Le 5S : Un pilier fondamental de l'amélioration continue dans la production industrielle
Le 5S est une méthodologie japonaise qui s'est imposée comme un élément essentiel de l'amélioration continue dans le contexte de la production industrielle. Cette approche, simple mais puissante, vise à optimiser l'organisation du lieu de travail, à améliorer la productivité et à renforcer la qualité des produits et services. Le 5S tire son nom des cinq étapes qui le composent, chacune commençant par la lettre "S" en japonais : Seiri (trier), Seiton (ranger), Seiso (nettoyer), Seiketsu (standardiser) et Shitsuke (maintenir).
L'histoire du 5S remonte aux années 1950 au Japon, dans le contexte de la reconstruction industrielle d'après-guerre. Il a été développé comme une partie intégrante du système de production Toyota (TPS), qui visait à éliminer les gaspillages et à améliorer l'efficacité. Taiichi Ohno, l'un des architectes du TPS, a joué un rôle crucial dans la formalisation et la promotion de cette méthodologie. Au fil des décennies, le 5S s'est répandu bien au-delà des frontières japonaises pour devenir un standard mondial dans l'amélioration des processus industriels.
La première étape du 5S, Seiri (trier), consiste à identifier et à éliminer tous les éléments inutiles de l'espace de travail. Cela peut impliquer de se débarrasser d'outils obsolètes, de documents périmés ou de matériaux excédentaires. Par exemple, dans une usine automobile, cela pourrait signifier retirer des établis les outils qui ne sont plus utilisés pour le modèle de voiture en cours de production.
La deuxième étape, Seiton (ranger), vise à organiser efficacement les éléments nécessaires. Chaque objet doit avoir une place désignée, facilement accessible et clairement identifiée. Dans un atelier de production, cela pourrait se traduire par l'utilisation de tableaux d'outils ombragés où chaque outil a son emplacement prédéfini, permettant une identification rapide des outils manquants ou mal rangés.
Seiso (nettoyer), la troisième étape, implique un nettoyage régulier et approfondi de l'espace de travail. Ce n'est pas seulement une question d'apparence, mais aussi un moyen de vérifier l'état de l'équipement et de l'environnement de travail. Dans une usine agroalimentaire, par exemple, cette étape est cruciale pour maintenir les normes d'hygiène et identifier rapidement tout problème potentiel avec les équipements.
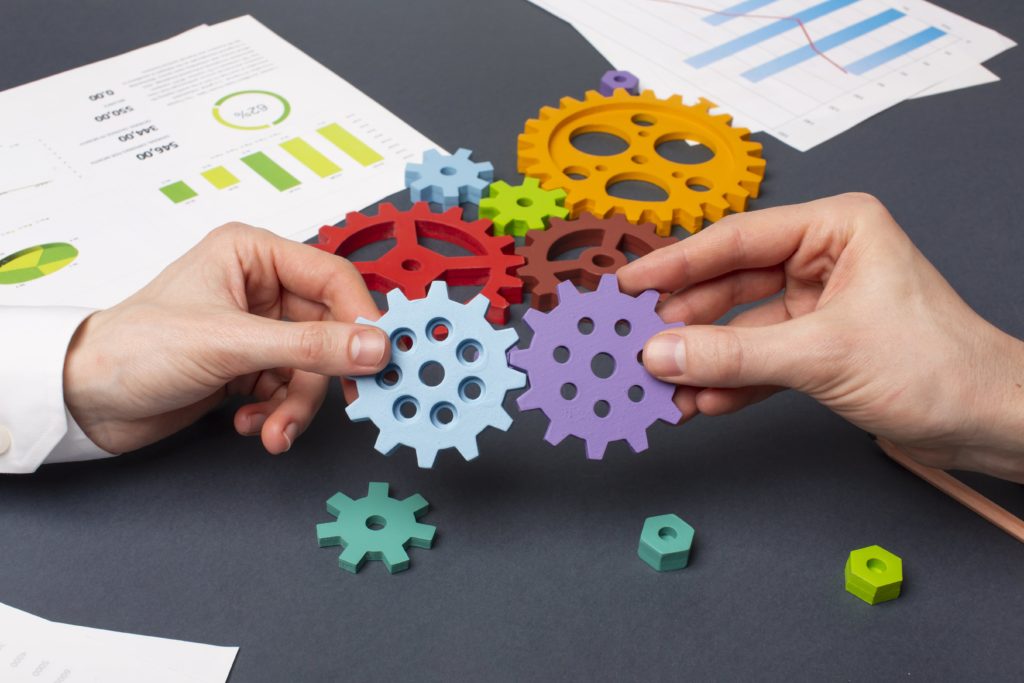
La quatrième étape, Seiketsu (standardiser), consiste à établir des procédures et des normes pour maintenir les trois premières étapes. Cela peut inclure la création de listes de contrôle, de procédures opérationnelles standardisées et de systèmes visuels. Dans une ligne d'assemblage de produits à destination de l'industrie médicale, cela pourrait se manifester par des instructions visuelles standardisées à chaque poste de travail, assurant une cohérence dans les méthodes de travail.
