MES : Définition, objectifs et impact sur la gestion de la production industrielle
Le Manufacturing Execution System (MES) est un logiciel industriel qui assure le suivi, le contrôle et l’optimisation des processus de production en temps réel. Il constitue un maillon essentiel dans la transformation numérique des industries en offrant une visibilité complète sur l’atelier de production. Sa mission principale est d’assurer une exécution efficace des ordres de fabrication en connectant les données issues des machines, des opérateurs et des systèmes de planification.
Le rôle du MES dans l’optimisation des processus de production est déterminant. Il permet notamment de réduire les temps d’arrêt, d’optimiser l’utilisation des ressources et d’améliorer la qualité des produits finis en assurant un contrôle continu des opérations. Grâce à l’exploitation des données en temps réel, les industriels peuvent ajuster leur production en fonction des exigences du marché et détecter rapidement toute anomalie dans le processus de fabrication.
Le MES se distingue des autres systèmes d’information industriels, notamment de l’ERP (Enterprise Resource Planning). Alors que l’ERP est centré sur la gestion globale de l’entreprise (achats, stocks, ventes, comptabilité), le MES agit comme un système intermédiaire entre l’ERP et les équipements de production. Il garantit que les décisions prises au niveau de la planification stratégique sont exécutées de manière optimale sur le terrain, en assurant une traçabilité fine et une réactivité accrue.
Dans un contexte où l’industrie se digitalise et se modernise, le MES joue un rôle clé dans la mise en œuvre des principes de l’Industrie 4.0. Son interconnexion avec les machines intelligentes, les capteurs IoT et les systèmes de gestion avancés en fait un atout stratégique pour toute entreprise cherchant à améliorer sa compétitivité et à optimiser sa performance industrielle.
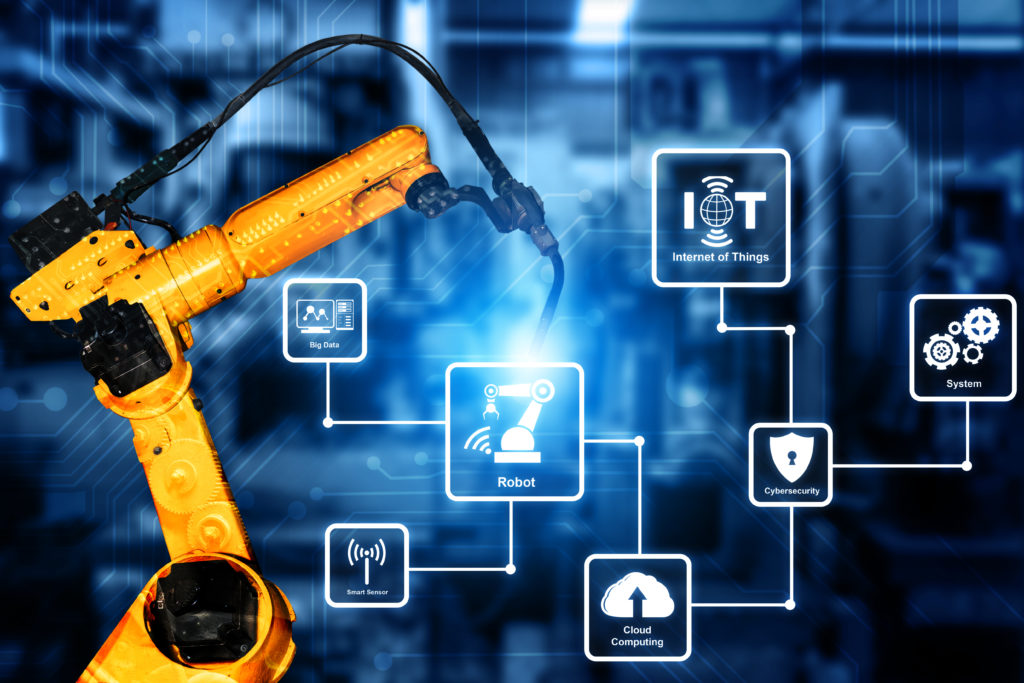
1. Les fonctions clés d’un MES
Le Manufacturing Execution System (MES) est un outil central pour l’optimisation des ateliers industriels, en offrant une gestion fine et automatisée des opérations de production. Il assure une supervision en temps réel des processus, garantissant ainsi une meilleure réactivité et une réduction des pertes. Ses principales fonctionnalités couvrent plusieurs aspects cruciaux de la gestion industrielle.
