connectée
Les capteurs intelligents installés sur les équipements industriels collectent une masse gigantesque d’informations : températures, vibrations, taux d’usure, consommation énergétique. Ces données sont transmises en temps réel aux systèmes de pilotage, qui les analysent et déclenchent des actions immédiates. Plus besoin d’attendre un rapport d’audit pour identifier une anomalie : tout est visible et ajustable en direct.
L’IoT transforme ainsi le rôle des opérateurs et des managers de production. Ils ne surveillent plus passivement des machines, mais interagissent avec elles, anticipant les incidents avant qu’ils ne deviennent des problèmes majeurs. Ce mode de fonctionnement réduit les arrêts de production, optimise l’utilisation des ressources et, surtout, améliore la qualité des produits finis.
Toute votre gestion d'entreprise
dans un seul outil.
Intelligence artificielle et prédictibilité de la production : anticiper l’inattendu
L’une des grandes promesses de l’intelligence artificielle (IA) en industrie est sa capacité à donner un coup d’avance aux industriels. Plutôt que de réagir aux incidents après qu’ils se soient produits, l’IA permet d’anticiper et d’éviter les interruptions.
Grâce au machine learning, les algorithmes analysent les schémas de production, détectent les variations anormales et prédisent les pannes avant qu’elles ne surviennent. Une entreprise utilisant l’IA peut, par exemple, ajuster sa maintenance en fonction des signaux faibles détectés sur ses équipements , , optimisant ainsi la durée de vie de ses machines tout en réduisant les coûts d’intervention.
Mais l’IA ne se limite pas à la maintenance prédictive. Elle révolutionne également la gestion des flux et des stocks en identifiant les goulots d’étranglement et en suggérant des optimisations en continu. Elle aide à prévoir la demande client avec une précision inédite, permettant d’adapter la production sans générer d’excédents ni de retards.
Cette capacité à anticiper et à ajuster la production en temps réel transforme radicalement la compétitivité des entreprises. Plus de surproduction, moins de gaspillage, une meilleure utilisation des ressources : l’IA devient l’alliée incontournable d’un pilotage industriel intelligent et agile.
Les défis de l’interopérabilité des systèmes : un langage commun pour l’usine
Si la digitalisation du pilotage industriel ouvre des perspectives incroyables, elle pose aussi un défi majeur : l'interopérabilité des systèmes machine learning. Car une technologie, aussi performante soit-elle, ne sert à rien si elle ne peut pas communiquer avec le reste de l’écosystème industriel.
Trop souvent, les entreprises se retrouvent avec des outils incompatibles : un ERP qui ne dialogue pas avec le MES, des capteurs IoT qui ne transmettent pas leurs données aux systèmes d’analyse, des machines anciennes incapables de s’intégrer aux nouvelles architectures numériques.
Les solutions émergent progressivement, avec des standards comme OPC-UA, conçu pour harmoniser les échanges entre équipements industriels. Mais la véritable transformation viendra d’une approche unifiée, où les outils sont conçus dès le départ pour être interconnectés.
Les ERP modernes, comme Open-Prod, intègrent déjà cette dimension, en facilitant la communication entre les différents systèmes via des API ouvertes et des protocoles universels. L’objectif est clair : offrir une vue unique et cohérente de l’ensemble des opérations, en éliminant les silos qui freinent encore trop souvent l’efficacité des industries.
Découvrez Open-Prod au travers d'une présentation de 90 minutes, et découvrez comment un ERP adapté dédié aux entreprises industrielles peut transformer durablement vos processus pour vous permettre d'accroître vos performances.