Enfin, Shitsuke (maintenir) vise à ancrer les pratiques 5S dans la culture de l'entreprise, en faisant de l'amélioration continue une habitude. Cela implique souvent des audits réguliers, des formations continues et des systèmes de récompense pour encourager l'adhésion au 5S. Une entreprise pourrait, par exemple, organiser des concours mensuels du "meilleur espace 5S" pour maintenir l'engagement des employés.
Les bénéfices du 5S sont nombreux et significatifs. Il permet d'améliorer la sécurité en réduisant les risques d'accidents liés au désordre ou à la mauvaise organisation. La productivité augmente grâce à la réduction du temps perdu à chercher des outils ou des informations. La qualité s'améliore car un environnement propre et organisé facilite la détection et la prévention des défauts. De plus, le 5S contribue à créer un environnement de travail plus agréable, ce qui peut avoir un impact positif sur le moral des employés.
Cependant, le 5S n'est pas sans limites ni défis. L'une des principales difficultés réside dans le maintien à long terme des pratiques 5S. Sans un engagement constant de la direction et des employés, les anciennes habitudes peuvent rapidement refaire surface. De plus, une application trop rigide du 5S peut parfois conduire à une sur-standardisation, limitant la créativité et la flexibilité nécessaires dans certains environnements de travail.
Toute votre gestion d'entreprise
dans un seul outil.
Un autre défi est la perception erronée que le 5S n'est qu'un simple exercice de nettoyage et de rangement. En réalité, c'est un changement culturel profond qui nécessite une compréhension et un engagement à tous les niveaux de l'organisation. Certaines entreprises peuvent également rencontrer des résistances de la part des employés qui perçoivent le 5S comme une critique implicite de leurs méthodes de travail actuelles.
Malgré ces défis, le 5S reste un outil puissant dans l'arsenal de l'amélioration continue. Son succès dans des entreprises de toutes tailles et de tous secteurs témoigne de sa versatilité et de son efficacité. Que ce soit dans une petite entreprise manufacturière ou dans un grand complexe industriel, le 5S offre un cadre simple mais robuste pour créer un environnement de travail plus efficace, plus sûr et plus productif.
En conclusion, le 5S est bien plus qu'une simple méthode d'organisation du lieu de travail. C'est une philosophie qui encourage une culture d'amélioration continue et de respect du lieu de travail. Bien que sa mise en œuvre puisse présenter des défis, les bénéfices potentiels en termes de productivité, de qualité et de satisfaction des employés en font un investissement précieux pour toute organisation cherchant à optimiser ses opérations et à rester compétitive dans un environnement industriel en constante évolution.
En savoir plus
Retrouvez l’ensemble de nos ressources pour accroître vos connaissances sur l’ERP pour le domaine industriel.