Suivi en temps réel de la production
Le MES collecte et analyse en continu les données des machines et des opérateurs. Grâce à l’intégration avec les capteurs IoT et les automates industriels, il fournit une visibilité instantanée sur l’état des équipements, les performances des lignes de production et l’avancement des ordres de fabrication. Cette surveillance permet aux industriels de réagir immédiatement en cas d’écart par rapport aux objectifs de production, réduisant ainsi les risques d’arrêts imprévus et améliorant la productivité globale.
Gestion des ordres de fabrication
L’un des rôles majeurs du MES est d’optimiser l’exécution des ordres de fabrication en tenant compte des priorités, des contraintes de ressources et des objectifs de performance. Il orchestre le déclenchement des opérations, l’assignation des tâches aux machines et aux opérateurs, et l’optimisation des flux de production pour garantir une efficacité maximale. Cette gestion dynamique permet d’adapter la fabrication en fonction des besoins réels et d’assurer une flexibilité accrue face aux variations de la demande.
Traçabilité et qualité
Le MES assure une traçabilité complète des matières premières, des composants et des produits finis tout au long du processus de fabrication. Chaque étape de transformation est enregistrée, permettant ainsi une reconstitution précise de l’historique de production. Cette capacité de suivi est particulièrement précieuse dans les industries soumises à des réglementations strictes, comme l’aéronautique, la pharmaceutique ou l’agroalimentaire. De plus, le MES intègre des outils de contrôle qualité, automatisant la détection des non-conformités et facilitant l’application des procédures correctives en temps réel.
Maintenance prédictive
Grâce à l’analyse avancée des données de production, le MES joue un rôle clé dans la réduction des temps d’arrêt en permettant une maintenance prédictive. En exploitant les données issues des machines (température, vibrations, cycles d’utilisation), il anticipe les risques de panne et déclenche des interventions préventives avant qu’un dysfonctionnement majeur ne survienne. Cette approche permet d’allonger la durée de vie des équipements, d’optimiser les plannings de maintenance et de limiter les interruptions non planifiées, qui sont souvent coûteuses pour les industriels.
Analyse des performances (OEE - Overall Equipment Effectiveness)
L’efficacité des équipements est un levier majeur d’amélioration de la productivité industrielle. Le MES mesure en continu l’OEE (Overall Equipment Effectiveness), un indicateur qui évalue la performance globale des machines en prenant en compte la disponibilité, la performance et la qualité. Cette analyse permet d’identifier les points de blocage, d’optimiser les cadences et d’engager des actions correctives pour maximiser le rendement. En fournissant des tableaux de bord détaillés et des analyses comparatives, le MES contribue à une amélioration continue et à une prise de décision éclairée.
L’intégration d’un MES dans un environnement industriel permet donc une maîtrise fine de la production, une meilleure coordination des opérations et une amélioration significative des performances. Il constitue un atout essentiel pour les entreprises cherchant à optimiser leurs coûts, renforcer leur compétitivité et accélérer leur transition vers l’Industrie 4.0.
2. Avantages du MES pour l’industrie
L’intégration d’un Manufacturing Execution System (MES) dans un environnement industriel transforme la gestion des opérations et optimise la production en s’appuyant sur des technologies avancées. Il constitue un levier stratégique pour les entreprises cherchant à accroître leur compétitivité tout en réduisant leurs coûts. Ses bénéfices se manifestent à plusieurs niveaux, allant de la réduction des gaspillages à l’amélioration de la traçabilité et de l’interconnectivité avec les autres systèmes industriels.
Réduction des coûts et des gaspillages (lean manufacturing)
Le MES s’inscrit pleinement dans les principes du lean manufacturing, en permettant d’identifier et d’éliminer les sources de gaspillage dans la production. Grâce à un suivi en temps réel des opérations et à une analyse fine des flux, il aide à réduire les temps d’arrêt, minimiser les pertes de matière première et optimiser l’utilisation des ressources. Il contribue ainsi à la mise en place d’un processus plus agile, où chaque étape de fabrication est optimisée pour maximiser la rentabilité et minimiser les coûts inutiles.