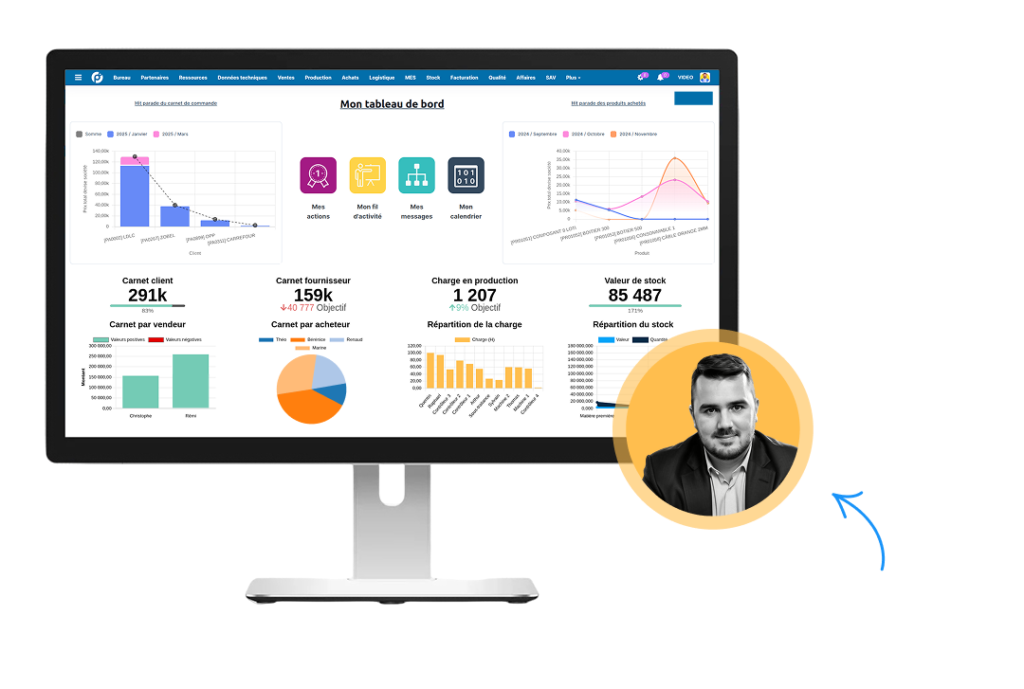
L’usine connectée : une révolution en marche
Le pilotage industriel entre dans une ère nouvelle, où la donnée devient le moteur de la performance. Les systèmes MES intégrés aux ERP, les capteurs IoT et l’intelligence artificielle permettent de piloter les usines avec une finesse et une réactivité inédites.
Mais cette transformation ne se fera pas en un jour. Le défi de l’interopérabilité reste à relever, et les entreprises doivent adopter une approche stratégique pour tirer pleinement parti de ces innovations. Une chose est certaine : dans l’industrie de demain, ceux qui sauront orchestrer ces technologies auront une longueur d’avance. Les autres risquent d’être laissés sur le bas-côté.
En savoir plus
Retrouvez l’ensemble de nos ressources pour accroître vos connaissances sur l’ERP pour le domaine industriel.