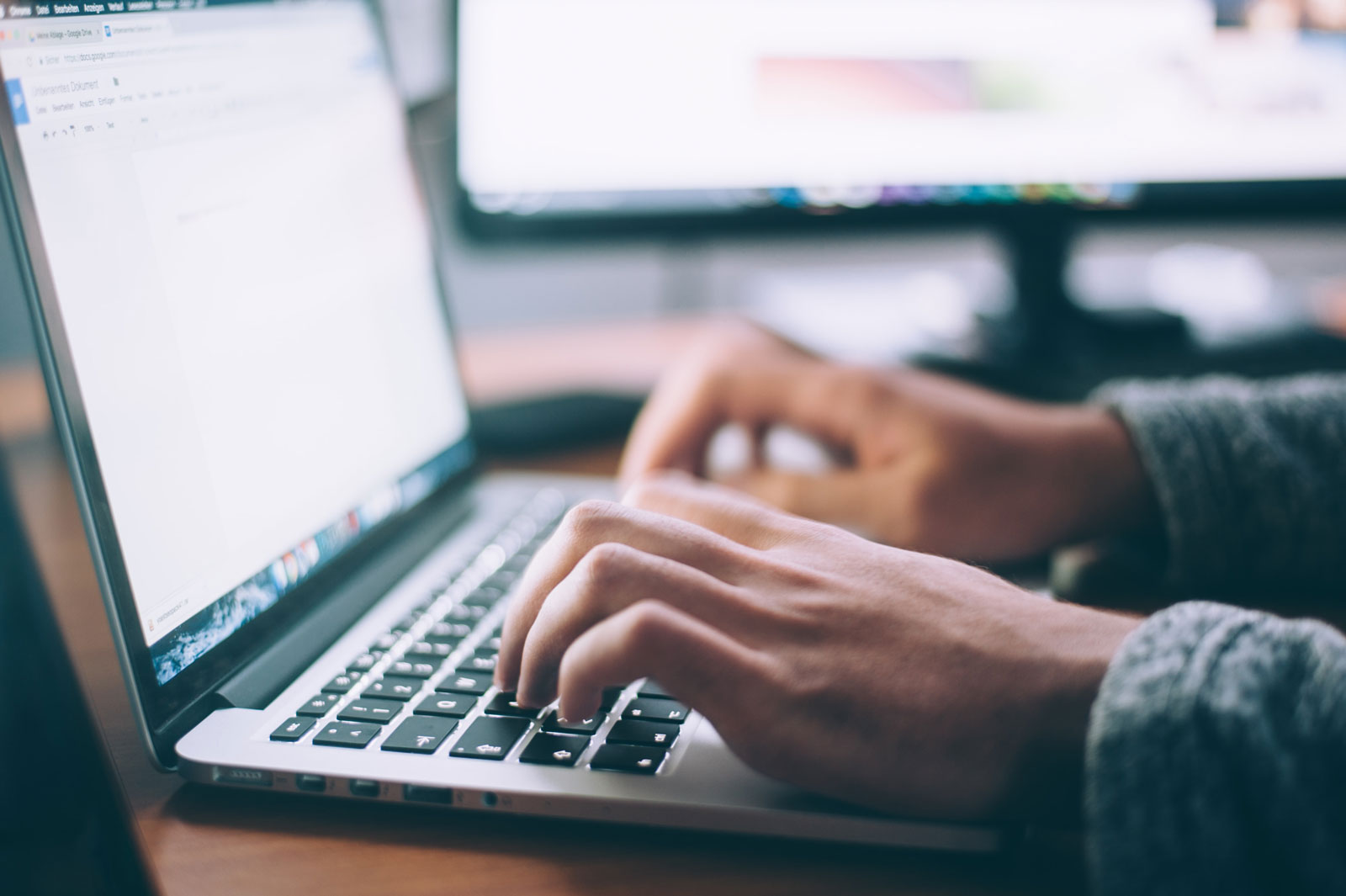
Retrouvez l’ensemble des réponses fonctionnelles de l’ERP Open-Prod aux différents secteurs industriels.