L’impact du MES sur la gestion des stocks est également crucial. En intégrant des outils de planification et de suivi précis, il permet d’éviter les ruptures de matières premières tout en limitant la surproduction. L’optimisation des en-cours et la synchronisation des approvisionnements avec la demande réelle conduisent à une réduction des stocks dormants et donc à une meilleure gestion financière des actifs de l’entreprise.
Amélioration de la productivité et de la qualité
En automatisant le suivi des performances et en facilitant la prise de décision, le MES permet aux industriels d’augmenter leur productivité sans nécessairement investir dans de nouveaux équipements. Il offre une visibilité détaillée sur le rendement des machines et des opérateurs, permettant d’ajuster en temps réel les cadences de production et d’optimiser les taux d’utilisation des ressources.
L’amélioration de la qualité est un autre bénéfice majeur du MES. En intégrant des outils de contrôle qualité automatisés, il détecte rapidement les écarts par rapport aux normes de fabrication et prévient la propagation des défauts sur l’ensemble de la chaîne de production. Cette réactivité contribue à réduire le taux de rebuts, à éviter les rappels de produits coûteux et à garantir un niveau de conformité optimal aux exigences réglementaires et aux attentes des clients.
Visibilité et traçabilité des opérations
Le MES fournit un historique détaillé de chaque lot de production, assurant une traçabilité complète des matières premières jusqu’au produit fini. Cette fonctionnalité est essentielle pour les secteurs industriels soumis à des normes strictes, comme l’aéronautique, la pharmaceutique ou l’agroalimentaire. En cas de problème de qualité, le MES permet d’identifier rapidement la source du dysfonctionnement et de prendre les mesures correctives appropriées.
Grâce à des tableaux de bord dynamiques et des indicateurs de performance en temps réel, les équipes industrielles disposent d’une vision claire et détaillée des opérations. Cette transparence améliore la réactivité face aux aléas de production et facilite la coordination entre les différents acteurs de la chaîne de valeur.
Connexion avec l’ERP et l’IIoT (Industrial Internet of Things)
L’un des atouts majeurs du MES réside dans sa capacité à s’intégrer avec les ERP (Enterprise Resource Planning) et les systèmes IIoT (Industrial Internet of Things). Cette interconnexion permet une synchronisation fluide entre la planification stratégique (ERP) et l’exécution opérationnelle (MES). L’ERP pilote les prévisions et les ressources, tandis que le MES veille à leur mise en œuvre efficace sur le terrain.
L’intégration avec l’IIoT amplifie encore l’efficacité du MES en exploitant les données en temps réel issues des capteurs et des équipements connectés. Cette synergie permet d’automatiser la collecte d’informations, d’améliorer la maintenance prédictive et d’optimiser l’utilisation des ressources énergétiques. Les entreprises bénéficient ainsi d’une usine intelligente et interconnectée, où chaque donnée devient un levier d’amélioration continue.
L’adoption d’un MES représente donc un investissement stratégique pour les industriels cherchant à renforcer leur compétitivité, gagner en agilité et assurer une production plus performante. En intégrant cette technologie, ils s’inscrivent pleinement dans la dynamique de l’Industrie 4.0, où l’optimisation des processus, la digitalisation et l’interconnexion des systèmes sont les piliers de l’usine du futur.
Toute votre gestion d'entreprise
dans un seul outil.
3. Déploiement d’un MES : Étapes clés
L’implémentation d’un Manufacturing Execution System (MES) est un projet stratégique pour une entreprise industrielle. Son déploiement doit être méthodique afin d’assurer une adoption efficace et un retour sur investissement optimal. Une mise en place réussie passe par plusieurs étapes clés, allant de l’analyse des besoins à l’évaluation continue de la performance du système.
Audit des besoins et définition des objectifs
Avant de choisir et d’implémenter un MES, il est essentiel de réaliser un audit détaillé des processus existants. Cette première phase permet d’identifier les points de blocage, les inefficacités et les opportunités d’amélioration. L’analyse porte sur plusieurs aspects :
- Les flux de production : quelles sont les étapes critiques nécessitant une automatisation ou une meilleure supervision ?
- Les besoins en traçabilité : quelles sont les exigences réglementaires et clients à respecter ?
- L’interopérabilité avec les systèmes existants : comment le MES s’intégrera-t-il avec l’ERP et les équipements industriels ?