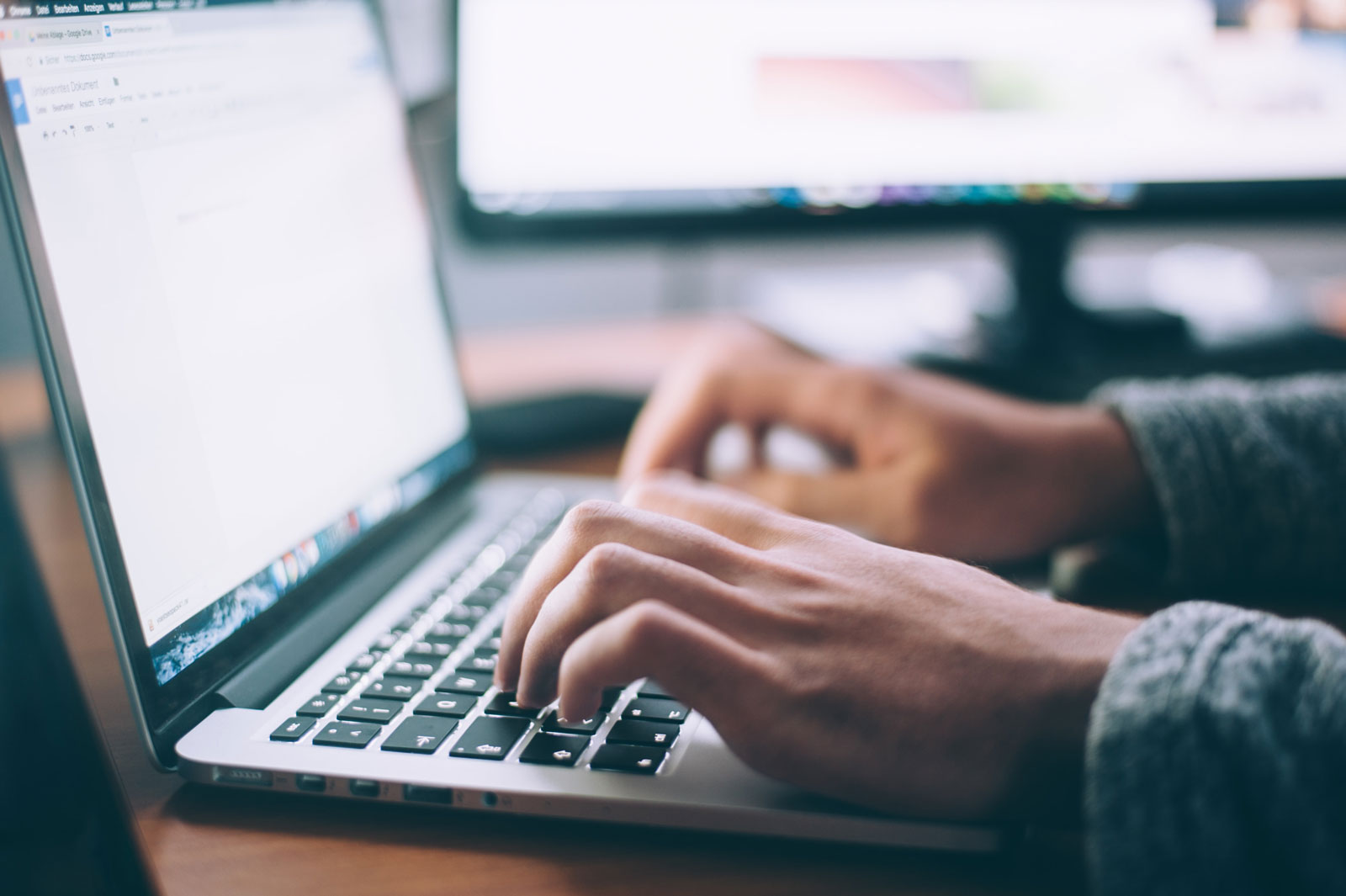
Retrouvez l’ensemble des réponses fonctionnelles de l’ERP Open-Prod aux différents secteurs industriels.