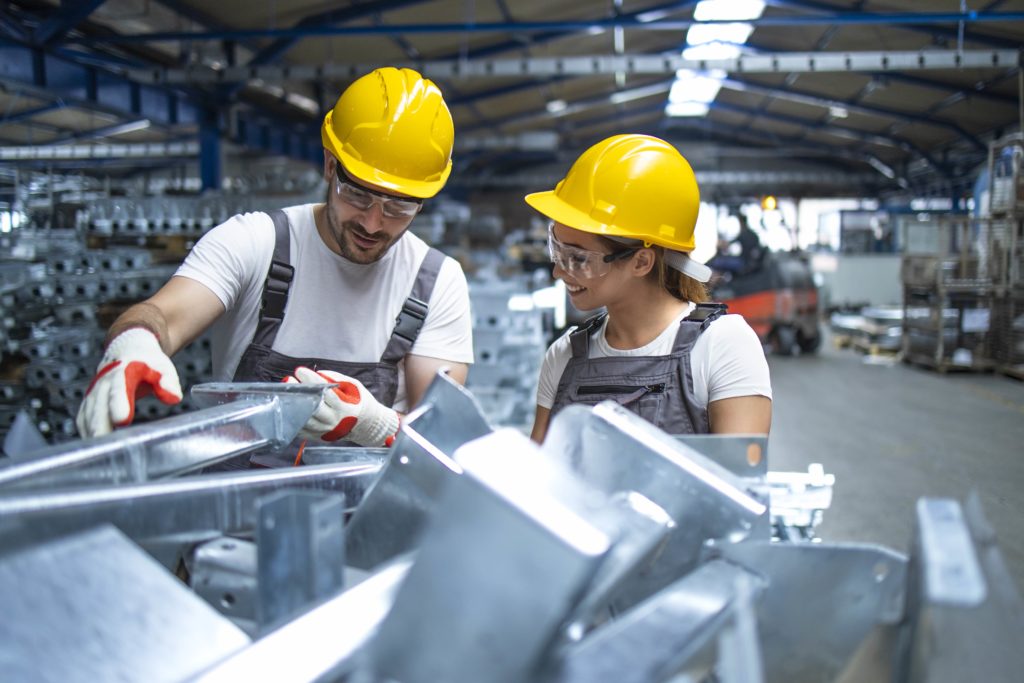
Découvrez les +200 modules d’Open-Prod conçus pour répondre aux besoins des entreprises industrielles.
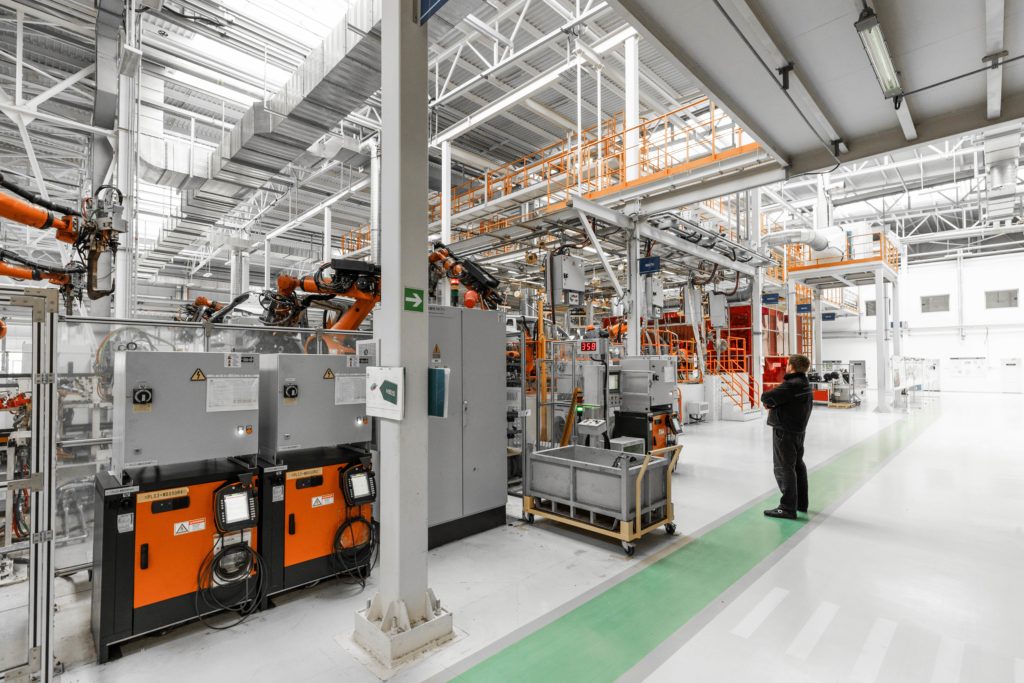