À partir de cet audit, l’entreprise peut fixer des objectifs clairs et mesurables : réduction des pertes, amélioration du taux de rendement global (OEE), optimisation de la gestion des ordres de fabrication, digitalisation des suivis de production, etc. Ces objectifs serviront de référence pour évaluer la performance du système après son déploiement.
Intégration avec l’ERP et autres systèmes IT
Un MES ne fonctionne pas de manière isolée. Il doit être intégré aux autres systèmes d’information industriels, notamment l’ERP (Enterprise Resource Planning), la GPAO (Gestion de la Production Assistée par Ordinateur) et les plateformes IIoT (Industrial Internet of Things). Cette interconnexion permet une gestion fluide des données et une synchronisation en temps réel entre la planification et l’exécution des opérations.
L’intégration entre l’ERP et le MES assure une cohérence entre les décisions stratégiques et leur application en production. L’ERP pilote les aspects macroéconomiques (gestion des stocks, planification des ressources, suivi des coûts), tandis que le MES optimise la réactivité de l’atelier, en adaptant la production en fonction des contraintes opérationnelles.
Avec l’IIoT, l’intégration du MES permet une collecte automatisée des données issues des capteurs et machines connectées. Ces informations en temps réel facilitent la maintenance prédictive, le contrôle qualité automatisé et l’optimisation des performances énergétiques. Un bon déploiement repose donc sur une architecture IT bien définie et une interopérabilité maîtrisée.
Formation des équipes et accompagnement au changement
Le succès d’un projet MES repose sur l’adhésion des équipes de production et des responsables opérationnels. Une transformation digitale ne peut être efficace que si les opérateurs comprennent les bénéfices concrets du système et savent l’exploiter pleinement.
La formation est donc une étape clé du déploiement, et elle doit être adaptée aux différents profils d’utilisateurs :
- Les opérateurs : apprentissage des interfaces et des nouvelles procédures de suivi en temps réel
- Les responsables de production : exploitation des tableaux de bord et des indicateurs de performance pour ajuster les flux de travail.
- Les équipes IT : gestion technique du MES, interconnexion avec les autres systèmes et résolution des incidents.
Un accompagnement au changement est également nécessaire pour anticiper les résistances et favoriser une adoption rapide. La mise en place d’un support interne et d’un suivi post-déploiement permet de rassurer les équipes et de réajuster ’outil en fonction des retours terrain.
Suivi des KPI (Key Performance Indicators) pour mesurer le ROI
L’implantation d’un MES représente un investissement significatif, dont l’efficacité doit être évaluée en continu. Le suivi des indicateurs clés de performance (KPI) est essentiel pour mesurer le retour sur investissement (ROI) et ajuster le système si nécessaire.
Parmi les KPI les plus utilisés, on retrouve :
- Le Taux de Rendement Global (OEE – Overall Equipment Effectiveness) : il mesure la performance des équipements en prenant en compte leur disponibilité, leur efficacité et la qualité de production.
- Le taux de rebuts et de non-conformités : pour évaluer l’impact du MES sur l’amélioration de la qualité.
- La réduction des temps d’arrêt machine : indicateur clé pour mesurer l’efficacité de la maintenance prédictive.
- L’optimisation des cycles de production : permet d’évaluer si les gains de productivité annoncés sont bien atteints.
- La fiabilité des prévisions de production : grâce à l’intégration avec l’ERP, le MES doit permettre un meilleur ajustement de la planification industrielle.
Un suivi rigoureux de ces indicateurs permet de quantifier les gains réels, d’ajuster les paramétrages du système et d’optimiser progressivement les performances industrielles.
Un levier stratégique pour l’industrie 4.0
Le déploiement d’un MES est une étape clé de la transformation numérique des usines. Son implémentation doit être planifiée avec précision, en impliquant toutes les parties prenantes et en veillant à son intégration efficace avec les outils existants. Une approche méthodique garantit un ROI rapide, une amélioration continue des performances et une transition fluide vers l’Industrie 4.0.
Découvrez Open-Prod au travers d'une présentation de 90 minutes, et découvrez comment un ERP adapté dédié aux entreprises industrielles peut transformer durablement vos processus pour vous permettre d'accroître vos performances.