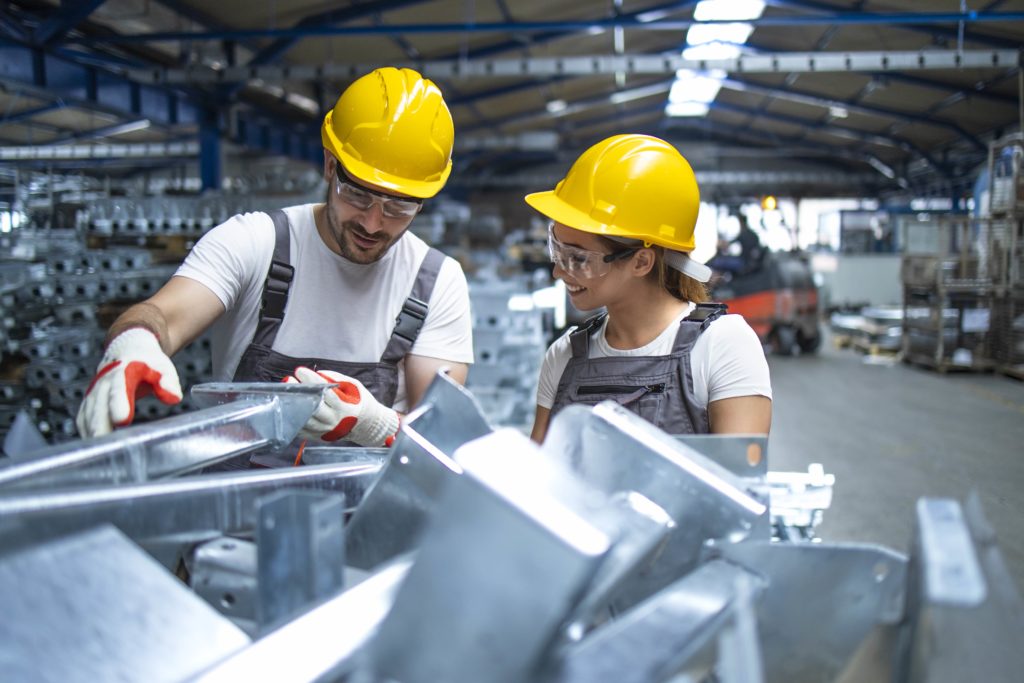
Découvrez les +200 modules d’Open-Prod conçus pour répondre aux besoins des entreprises industrielles.
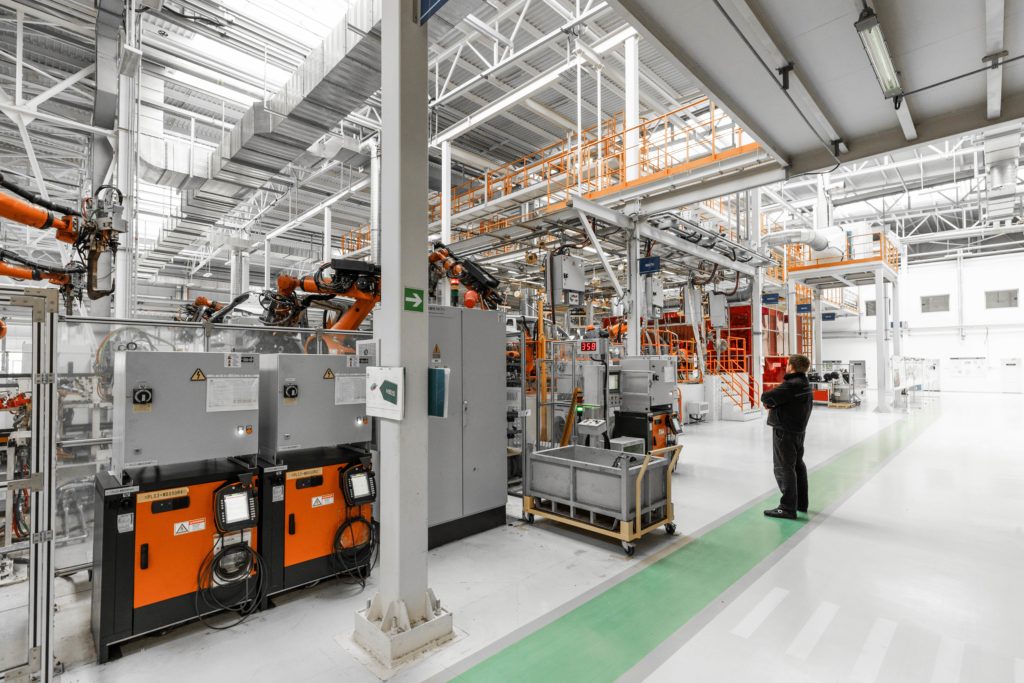