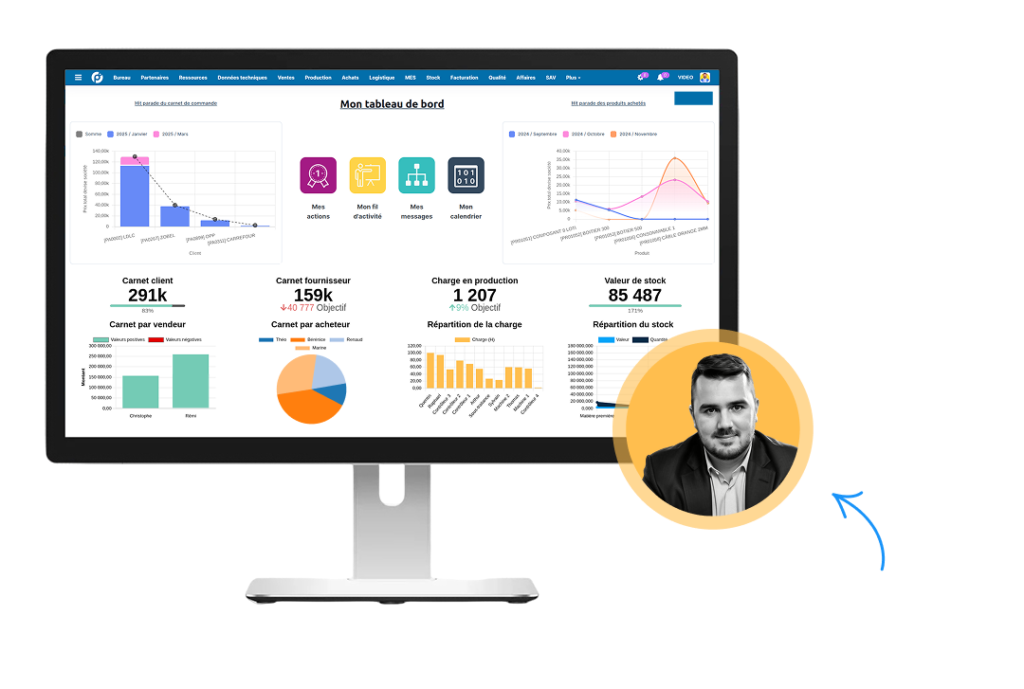
Conclusion : Le MES, un pilier essentiel de l’industrie 4.0
Le Manufacturing Execution System (MES) s’impose aujourd’hui comme un levier stratégique pour les entreprises industrielles cherchant à optimiser leurs processus de production et à renforcer leur compétitivité. Grâce à sa capacité à suivre en temps réel la production, à optimiser les flux de fabrication, à garantir la traçabilité des produits et à améliorer la maintenance des équipements, il constitue un élément central de la digitalisation des usines.
L’adoption d’un MES offre de multiples avantages, notamment la réduction des coûts et des gaspillages grâce aux principes du lean manufacturing, l’amélioration de la productivité et de la qualité des produits, ainsi qu’une meilleure visibilité et traçabilité des opérations. En intégrant l’Industrial Internet of Things (IIoT) et en se connectant à un ERP, il permet une gestion fluide des données et une synchronisation optimale entre la planification stratégique et l’exécution opérationnelle.
Son déploiement, cependant, requiert une approche méthodique. Une analyse approfondie des besoins, une intégration maîtrisée avec l’ERP et les autres systèmes IT, ainsi qu’un accompagnement au changement et une formation des équipes sont des étapes essentielles pour garantir son succès. Une fois en place, le suivi des KPI (Key Performance Indicators) permet d’évaluer le retour sur investissement (ROI) et d’optimiser en continu la performance du système.
Dans un contexte industriel en pleine transformation, marqué par la montée en puissance de l’Industrie 4.0, le MES apparaît comme un outil incontournable. Il ne se contente pas d’améliorer la productivité, mais permet aussi aux entreprises de gagner en agilité, d’anticiper les évolutions du marché et d’intégrer progressivement les technologies de demain. Loin d’être un simple logiciel de gestion de production, il est le socle d’une usine connectée, performante et tournée vers l’avenir.
En savoir plus
Retrouvez l’ensemble de nos ressources pour accroître vos connaissances sur l’ERP pour le domaine industriel.
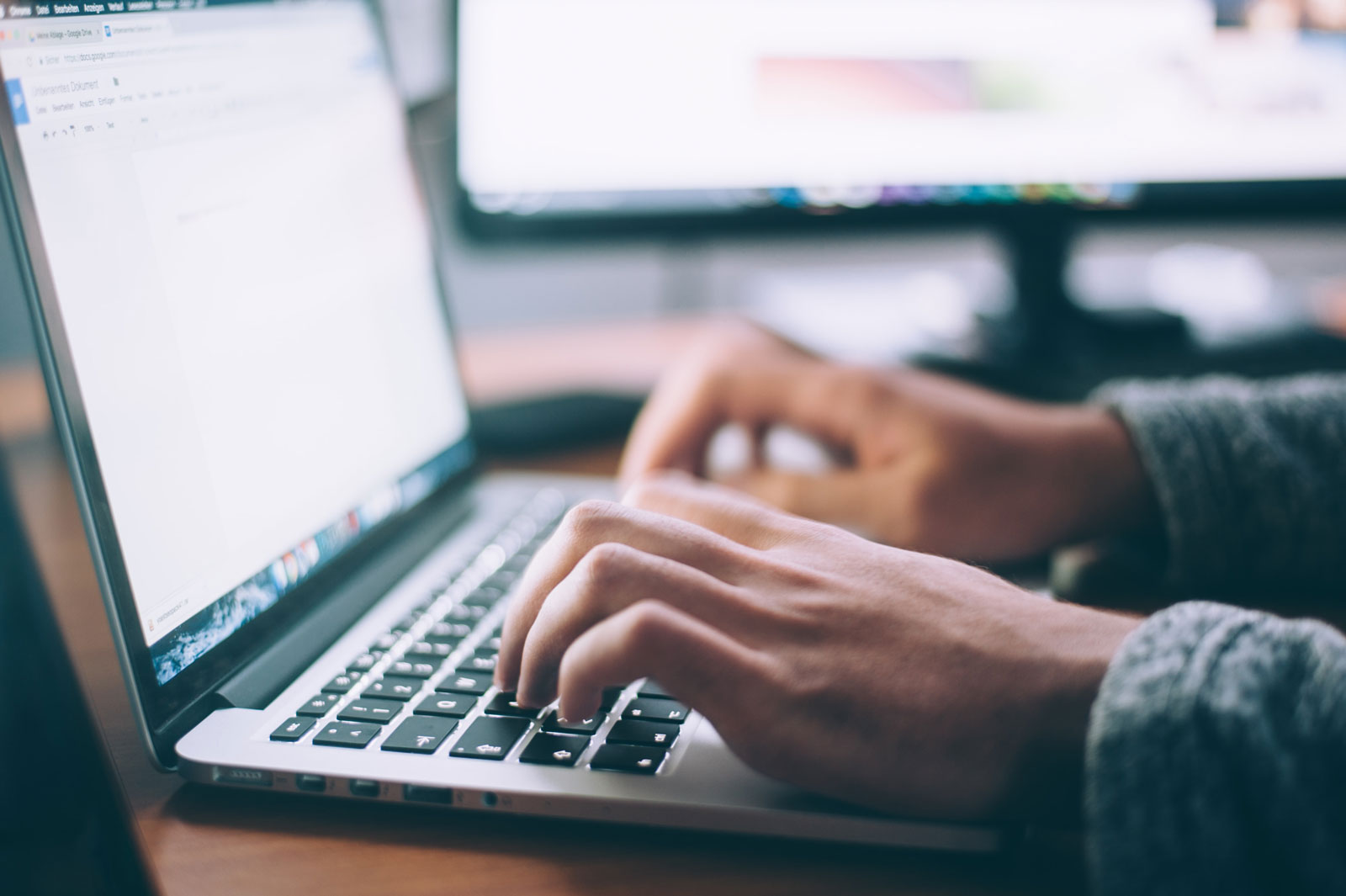
Retrouvez l’ensemble des réponses fonctionnelles de l’ERP Open-Prod aux différents secteurs industriels.
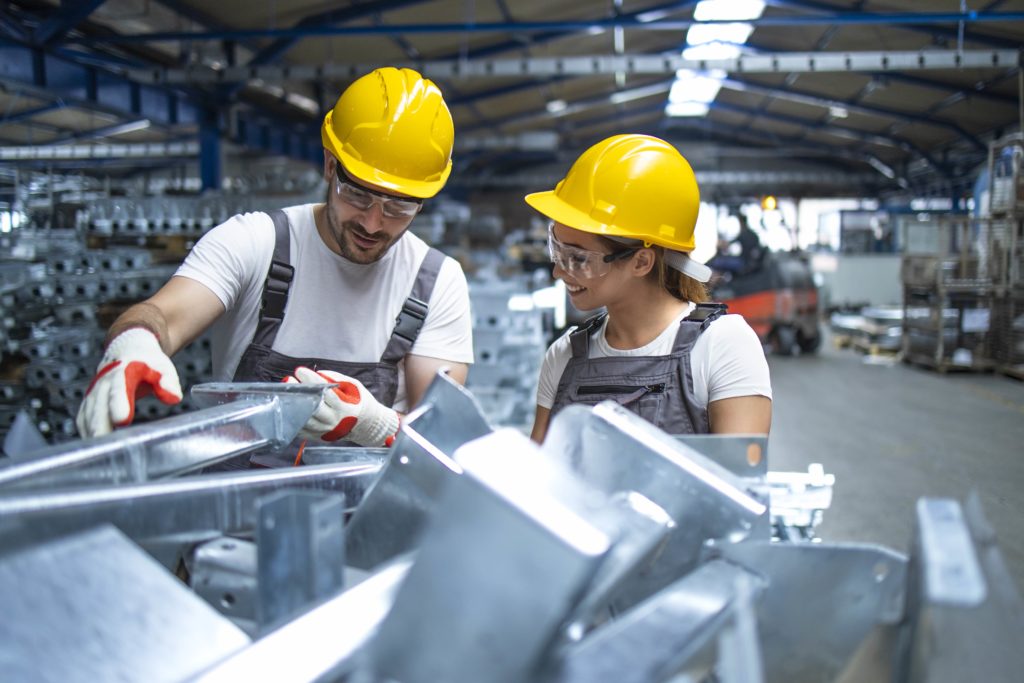
Découvrez les +200 modules d’Open-Prod conçus pour répondre aux besoins des entreprises industrielles.
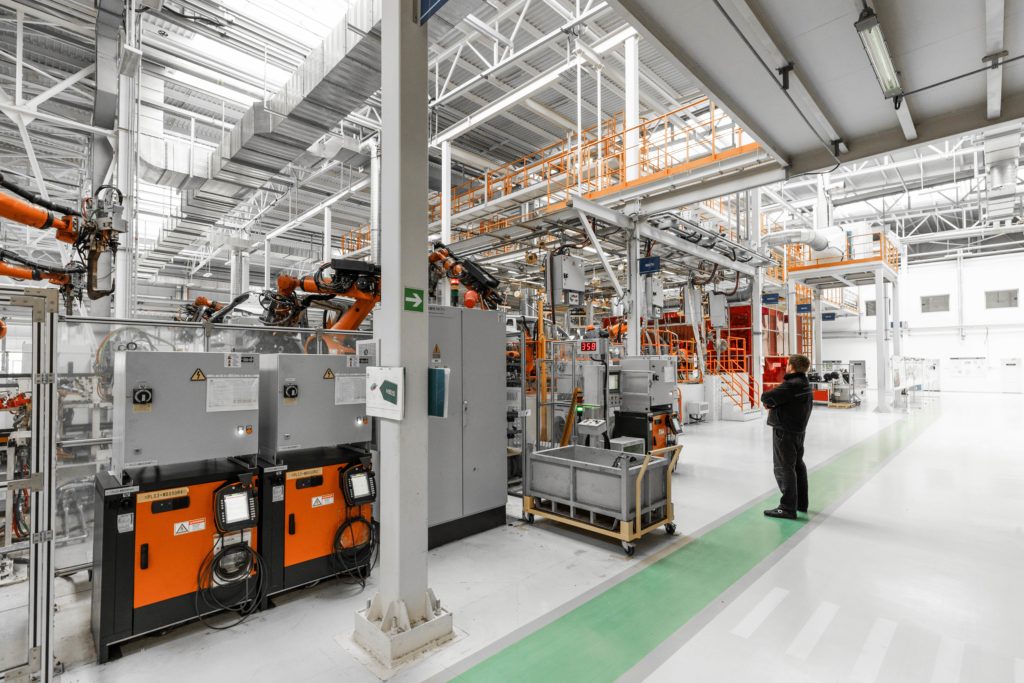